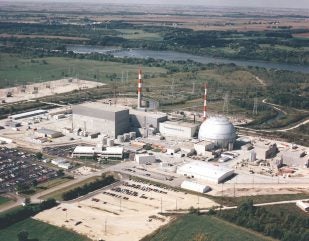
Dresden 2 and 3 are BWR/3S designed and supplied by GE Nuclear Energy. They sit on a site in Illinois, USA, along the Illinois, Des Plaines and Kankakee rivers. Dresden 1, which shares the site, is in a safe storage condition.
Constellation Energy Generation is the licensed operator of the two units, which were originally licensed to operate at 2527 MWt, raised to 2957 MWt in 2001. Dresden 2’s operating licence will expire at midnight on 22 December 2029 and Dresden 3’s operating licence will expire at midnight on 12 January 2031. Both licences have already been extended once, and now Constellation is seeking a ‘subsequent’ licence extension that would add a further 20 years.
Constellation’s ‘Subsequent Licence Renewal Application’ was submitted to the US Nuclear Regulatory Commission (NRC) in April. It included a series of new aging management programmes and a larger number that would be enhanced. The summary below gives a flavour of the how the plant’s aging management programmes are being use to support the new life extension application.
New programmes
The new mechanical programmes are related to potential material loss from components; embrittlement; inspection of less accessible areas such as internal pipe surfaces or buried pipes and cabling; or external factors such as water ingress. One adds a one-time inspection to the existing inspection regime.
External surfaces monitoring of mechanical components will manage loss of material of metallic components, as well as loss of material, cracking, blistering, hardening and loss of strength for elastomeric and polymeric components, and reduced thermal insulation resistance due to moisture intrusion. Periodic visual inspections of metallic components, elastomers, polymers, and insulation jacketing will be conducted on a two year frequency. For certain materials, such as flexible polymers and elastomers, physical manipulation to detect hardening or loss of strength will be used to augment these visual examinations. A sample of outdoor component surfaces that are insulated and a sample of indoor insulated components exposed to condensation (due to the in-scope component being operated below the dew point), will be periodically inspected every 10 years during the subsequent period of extended operation.
Inspection of internal surfaces in miscellaneous piping and ducting components will manage loss of material, and cracking of metallic components, as well as loss of material, cracking, blistering, hardening and loss of strength of elastomeric materials. Reduction of heat transfer and flow blockage will also be managed. It will consist of visual inspections of all accessible internal surfaces of piping, piping components, ducting, heat exchanger components, polymeric and elastomeric components and other mechanical components. Visual inspections for leakage or surface cracks will be performed to detect cracking of stainless steel components exposed to a diesel exhaust environment as the detection of staining on the component external surface demonstrates the ability to detect leakage. An evaluation will be performed that demonstrates that cracks will be detected prior to challenging the structural integrity or intended function of the component.
At least once in each 10-year period of extended operation, a sample (20% of the population) will be inspected, along with opportunistic inspections. For certain materials, such as flexible polymers, physical manipulation or pressurisation to detect hardening or loss of strength will augment visual examinations.
A thermal aging embrittlement of cast austenitic stainless steel (CASS) programme will provide assurance that the intended functions of the reactor coolant pressure boundary components – piping components and pump casings – with the potential for significant thermal aging embrittlement will be maintained. A screening methodology based on casting method, molybdenum content, and ferrite percentage will identify components to undergo qualified visual inspections, such as enhanced visual examination or qualified ultrasonic testing methodology, or a component-specific flaw tolerance evaluation.
Note that reactor vessel internal components fabricated from CASS are already managed by another aging management programme.
