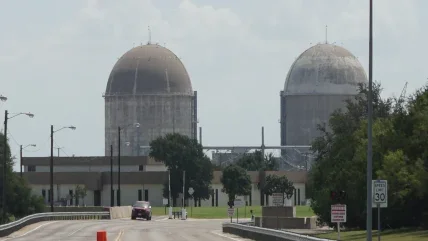
Vistra Operations Company, the operator of Comanche Peak nuclear power plant in Texas, has sought renewed operating licences for Comanche Peak 1 and 2. The company – acting both on its own behalf and on behalf of the plant owner, Comanche Peak Power Company – has submitted a formal application for licences that would add an additional 20 years to the plant lifetimes, bringing them up to 60 years each.
The existing licences for unit 1 and unit 2 expire on 8 February 2030 and 2 February 2033, respectively. The application for licence renewal – which requires no physical plant alterations or modifications – was submitted to the Nuclear Regulatory Commission (NRC) in October and was recently made public.
Comanche Peak 1 and 2 are sited 65 miles (108 km) southwest of Dallas-Fort Worth, Texas. Each unit is based on a four-loop Westinghouse Electric nuclear steam supply system. They are among the youngest of the USA’s fleet of nuclear stations – commercial operation began at Unit 1 on 13 August 1990 and Unit 2 on 3 August 1993. They were followed by Watts Bar 1 and 2. Each reactor was initially operated at a rated thermal power of 3411 MWt, but by 2008, the two units were each producing 3612 MWt after a series of upratings. As a consequence, electricity output has also been increasing; Unit 1 was uprated in autumn 2008 from 1,210 MWe to 1,259 MWe and Unit 2 was uprated in autumn 2009 from 1,208 MWe to 1,245 MWe.
At that time it was thought that additional units could potentially be built at the site. Vistra subsidiary Luminant formed a joint venture with Mitsubishi Heavy Industries for this purpose and in 2008 they jointly applied for a combined construction and operating licence from NRC, planning to build two 1,700 MW advanced PWRs of a Mitsubishi design. However, that application was suspended in 2013 when falling gas prices and the build out of wind in Texas hollowed out the financial case for expansion at the site. Meanwhile MHI shifted its focus to restarting its Japanese reactors following the Fukushima event. The application has not, however, been withdrawn although Vistra’s focus is now on gaining a new and substantially longer licence for the existing plant.
Preparing for the period of extended operation
In order to prepare for the licence renewal application, the plant operator carried out a scoping and screening process to define which systems and structures were relevant for the renewed licence. These systems and structures were grouped into the following areas:
- Reactor vessel, internals and reactor coolant system
- Engineered safety features
- Auxiliary systems
- Steam and power conversion systems
- Containments, structures and component supports
- Electrical, instrumentation and control systems
Typical aging effects that require management in these groups of components are cracking, cumulative fatigue damage, change in dimension, loss of fracture toughness, loss of material, reduction of heat transfer or wall thinning.
There are several general safety issues currently under scrutiny by the US Nuclear Regulatory Commission (NRC) and designated as ‘active or unresolved’. Four of these that may apply to the units at Comanche Peak are as follows:
- ‘Multiple steam generator tube leakage’ has been incorporated into the steam generator programme. It covers inspection requirements for steam generator tubes.
- ‘Fatigue evaluation of metal components for 60-year plant life’, concluded that licensees should address the effects of reactor coolant environment on component fatigue life as aging management programmes are formulated in support of licence renewal.
- ‘Assessment of debris accumulation on PWR sump performance’ addresses the potential for blockage of containment sump strainers that filter debris from cooling water supplied to the safety injection and containment spray pumps following a postulated loss of coolant accident. The issue is based on the identification of new potential sources of debris, including failed containment coatings, which may block the sump strainers.
- ‘Boral degradation’ addresses the potential for spent fuel racks that use Boral for neutron absorption experiencing problems with swelling and degradation of the plates over long periods of time.
Aging management programmes
Plant safety and efficiency are managed via a series of aging management programmes (AMPs) focused on specific components or systems. There are four types of aging maintenance programmes:
- Prevention programmes that stop the effects from occurring
- Mitigation programmes that slow the effects of aging
- Condition monitoring programmes that examine the presence and extent of aging
- Performance monitoring programmes that test the ability of a structure or component to perform its intended function.
In preparing for any licence renewal application, existing programmes and activities that apply to systems, structures, components, or commodity groups are reviewed because they are often based on a regulatory commitment or requirement, rather than specifically designed for aging management.
At Comanche Peak the renewal application says that many of these programmes had the required attributes and adequately manage aging effects. However, the plant operator will introduce several new ageing management programmes for the purposes of licence renewal. They are:
- Thermal aging embrittlement of cast austenitic stainless steel (CASS). This includes a screening methodology to determine component susceptibility to thermal aging embrittlement based on casting method, molybdenum content and ferrite percentage. For “potentially susceptible” components, thermal aging embrittlement management is accomplished through plant-specific flaw tolerance evaluations. Inspections or evaluations are not required for components that are determined not to be susceptible to thermal aging embrittlement. Three reactor coolant loop components are susceptible to thermal aging embrittlement in Unit 1 – a crossover leg 40-degree elbow, a crossover leg 90-degree elbow, and a crossover 90-degree elbow with plenum. A plant-specific flaw evaluation using plant-specific geometry and stress information was completed for all three of the components and it was determined that even with thermal aging, the susceptible CASS components are flaw tolerant for 60 years of service.
