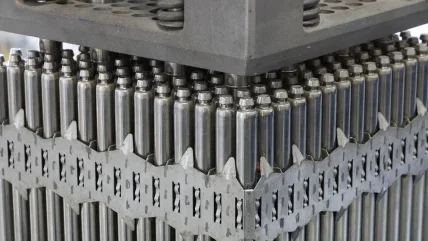
The global market for nuclear fuel is steadily developing as the recent energy crisis and climate change concerns are allowing nuclear generation to experience something of a renaissance. According to IAEA forecasts, by 2050 the global nuclear power plant fleet will more than double its current capacity: from almost 380 GW now to 873 GW. However, the Agency notes that the increase will be largely achieved through nuclear technologies that are now just being developed and tested, including those which involve the use of novel fuels.
Today, about 30 companies from two dozen countries produce nuclear fuel for land-based reactors. The total volume of nuclear fuel production capacity is not so large – about 20,000 tonnes per year. The three largest producers – French company Framatome, US-based Westinghouse and Russia’s TVEL – supply approximately half of this total production volume.
In recent years many of these producers have accelerated their activities in the field of development of novel fuels. At the same time, the current diversity of technical reactor concepts implies an equal diversity of fuel types. As part of these developments, particular attention is being paid to new accident tolerant fuels (ATF).
The development of ATF has become a priority for fuel designers over the last decade, notably in response to an analysis of the causes of the accident at the Fukushima Daiichi nuclear power plant which included the zirconium-steam reaction that takes place at temperatures above 1200 °C. There are currently two key pathways to develop ATF technology: to reduce the amount of zirconium in the fuel assembly or to modify the chemical composition of the fuel so that the heat transfer rates of the fuel increases. While it cannot be said that the use of novel fuels will prevent all possible accidents the development of ATF is designed to provide more response time in the event of a rare emergency, as well as to obtain technological and economic advantages during normal operations of the nuclear reactor.
The creation of novel fuel is currently being carried out by all the largest manufacturers as well as other significant players in Europe, the Americas and Asia.
Changing cladding and composition
At present the main ATF efforts of developers are aimed at creating new materials for both cladding and fuel composition. One of the more promising possible solutions is the development of cladding coatings that include chromium in one form or another. Chromium coatings on zirconium alloys provide increased corrosion and wear resistance, as well as reduced hydrogen permeability, which helps maintain the ductility of zirconium alloys. Another option that requires further study, but is potentially interesting for the production of cladding, is composite materials based on silicon carbide.
A universally preferred coating technology has not yet been identified; various manufacturers use different options that they find most suitable. According to Fedor Vysikailo, a professor at the Department of Theoretical Physics at Moscow State University, complex application methods have a high technological, but low economic efficiency.
The methods of heavily doping the surface have the same problem. More promising, according to Vysikailo, are laser application methods. Scientists also note the attractiveness of magnetron methods for coating fuel rods (high application speed and uniformity of coating).
For fuel compositions, options are also being considered that include the addition of chromium or molybdenum, as well as the use of silicides or uranium nitride instead of uranium oxide. New fuel compositions also include doped uranium dioxide (UO2), high-density fuels (eg, U3Si2), and metallic fuels, such as uranium-molybdenum.
Like Westinghouse, Framatome is focused on developing composite-clad fuels. In the long term, the company plans to develop a SiC/SiC composite cladding and Cr2O3-doped uranium dioxide fuel. Currently, Framatome is preparing to manufacture a novel molybdenum-uranium (U-Mo) fuel to extend the life and safe operation of the Forschungsreaktor München II (FRM II) research reactor in Germany and has recently received approval from the US Nuclear Regulatory Commission (NRC) to apply the company’s suite of Advanced Codes and Methods to operating conditions with uranium 235 enrichments above the industry standard of 5%.
The activity of American developers in the area of novel fuels could be partly explained by the aging of the local nuclear fleet – approximately half of the existing units will reach the end of their design life before the mid-2030s and with them the status of the US as one of the world’s largest nuclear fuel importers.