The selective leaching programme will monitor components whose materials are susceptible to selective leaching and in their specific environment. Susceptible materials include grey cast iron, malleable iron, ductile iron, and copper alloys containing greater than 15% zinc. It includes one-time inspections in closed cycle cooling water and treated water environments, but operating experience has not revealed selective leaching in these environments. Opportunistic and periodic inspections consist of visual and mechanical examination techniques (for grey cast iron, malleable iron, and ductile iron components), as well as periodic non-destructive and destructive examinations for determining physical properties such as the degree of dealloying, depth of dealloying, through-wall thickness, and chemical composition, for components exposed to raw water, waste water, and soil environments. Inspections and tests will be conducted to determine whether loss of material will affect the ability of the components to perform their intended function through the subsequent period of extended operation.
The ASME Code Class 1 small-bore piping programme augments existing ASME Code, Section XI requirements for small-bore piping and systems of 1-4” (2.4-10 cm) diameter. It includes volumetric or destructive examination of a sample of full penetration (butt) welds and partial penetration (socket) welds in Class 1 piping to manage cracking due to stress corrosion cracking or thermal or vibratory fatigue loading. The programme will verify that degradation is not occurring and validate the effectiveness of existing programmes and practices.
The extent and schedule for volumetric examination is based on Dresden plant-specific operating experience, which demonstrates that cracking of Class 1 small-
bore welds is not occurring and that actions have been implemented to effectively mitigate the causes of the single instance of past cracking.
Internal coatings/linings for in-scope piping, piping components, heat exchangers, and tanks programme manages degradation of internal coatings/linings exposed to raw water, treated water, fuel oil and condensation.
For buried cement-lined fire water piping, opportunistic inspections will be performed in addition to flow tests and internal piping inspections. There are no piping or components with internal coatings/linings in the program scope that are exposed to air, closed-cycle cooling water, waste water, lubricating oil or treated borated water. It includes visual inspection where loss of coating or lining integrity could impact the component’s or downstream component’s functions.
Peeling and delamination is not acceptable. Blisters are limited to a few intact small blisters that are completely surrounded by sound coating/lining bonded to the substrate with blister size or frequency not increasing between inspections. Minor cracks in cementitious coatings are acceptable provided there is no evidence of debonding. All other degraded conditions are evaluated by a coatings specialist.
Electrical insulation for inaccessible instrument and control cables not subject to 10 CFR 50.49 environmental qualification requirements applies to inaccessible or underground instrument and control cables that are within the scope of licence renewal and potentially exposed to significant moisture (three days of wetting or submergence over a continuous period). Manholes, handholes and associated accessible conduit ends are inspected for water accumulation and the water is removed as needed.
Electrical cable connections not subject to 10 cfr 50.49 environmental qualification requirements requires testing of a representative sample of electrical connections prior to the subsequent period of extended operation. The results will be evaluated to determine if there is a need for subsequent periodic testing on a 10-year frequency. Twenty per cent of each connector type population is a representative connector sample size and they will be tested to detect increased resistance of the connection.
One-time inspection of selected components will verify: the system-wide effectiveness of an aging management programme that is designed to prevent or minimise aging to the extent that it will not cause the loss of intended function during the subsequent period of extended operation; the insignificance of an aging effect; and that long-term loss of material will not cause a loss of intended function for steel components exposed to environments that do not include corrosion inhibitors as a preventive action.
The programme will include: determination of the sample size of components to be inspected; identification of the inspection locations in the system or component based on the potential for the aging effect to occur; determination of the examination technique, including acceptance criteria that would be effective in managing the aging effect for which the component is examined; and an evaluation of the need for follow-up examinations to monitor progression if age-related degradation is found that could jeopardize an intended function before the end of the subsequent period of extended operation.
