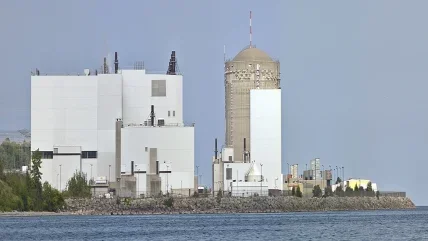
After more than 30 years of operations, some components of the four CANDU reactors at the Darlington Nuclear Power Plant in Ontario, Canada, had reached the end of their scheduled service life and were due for replacement. This refurbishment programme began in October 2016 but there had been more than a decade of planning beforehand to ensure the programme was flawlessly executed. The first unit to be shut down for replacement was Unit 2, which was subsequently put back into service in June 2020. However, even after the years of planning were completed, with three more reactor component replacements to complete over the course of a decade, key to keeping the project on time and on budget was the ability to take learnings from one unit and apply them to subsequent reactor replacements.
“We did Unit 2 independently so we could learn all the lessons from that programme,” explains Gary Rose, Vice President of New Nuclear Growth at Ontario Power Generation. “We then started Unit 3, applied all those lessons and we’ve seen some great success,” he adds.
In the latest update on the project, Ontario Power Generation (OPG) announced that the static commissioning for the turbine control modifications was complete and work is progressing through final field changes and software upgrades. To date, more than 90% of the work on Unit 3 is now complete. Following regulatory approvals return-to- service activities will begin and the reactor is scheduled to begin operations in the second half of 2023. “We started on
Unit 3 in September 2020 and are nearing completion of that. It will probably return to service in the middle of this year. That will be ahead of schedule,” says Rose. Indeed, at the end of 2022, Unit 3 saw 6,240 bundles of new fuel loaded into the reactor following completion of the lower feeder tube installation.
In a unique development for OPG, both Units 1 and 3 of Darlington are being refurbished in an almost simultaneous programme. Unit 1 refurbishment began in February 2022 and it is currently around halfway complete. Reactor disassembly is progressing and will be followed by the removal of all the internal reactor components, including some 480 calandria tubes and pressure tubes. As Rose says: “Unit 1 was started in parallel with Unit 3. We started Unit 1 in January last year (2022) so we are close to the midway point of that unit.”
According to OPG, the overall project has now entered its second half. Meanwhile, planning the Unit 4 programme on the basis of the lessons learned from work done on earlier phases of the refurbishment is underway. Replacement of the Unit 4 reactor is expected to begin in the third quarter of this year. “We will start the last unit, Unit 4, later this year once Unit 3 is complete and returned to service. We will be done all four units by 2026,” says Rose.
Replacing a CANDU reactor after 30 years of operations, although part of its standard operating model, is nonetheless no easy task. Rose explains: “The main component being replaced is the reactor core. We’re basically doing a retube, removing and replacing the pressure tubes, the calandria tubes and feeder pipes which is where all the nuclear reactivity occurs. We also looked at the rest of the systems and did a component condition assessment to see what systems needed to be replaced to support the 30-year extended life of the asset.” Work is progressing on the Primary Moisture Separator replacement on two of the steam generators, for example, although the majority of the steam generators do not need to be replaced even after 30 years: “The steam generators at Darlington were in very good condition,” Rose notes. Similarly, although the output of the plant will not change as a result of the refurbishment programme, some systems are being improved where that is appropriate: “We are upgrading our turbines in terms of the control system and we’re doing maintenance work on those. We’re not replacing any blades but we are replacing the stator in a couple of cases. We also have some safety upgrades to make and balance of plant items too such as electrical systems and some piping work,” Rose says.
The design of the CANDU reactor requires replacement of the pressure tubes and calandria tubes at the midlife stage. “That mid-life for Darlington was at about the 230,000 effective full power hour level, but of course you can’t change all four units on one day. We started Unit 2 early at about 180,000 hours so that when we got to the last unit it was within its range of needing to be replaced. This mid-life refurbishment is a design requirement and depending on the unit that midlife could be at different full power hours before it needs to be refurbished,” Rose explains.
Learning by doing
Almost unique among nuclear projects, the Darlington reactor replacement programme is not only on budget but it is ahead of time too. Rose puts this remarkable outcome down to both the detailed multi-year planning but also assiduously applying learning from one unit to another: “A lot of learnings came from the work on Unit 2. The team tracked about 3,000 different learnings, some very minor learnings where we updated procedures to make it easier, more efficient, safer or better quality, for example,” he says.
He explains the challenges of translating even the most thoroughly laid plans into the actuality of on-site action and the necessity of maintaining a dynamic approach to major infrastructure projects like reactor replacement. “The first time you do anything you have great plans laid out but once you get into those and the reality of the job face, it doesn’t work exactly as you had planned. The teams learned lessons and learned them in real time. It might be things like adjusting the parameters of the welding machines to optimise the welds of these feeder pipes onto the headers which is a significant component of our work. Learnings from how to do the welding of the feeders on Unit 2 made it more efficient for the subsequent units,” Rose says.
One of the key issues was a change to the conceptual team structure to create a more cohesive unit between OPG staffers and third-party contractors. Rose says: “One of the large learnings was the ‘one team’ concept. When we started Unit 2 we approached it in a traditional EPC way where OPG was the general contractor and we had a vendor who was the EPC.” He continues: “We found out during the process of doing Unit 2 that instead of having our team doing oversight it made a lot more sense for us to be an integrated team. So, we integrated the OPG oversight team with the vendor team into this one team concept. You didn’t know who was working for what company and, quite frankly, it didn’t matter. It was all about the team working together on a common goal to accomplish the refurbishments on time and on budget.”