Much of the activity the surrounds novel nuclear fuels is focused of high enrichment low assay uranium (HALEU) which can reach enrichments of up to 20% U235. For example, Centrus is notably beginning first-of-a-kind HALEU production at its American Centrifuge Plant cascade located on the Department of Energy’s Portsmouth Gaseous Diffusion Plant (PORTS) reservation in Piketon, Ohio. According to Dan Leistikow, VP of corporate communications at Centrus, that will be the first new US-owned and US-based technology enrichment plant to start production in 70 years. Centrus’ demonstration project will only deliver an initial 20 kilograms of HALEU before the end of the year, but the company has plans to scale up to 900 kg of annual production starting in 2024.
According to analysts, that will create certain conditions for the beginning of mass production of HALEU in the US, but only in due course.
At the same time another US-based generating company, Southern Nuclear, has announced that it has also received permission from the US NRC to use advanced nuclear fuel enriched with uranium 235 to 6% at the newly commissioned Vogtle nuclear power plant. This is the first time a US commercial reactor has been approved to use fuel enriched above 5%.
Particular hopes are also being raised by the novel nuclear fuel which is being produced by the American-based Lightbridge Corporation. This fuel is reportedly rapidly gaining popularity in the US and some other Western countries.
In case of Russia’s Rosatom and its fuels subsidiary TVEL, the production of novel nuclear fuel is expected to be launched on the basis of Mining and Chemical Combine (MCC) loctaed in Zheleznogorsk, Krasnoyarsk Territory. That will be a mixed oxide uranium-plutonium MOX fuel, that will be used for the world’s most powerful multi-purpose fast neutron research nuclear reactor, the MBIR, with an output of 150 MWth. The reactor is being built at the site of the Rosatom Research Institute of Atomic Reactors (NIIAR) in Dimitrovgrad, in Ulyanovsk region. Commissioning of the reactor is scheduled for the second half of the 2020s.
The capabilities of the MCC make it possible to organise the production of various types of nuclear fuel on its site, while the current MOX fuel which is produced uses depleted uranium and plutonium separated during the reprocessing of spent nuclear fuel from thermal reactors.
Rosatom has also plans to more actively promote its advanced nuclear fuel abroad. As part of this, the company has recently offered its advanced nuclear fuel to extend the Indian Kudankulam reactor cycle from 18 months to 2 years. In general, most analysts believe that Russia has good chances to secure a significant share in the global market for advanced fuels, which is partly due to their ability to access cheaper raw materials.
High temperature reactor fuels
The ever-growing interest in small high-temperature gas reactors reactors (HTGR) and the novel nuclear fuel needed for them has become one of the most obvious trends. At the turn of the 1990s–2000s, Japan commissioned a high-temperature technical reactor (HTTR) with a capacity of 30 MW. The fuel for it is TRISO – uranium microspheres packed in a multilayer cladding of silicon carbide and pyrolytic carbon. The main function of the cladding is to retain fission products inside the microsphere and provide mechanical strength. Fuel spheres were placed in tubes, which were assembled into fuel assemblies. Work is underway to further improve the fuel. One option is to replace the silicon carbide in the microsphere cladding with zirconium carbide.
In the US, the production of fuel for HTGRs is being developed by the companies including X-energy, BWXT, and USNC. The state supports R&D on this topic and also invests in the creation of industrial production of such fuel (through AGR, ARDP programs, for instance). In China, the CNNC company is building the HTR-PM project – an HTGR with a capacity of 200 MW. Here microspheres are poured directly into the reactor core in a “pebble bed” technology. This reactor also runs on TRISO fuel. The fuel cores, which are about 0.5 mm in diameter, consist of uranium enriched to 8.9% in a multilayer cladding.
It’s clear that new kinds of nuclear fuels are emerging in response to both a new generation of reactors and new demands for safety and performance. Many of these fuels are still under development but there’s little doubt that novel nuclear fuel is set to become a commercial reality.