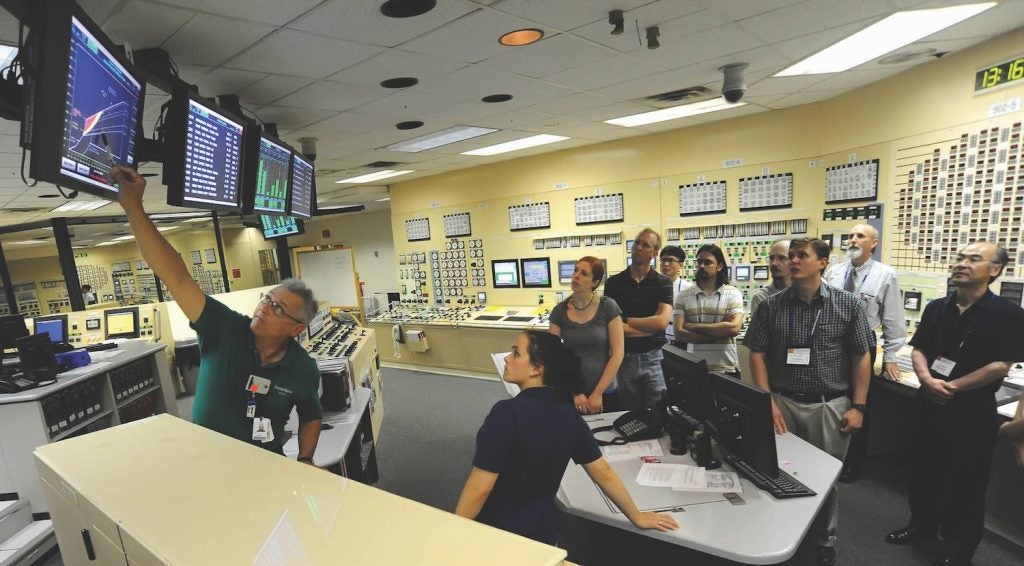
Requires enhancement
BWR vessel internals programme manages the effects of cracking and evaluations determined that supplemental inspections are not necessary during extended operation.
The BWR Vessel Internals program will be enhanced to limit the scope expansion exemption applying to large diameter jet pump diffuser, adapter and lower ring welds that are inspected by UT.
Flow-accelerated corrosion programme manages wall thinning caused by flow accelerated corrosion (FAC). It will be extended to reassess infrequently used piping systems excluded from the scope of the program to ensure adequate bases exist to justify this exclusion for periods of extended operation beyond 60 years.
Bolting integrity programme manages aging for loss of preload, cracking, and loss of material of safety-related and non-safety-related closure bolting on pressure-retaining components.
It will be enhanced to clarify guidance that proper selection of bolting material and lubricants, and appropriate installation torque or tension to prevent or minimize loss of bolting preload and cracking of high- strength bolting is a requirement and to perform periodic visual inspections of a representative sample of bolting for bolted joints where leakage is difficult to detect, such as bolting in joints that are submerged, in systems that are not normally pressurised, and in systems containing air or gas. It will revise procedures on visual examinations of bolted joints to include inspection parameters such as lighting, distance, and offset and will require additional bolts to be inspected when samples do not meet acceptance criteria.
Open-cycle cooling water system aging management programme will additionally include at least 20 inspections for recurring internal corrosion in the raw water systems every 24 months; a comparison to the design minimum allowable wall thickness to determine the acceptability of the component for continued use; and a determination of re-inspection interval.
Closed treated water systems programme manages loss of material, cracking, and reduction of heat transfer in piping, piping components, tanks, and heat exchangers exposed to a closed cycle cooling water environment. It will add opportunistic visual inspections and sample-based periodic inspections using techniques (visual, surface, or volumetric) capable of detecting loss of material, cracking, and fouling.
The reactor vessel surveillance programme manages the loss of fracture toughness due to neutron irradiation embrittlement of the reactor vessel beltline materials. The programme is part of the BWRVIP Integrated Surveillance Program which is providing fluence and materials data. The programme will be enhanced to comply with 10 CFR 50 Appendix H.
The buried and underground piping and tanks condition monitoring programme addresses piping and tanks constructed of any material, including carbon
steel, stainless steel, polymers, aluminium, carbon fibre reinforced polymer, asbestos cement and cast iron. Annual cathodic protection surveys are conducted.