Rose emphasises the importance of the shift from the traditional EPC model to one of an integrated project delivery model as a key component of the successful outcome.
In addition, the OPG approach also meant having the courage to change the model for CANDU replacement.
Rose explains: “There were other things we learned on unit 2, for example we removed the pressure tubes first and then the calandria tubes in series. That’s the way the 10 refurbishments before us had all been done. But during Unit 2 when we started to think about some possible efficiency improvements one of our engineers brought forward this idea of removing both the pressure tube and calandria tubes together. It’s faster and in fact it’s safer because you have less transports of the pressure tubes from the reactor to the waste stream. In Unit 3 we removed both of them together and it saved us over 30 days on the schedule and it’ll save at least that on Units 1 and 4, too. That investment ultimately saves 90 days on the schedule, which is quite a bit of money when you think about the cost of all the people working on this project, the capitalised interest and so on.”
Tooling and testing
Devising a new procedure to take out the pressure tube and the calandria at the same time was a combination of changing the process but also developing new equipment and a new device. All those changes had to be qualified too. As Rose says: “Modifications to the tools, to the procedures, to the work that was happening on the face – in nuclear every task is qualified so we have to have procedures, we have to have inspection points so all of those things that need to be done associated with that change in process also needed to be completed.”
OPG also adopted new digital and automated tools where possible. This not only meant plant equipment, such as new digital controls for the steam turbines, but also in the refurbishment process, too. “We’re removing components that have been in the in the reactor for 30 years but many of the tools used for the removal phase of the reactor used digital and automated tooling to make the process safer and easier. Many of these tools were controlled by an operator who was in a different location from the actual vault where the work was being done. The whole point of that was to minimise the number of people that were interacting with the tool during the removal phase and increase safety for workers,” explains Rose.
“There’s a number of digital improvements that were made in the tooling and continued to advance to automate the job and increase worker safety,” says Rose. Again, learnings from Unit 2 were applied to get the most out of the automated tooling. He says: “A lot of our welding tooling for the feeder pipes is automated. You lock on these welders, calibrate all the tools and through computer- assisted processes do the welding. It is very difficult to get the parameters right to make sure that the welding happened correctly though. That was one of the lessons learned on Unit 2. Because every weld is subsequently inspected, in Unit 2 the radiography required clearing the zone. We went to digital radiography in the subsequent units so in Unit 3 by using a digital radiography you did not need to get every worker out of the vault to do the radiography. That is another technology advance.”
The use of mock ups and detailed modelling of procedures with new tools were also important to the overall success of the refurbishment programme. “The other key lesson from the project is that we created a full-scale mock-up of the calandria at the Darlington Energy Complex about 1.5 km from the station. Every single tool that we used in the plant was fully tested once at the factory during functional acceptance testing but also inside our mock-up. We would run it through its paces in as real-life situation as possible, we’d get the workers, put them in plastic suits and run them through the process of operating that tool. We’d even try to break it, throwing things out that were anomalies and making sure that they knew how to react. The whole point was if you fully tested that tool in the mock-up and fully trained the workers before they went into the real thing, you’re likely more successful.”
OPG worked with the third-party contractor SNC Lavalin Ltd but the tooling was sub-contracted to a number of different companies, including ATS, Cambridge, Rolls-Royce and others. CANDU also produced some of the tools.
Although the physical mock-up at Darlington delivered numerous operational benefits there were limitations due to the differences between the blueprints and the as-built plant. This required additional processes such as blue laser scans of the existing plant to know where all the positions were. “We used that as part of the planning,” says Rose, adding: “These reactors were built 30 years ago and even though there’s a design, the components are slightly out of place in terms of exact location. When you’re rebuilding components to put in there we want to make sure we accounted for that so we did a full laser scan of the vaults which then created a digital model.”
The importance of planning
While it is almost unique to have any kind of nuclear project delivered on time and on budget, the Darlington refurbishment has achieved that through an intense planning process, including mock-ups and modelling. “It really boils down to meticulous planning. Planning doesn’t guarantee success, but a lack of planning guarantees failure. We planned this job extremely well. We are rate regulated by the Ontario Energy Board and we had to present our plans and our cost estimate schedule to them. Independent experts said they hadn’t seen a project that was so ready to be executed. We had good plans and we had to stick to them,” says Rose, adding: “Too often I’ve seen where projects are very well planned and risk registers are created and then during the project it seems all of that gets parked and forgotten about. Because we had planned the project so well, we knew where we were supposed to be each and every day and if we weren’t we could take action. By knowing where we were supposed to be and how many people we were supposed to have on the work if we weren’t accomplishing the production rate it was very visible. Every day there was an issue we focused in on why we didn’t achieve the planned progress and what we were doing to resolve those issues. That meticulous focus each and every day really drove us to success. If there was a problem we were asking why and fixing it and rectifying it very early.”
However, he also adds a note regarding the importance of built-in flexibility as a result of in-depth planning. Rose says: “In every project we have contingency. There are risks on every project and we have mechanisms to draw down contingency. We used to draw down funds for contingency and where we had opportunities we would actually fund contingency. So, if we learned something on Unit 2 that we could put forward on Unit 3 we took the budget away and put it back into contingency in case any other things came about. We created what we called an opportunity register corresponding to a risk register and we went after the opportunities as aggressively as we manage the risks.”
Once the refurbishment programme is complete in 2026, this C$12.8 bn (US$9.4 bn) project will enable the Darlington station to operate for an additional 30-plus years but the learnings on CANDU will potentially last far longer, reducing the cost and risk of reactor replacements.