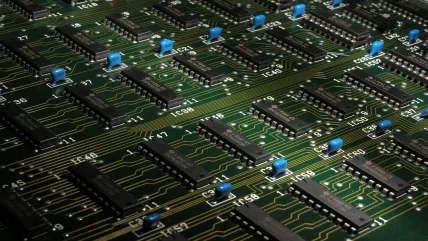
In many electronic circuits and printed circuit boards (PCBs), microcontrollers serve as the foundation. This is where programs are stored, run, and are connected to various sensors, motors, and other peripheral inputs and outputs based on the designers’ specifications.
There may be instances where microcontrollers will be utilised in applications or systems that operate in extremely hazardous environments, such as the nuclear energy sector, to observe and document environmental factors or obtain readings from sensors. They can also control valves, servos, lights, and alarms, dictate the flow of materials or services, make decisions based on sensor readings, and send alerts or alarms for emerging situations. In the nuclear industry, microcontrollers may be utilised in sensor networks to monitor environmental factors and record details of background radiation. In areas of high radiation, microcontrollers and their peripherals may become contaminated and malfunction.
This study aims to determine the levels of radiation that microcontrollers can handle before malfunctioning, succumbing to radiation, and being damaged beyond further use.
Assessing radiation exposure and shielding
In this study, the irradiation cycle entails placing an Arduino Uno Rev 3 microcontroller in its respective shielding material and exposing it to Cobalt-60 radiation source for five minutes. Different kinds of shielding were used to identify their radiation-shielding properties including 10mm-thick lead, 1.32mm-thick lead, 10mm-thick concrete, 10mm-thick aluminium and 10mm-thick steel. Also, various types of 3D printing filament 10mm-thick and no shielding were deployed. Following the completion of the irradiation process, the microcontroller was connected to an LCD display to determine if the correct output was displayed. If so, the microcontroller was exposed to a subsequent irradiation cycle. If the LCD showed an incorrect output after an irradiation cycle, a bench test was conducted.
The microcontrollers were able to endure as much as 60Gy/min or an overall ionising dose of 1050Gy. Nonetheless, at 70Gy/min, the controllers malfunctioned, and a bench test verified that all microcontrollers had sustained damage and were non-functional.
The tested materials, namely aluminium, steel, lead flashing, PLA, PLA+, PETG, and concrete, proved ineffective in providing any supplementary shielding for the microcontrollers during the irradiation process.
Based on these results, it has been determined that a lead thickness of 10mm provides the optimum protection. This specific lead can withstand doses of up to 70Gy/min (1400Gy) and 80Gy/min (1800Gy). However, it is crucial to consider the weight when deploying systems.
Code 3 lead flashing at 1.32mm provided no protection whatsoever for the microcontroller against radiation.
Effective shielding of microelectronics
It is evident from the tests conducted on various shielding materials that none of them can guarantee the protection of the microcontroller beyond the 70Gy/Min mark or 1400Gy Total Ionising Dose (TID) Rate. However, by using a 10mm thick lead shield, additional protection can be provided, enabling the Arduino micro-controller to withstand gamma radiation up to 90Gy/Min or 2250Gy TID. Despite being the most effective shielding material, the challenges of using such materials must be considered before deploying microcontrollers or electronic systems in environments with a radiation hazard.
Further research is imperative to investigate alternative materials that can act as shielding materials to protect the microcontroller and increase its longevity. Furthermore, it would be prudent to consider utilising microcontrollers that have undergone the radiation hardening process.
This article was produced in collaboration with University of Gloucestershire and the University of Manchester Dalton Nuclear Institute. Research funded by the National Nuclear Users Facility
Author: Mark Rhodes. BSc (Hons), MSc, PGCert(RM), DipEd, MSET, MBCS. University of Gloucestershire. Ph.D – Cyber & Technical Computing