In addition, the programme will include direct visual inspections: of one 10’ (3m) section of buried stainless steel piping, two 10’ sections of buried polymeric piping and two 10’ segments of buried carbon steel piping, selected based on susceptibility to degradation and consequences of failure. Condition inspections be carried out on steel and stainless-steel piping including annual monitoring of the cathodic protection system and inspection of at least 25% of the internal surface of some buried fuel oil tanks.
An ASME aging management programme of metallic pressure-retaining components of steel containments will be enhanced with surface or enhanced visual examination to detect cracking, as well as volumetric examination of containment metal shell surfaces that are inaccessible from one side, if there is shell corrosion.
An ASME aging management programme of inspection of piping and component supports will be augmented with periodic evaluations of the acceptability of inaccessible areas of supports (for example, portions of supports encased in concrete, buried underground, or encapsulated by guard pipe), if warranted by conditions. Volumetric examination will be added if additional high-strength bolting is installed.
Enhanced electrical insulation programmes manage the effects of reduced insulation resistance at various voltage levels.
Insulation material is visually inspected and may be subject to other tests including thermography. The management programme will be enhanced to evaluate operating experience to confirm that insulation can still perform its function despite the cumulative effect of mitigated ageing, and testing a sample population when a large number of cables are identified as degraded.
Inaccessible medium voltage cables exposed to significant moisture undergo periodic testing to assess insulation condition.
Enhancements will include cable testing of circuits in scope at least once every six years. If there are events that could result in water accumulation and cable submergence there will be additional inspections. Two manholes (MH-16 and SBO-4) have been identified for regular inspection in case of water accumulation.
The metal enclosed bus programme involves visual inspection for age-related cracks, corrosion, foreign debris, excessive dust build-up and evidence of moisture, covering insulation as well as other equipment. This will now include periodic inspections of the 4kV switchgear accessible bus duct and a sample of metal-enclosed bus bolted connections.
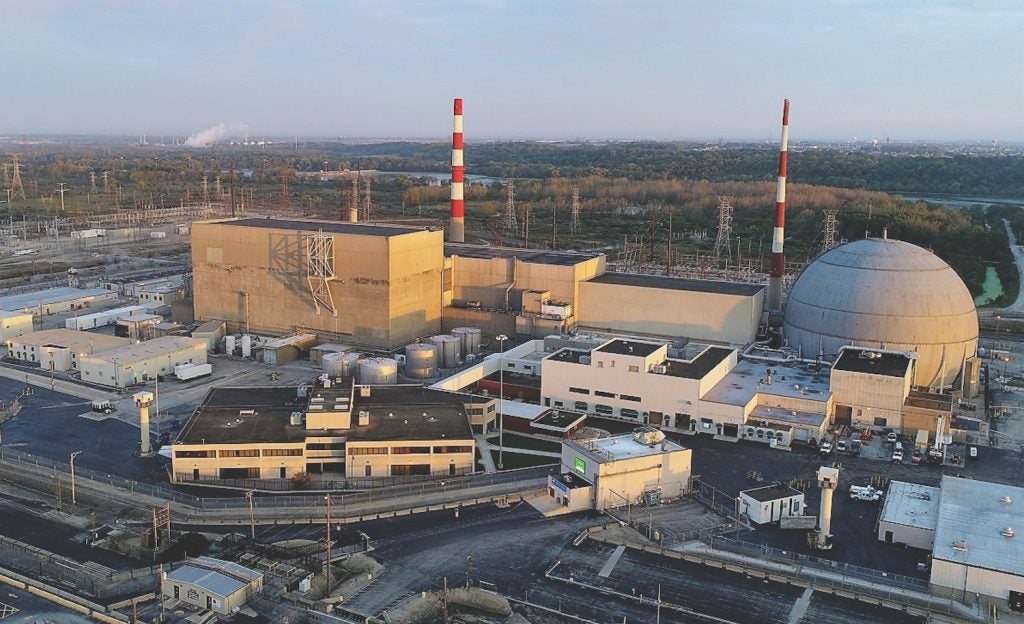
Balance of plant
Enhancements to the aging management programme include several that relate to systems and technologies that are familiar in non-nuclear and even in domestic contexts. Their inclusion illustrates the interconnected nature of complex nuclear power plants. Familiarity cannot be a reason for complacency over safety.
