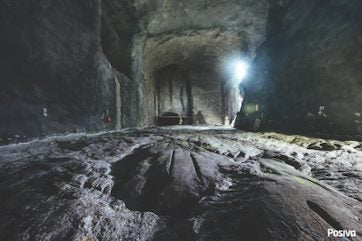
Four-legged ‘spot’ robots, developed by US-based Boston Dynamics, have negotiated pitch-black conditions to map an evaporator cell in the fuel cycle area of the Dounreay site in Scotland. Dounreay was the UK’s former fast reactor test facility, which operated from 1955 to 1994. It is now being decommissioned. Ongoing clean-up and dismantling work is continuing.
Spot’s task was to map out the four-storey cell, collecting important radiological data for the team to use when planning the decommissioning of the facility; and to gain useful experience on how the robot and survey equipment should be used.
A team of 12 has been supporting the robot trials. This includes Dounreay staff led by Project Manager Bernie Jones, as well as staff from Createc, the systems integrator for Spot, who are working with Dounreay on a series of seven use cases for the robot to be carried out over the next few months.
The site joiners constructed a wooden mock-up of the evaporator cell entrance and temporary containment in a clean area to test the abilities of the robot and train its operators before the work moved into the evaporator cell.
A Spot robot, covered in a protective suit, once inside the evaporator cell collected data to give the team a complete 3-dimensional map of the area. It also collected radiological data to create a full dosimetry map showing areas of higher radioactivity, which will enable the team to develop a radiological fingerprint.
“By doing the initial groundwork, Spot has shown us the hazards that might affect workers who are tasked with the decommissioning, said Bernie Jones. “We will use the data to ensure that we mitigate those hazards and keep our people safe. This work also has the potential to save money on our decommissioning investigation.”
Createc’s Energy MD, Will Newsom, said: “Over the course of five days, we deployed two Spots in multiple entries to the cell. The environment we were exploring was complex as it had not been accessed in over 20 years, so the team didn’t know what to expect: that’s what made the deployment so challenging.” He added: “Using our innovative NV-Explore sensor, the team captured 3D radiation maps. At the same time, one Spot with a robotic arm was used to take several physical samples for lab analysis.”
NDA Technology and Innovation Director Professor Melanie Brownridge noted that the work had shown the potential applicability of the technology across the NDA group. “Shared learning and collaboration across our group is essential to the successful delivery of our mission. We have many common challenges and the potential to learn and share the impact, benefitting from innovative approaches such as this is truly significant.”
Over the coming year, Dounreay will systematically validate the suitability of several different types of sensors, combined with Spot, to support the digitalisation of existing on-site processes. The use cases will demonstrate the multi-tasking value of the quadruped for nuclear sites, and its ability to carry out practical work for multiple teams.
The Spot robots were delivered to the Dounreay site in June. Spot had previously been deployed at sites across the NDA estate, with the NDA co-funding the work at Dounreay to help deliver benefit from the innovation groupwide. The work at Dounreay complements and builds on the recent deployment of Spot at Sellafield.
Earlier this year the robot canine was deployed into an active area at Sellafield for the first time to understand the benefits of using spot to inspect and clean active cells that would normally require workers to enter in air-fed protective suits. The safety benefits are clear, but the work can also be done faster as spot can work in these areas much longer than a human could. It has halved the predicted costs and significantly reduced the waste generated from protective gear, Sellafield says. Prior to spot deployment two operators would go in, needing up to seven other people and taking up to four hours to prepare for an hour’s work.
Charlotte Brew, sub project manager, Sellafield Ltd said: “We started with demonstrations of its potential and six months later, we’re using it to accelerate high hazard reduction. This work wasn’t meant to start happening until the late 2020s but identifying Spot like this has brought it forward. Just one robot dog is making a massive difference.”
Melanie Brownridge, Nuclear Decommissioning Authority technology and innovation director said: “This exciting technology is helping move our people away from harm, reducing our costs significantly and could help us deliver our mission years earlier than planned. We are also seeing the benefits across the NDA group as we share our experiences to overcome common challenges across multiple sites.”
Donkey on duty
In a related development, Swiss company ANYbotics has been testing the performance of its four-legged ANYmal robot in Finland’s Onkalo underground used fuel repository near Olkiluoto. Researchers at the Swiss University of Technology (EHT) built the first four-legged robot in 2009 and ANYbotics was established to commercialise this technology in particular its “ANYmal” robot. Although generally referred to as a robot “dog”, the robot used in the Olkiluoto test was called “Donkey”.
The test was jointly organised by the European Nuclear Energy Organisation (Euratom) and Finnish radioactive waste management company Posiva Oy. Euratom and Posive are interested in the use of robots that can access places unsafe for human operators, for example for safeguards inspections in high-radiation states or toxic environments. The robot is also not dependent on working hours and so can be programmed to do undertake inspections at night.
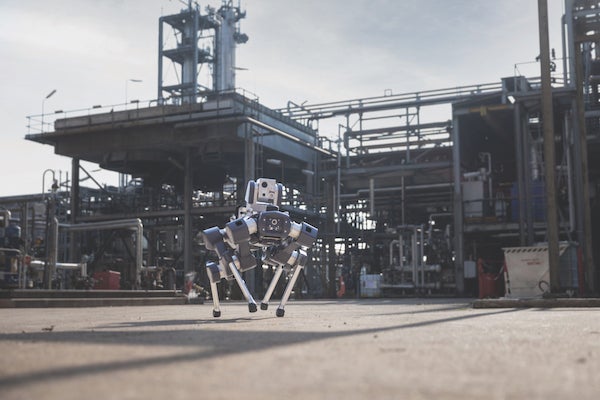
Moreover, a robot would also be available in an emergency at shorter notice than the time needed to call an inspector. It can be equipped for various tasks with various devices, such as optical and thermal cameras, microphones, gas or radiation detectors.
The Swiss robot uses laser sensors as well as cameras to observe the environment and is able to identify its own location very accurately. By combining observation with spatial data (such as mapping or area scanning), the robot can plan its navigation route independently if necessary. ANYmal is designed for autonomous action in challenging environments and has previously been tested in mountainous terrain. However, Onkalo’s tunnels provided a unique framework to assess the robot’s capability.
Using battery power, the robot walked through the Onkalo tunnels for about 1.5 hours. The purpose was to test the distance it could travel in Onkalo-type conditions on a single charge and also to see whether there were parts of the terrain that presented obstacles to its progress. The route was first planned using the robot’s scanning and mapping functions. It progressed autonomously on the scanned route observed by the research team but was always available for remote control, for example in an emergency. Various security functions were programmed into the robot. For example, it circulated the obstacles on the route from a certain safe distance and stopped when someone entered its safety zone.
ANYmal is 93cm long, 53cm wide and 89cm tall and weighs about 50kg. It is fully protected against moisture and dust. It has a walking speed of 1,3 metres per second and is able to cross a gap 30cm wide. It does not require light for autonomous action.
Single robot dogs are already making a difference in places like Sellafield and Onkalo, it’s easy to imagine that fleets – or packs – of them could transform decommissioning, waste management and a host of hazardous activities associated with nuclear energy.