- PWR vessel internals. The new aging management plan is used to manage the effects of age-related degradation mechanisms that are applicable to reactor vessel internal components. These degradation mechanisms include: cracking due to stress corrosion and fatigue or cyclic loading; loss of material induced by wear; loss of fracture toughness due to thermal aging and neutron irradiation embrittlement; change in dimension due to void swelling or distortion; and loss of preload due to thermal and irradiation-enhanced stress relaxation and creep.
- One-time inspection will verify the system-wide effectiveness of the existing water chemistry, fuel oil chemistry and lubricating oil analysis AMPs. It will inspect a representative sample of components, which is 20% of the population, and if possible it will include components most susceptible to aging, due to their time in-service or the severity of operating conditions at their location.
- Selective leaching requires one-time inspections to demonstrate the absence of selective leaching. As above, it will be applied to a representative sample of susceptible components such as piping, valve bodies, pump casings, heat exchanger components and bolting. The materials of construction for these components that are susceptible to selective leaching are grey cast iron, ductile iron and copper alloy with greater than 15% zinc or 8% aluminium. The inspection of 20% of susceptible components will include visual examinations, supplemented by hardness tests or other mechanical examination techniques such as destructive testing, scraping, or chipping of selected components.
- One-time inspection of small-bore piping and inspection of internal surfaces in miscellaneous piping and ducting components. This AMP will incorporate volumetric inspections of a sample of this Class 1 piping focused on full and partial penetration welds. It will include measures to verify that degradation is not occurring, thereby either confirming that there is no need to manage age-related degradation or validating the effectiveness of any existing AMP for the period of extended operation.
- Internal surfaces in miscellaneous piping and ducting components. This AMP will manage loss of material, cracking, hardening and loss of strength and reduction of heat transfer using representative sampling and opportunistic visual inspections of the internal surfaces of metallic and elastomeric (including polymeric) components.
- Accessible power cables will be visually inspected for cable and connection jacket surface anomalies such as embrittlement, discoloration, cracking, melting, swelling or surface contamination that could indicate electrical insulation degradation. The first inspection for licence renewal will be completed prior to the period of extended operation and there will be recurring inspections performed at least once every 10 years thereafter.
- Internal portions of metal enclosed buses (bus enclosure assemblies) will be inspected for cracks, corrosion, foreign debris, excessive dust build-up and evidence of water intrusion. The bus electrical insulation material will be inspected for signs of reduced insulation resistance, radiation induced oxidation, moisture or debris intrusion or ohmic heating, as indicated by embrittlement, cracking, chipping, melting, discolouration or swelling.
Absorbing operational experience
A key process to manage aging effects in nuclear power plants is to make use of operational experience at the power plant and across the industry.
Operational experience is used at Comanche Peak to enhance existing programmes, prevent repeat events and prevent events that have occurred at other plants. To achieve this, plant personnel screen, evaluate and act on documents and information from outside sources to prevent or mitigate the consequences of similar events. The operator draws on external sources including Institute of Nuclear Power Operations (INPO) and NRC documents. Relevant foreign and domestic research and development programmes are also reviewed. Relevant research and development sources include: industry consensus standards development organisations; EPRI; communications issued by NRC staff based on research conducted by national labs used by the NRC; and nuclear vendor and owner’s groups.
Experience, including that involving age-related degradation, is tracked. Adverse trends are entered into the corrective action programme, as appropriate, for evaluation. If experience is identified as potentially involving aging it is evaluated with regard to systems, structures and components, materials, environments, aging effects and aging mechanisms. It will also be evaluated with regards to aging management programmes, which have an established performance feedback mechanism in place.
In its application Vistra Operations said this process, in conjunction with the corrective action programme, had proven to be effective in learning from adverse conditions and events, and improving programmes that address age-related degradation. However, to provide additional assurance that internal and external operating experience related to aging management is used effectively – including NRC and industry guidance documents and standards – Comanche Peak will enhance its programme to:
- Require the review of internal and external experience for aging-related degradation or impacts to aging management activities, to determine if improvements to aging management activities are warranted.
- Provide procedural guidance for identifying and reviewing experience. This will aim to identify aging that is in excess of what would be expected, relative to design, previous inspection experience and the inspection intervals.
- Establish coding for use in identification, trending, and communications of aging-related degradation.
- Establish guidelines for reporting plant-specific operational experience on age-related degradation and aging management to the industry.
- Provide training, on a periodic basis, to those responsible for AMP implementation and those responsible for reviewing, evaluating, and communicating operational experience items related to aging management and aging-related degradation.
This will begin as soon as renewed operating licences are issued and will continue throughout the remaining plant lifetime.
Abandoned engineering
Any power plant in its fourth decade will have seen a number of its systems upgraded or replaced. In some cases the most suitable fate of the original system has been to remain in place, capped, closed or otherwise made safe for the remainder of the plant lifetime. Comanche Peak has several such abandoned systems:
- The chemical feed system for steam generators in Unit 1 was removed from service when the new steam generators were installed. The remaining Unit 1 chemical feed recirculation components (pumps, piping, pipe supports and instrumentation) have been disconnected, capped and abandoned in place. The reverse osmosis system portion of the liquid waste processing system is not used at either unit at Comanche Peak and many of the systems’ associated components have been abandoned in place.
Also abandoned in place are:
- The jockey fire pump and diesel-driven fire pump
- Electric hydrogen recombiners
- A boron concentration measurement system
- A waste baling system in unit 1 that forms part of the solid waste management system.
- Portions of the potable and sanitary water system
- Some exhaust dampers considered to be part of the safeguards building ventilation system are abandoned in place in the open position.