The compressed air monitoring programme will add opportunistic visual inspections of internal surfaces exposed to a dry air environment for signs of loss of material.
The fire water system programme applies sprinklers, fittings, valves, hydrants, hose stations, standpipes, pumps, and aboveground and buried piping and components. It will additionally include a a one-time volumetric wall thickness inspection on a representative sample of piping that is periodically subject to flow but is normally dry. It will also include biennial external visual inspections of sprinkler systems in accessible and inaccessible areas and internal visual inspections of sprinkler and pre-action system piping to identify internal corrosion, foreign material and obstructions to flow. Follow-up volumetric wall thickness examinations will be performed if internal visual inspections detect an unexpected level of degradation due to corrosion and corrosion product deposition.
The hydrant flushing procedure will be revised to require that hydrants drain within one hour. The testing frequency of the transformer deluge systems will be increased to a biennial basis and the flow test and main drain test procedures will be revised to perform additional tests after each failed test.
An outdoor and large atmospheric metallic storage tanks programme includes two contaminated condensate storage tanks, and contaminated and clean demineralised water storage tanks. These tanks contain treated water, and are constructed of aluminium. They are not insulated and are supported on a concrete and sand foundation. This means that the bottoms of the tanks are inaccessible for direct visual inspection. The programme is being enhanced to apply sealant to provide a moisture barrier at the perimeter of the bases of both the clean and contaminated demineralised water storage tanks. The programme will also perform an inspection of the sealant at the perimeter of the base of the contaminated condensate storage tanks and demineralised water storage tanks for signs of degradation every two years and perform periodic volumetric inspections of the contaminated condensate storage tanks, clean demineralised water storage tank, and contaminated demineralised water storage tank bottoms.
The fuel oil chemistry aging management programme relies on a combination of surveillance and maintenance procedures. It will be enhanced to perform periodic internal inspections of the emergency diesel generator fuel oil day tanks and fire pump fuel oil day tank at least once during each 10-year period.
Each tank will be drained and cleaned and the internal surfaces visually inspected. If there is evidence of degradation they will be volumetrically inspected. There will be quarterly particulate contamination, water and sediment checks, and microbiological activity checks for the isolation condenser makeup pump fuel oil day tanks. The fuel oil sampling and draining of accumulated water will use a new route to the existing drain valves that are connected to the flush drain connections of these tanks.
The structures monitoring programme relates to concrete and steel structures, steel edge supports, and steel bracings associated with masonry walls, groundwater chemistry and inspections of below grade concrete. It will be expanded to include the turbine and control buildings and include manholes, sliding surfaces and trash racks.
Clarified procedures will be required for cracking, spalling, scaling and leaching, while sliding surfaces will be examined for wear or corrosion and accumulation of debris. The programme will be expanded to sealants, seismic joint fillers, vibration isolators and bearing pads. New procedures will also be written to address aging management of areas exposed to raw water and groundwater/soil environments. After ground water testing adverse water chemistry results will be entered in a corrective action programme. If degraded concrete is identified it will be exposed for further inspection and possible repair.
Inspection of water-control structures includes structures such as intake canals and the discharge outfall structure.
Inspections will be performed at least once every five years for submerged components and every 10 years for those that are not. The programme will be expanded to include several new areas including canal bridges and embankments, as well as equipment such trash racks.
Water chemistry analysis will be used to model degradation.
In a recent statement, Constellation noted that renewing the NRC license for Dresden will give the company the ability to keep the plant operating through 2051. Although future policy and market conditions will ultimately determine how long the plant operates, renewal of its license would provide Illinois with an estimated 305 TWh of additional electricity over the 20-year extended lifespan. Constallation says this adds up to more low-carbon energy than all of the state’s wind and solar facilities have produced to date.