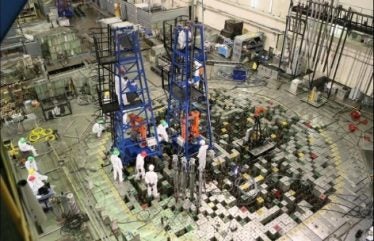
Four Russian nuclear power units with first generation RBMK-1000 reactors have been closed after 45 years of service and are being decommissioned. However, the NA Dollezhal Scientific Research & Design Institute of Power Engineering (Nikiet) has proposed extending the operating life of second generation RBMK’s from 45 to 50 years.
The RBMK (Reactor Bolshoi Moshnosti Kanalnii – high power channel reactor) is a heterogeneous thermal neutron reactor that uses graphite as a moderator. The coolant is water and the fuel is uranium dioxide. The reactor’s graphite stack is vertical columns 8 metres high, composed of blocks measuring 250×250 mm with a central hole. Fuel channels welded into the upper and lower metal structures of the reactor are inserted into the blocks. Fuel cartridges consisting of two fuel assemblies are installed in these channels. In addition to the fuel channels, the RBMK core contains channels for the control and protection system. The entire space of the graphite masonry is enclosed in a lightweight cylindrical body.
Initially, the designers determined the service life of the RBMK-1000 to be 30 years. “The first power units were designed in the late 1960s,” says Alexey Slobodchikov, Nikiet Deputy General Director and chief designer. “By that time, the USSR already had 20 years of experience in operating industrial uranium-graphite reactors, and had identified some limiting factors based on which the service life for the RBMK-1000 was established.”
RBMK-1000 reactors were constructed at NPPs in Chernobyl (Ukraine) – four units; Ignalina (Lithuania) – two units; and three NPPs in Russia. These included Leningrad (four units), Kursk (four units) and Smolensk (three units).
At Ignalina and Chernobyl the units were closed even before reaching the 30 -year service life. Unit 4 was closed following the 1986 acident and the other units were all shutdown by 2000. Ignalina’s reactors were both shut down by 2009 as a condition for Lithuania’s accession to the European Union. However, at Russia’s Leningrad, Kursk and Smolensk stations the first generation units operated for 15 years longer than originally planned accounting for 40 – 60% of Russia’s nuclear production.
“The first RBMK-1000 was launched in 1973 at the Leningrad NPP,” recalls Slobodchikov. “In 2003, its design life was coming to an end. And in 1998, the Russian Ministry of Atomic Energy launched a strategic programme to extend the service life of RBMK-1000 units. It included a whole range of large-scale work on safety justification and assessment of the residual life of equipment. Both the safety and control systems and the elements of the reactor plant were modernised. As a result, the life of all power units with RBMK-1000 reactors in Russia were extended their life by 15 years.”
In the 2010s, RBMK reactors encountered a rather serious problem – accelerated deformation of the graphite stack. Under the influence of radiation and temperature, graphite blocks change their geometry over time and begin to “push” each other, causing curvature of both the cells of the graphite columns and the fuel channels and control and protection channels. The development had been noticed in earlier industrial uranium-graphite plants and the RBMK was designed taking this features into account. But problems could not be completely avoided.
“We encountered this for the first time at the Leningrad NPP, said Slobodchikov. “In unit 1, the beginning of deformation was first recorded in 2011, and by 2012 had reached a point that did not allow further safe operation without additional measures.” Many organisations took part in the search for a solution. These included Nikiet, the Kurchatov Institute, Rosenergoatom, the All Russian Scientific & Research Institute for NPP Operation (VNIIAES), the Russian Federal Nuclear Centre – All-Russian Research Institute of Experimental Physics (RFNC-VNIIEF), the Afrikantov Experimental Design Bureau of Mechanical Engineering and others.
The task was extremely difficult. It was necessary to reduce the size of the blocks by removing excess graphite. Work in the core was performed by automated systems and robotic complexes. One repair required cutting about 150 graphite columns, which made it possible to reduce the deformation of the graphite stack to the required dimensions. The first repair at the Leningrad NPP took almost a year. Now it takes less than a month. The process has already been carried out at least once on all Russia’s RBMK‑1000, except at Smolensk 2&3, where it is not yet required.
Closure of first generation RBMKs began in 2018 and units 1&2 at the Leningrad and Kursk plants are being prepared for decommissioning. Secon generation RBMK reactors (units 3&4 at Leningrad and Kursk and Smolensk 1-3) generation 1000 (two at the Leningrad and Kursk NPP and three more at the Smolensk) were constructed differently. “By the time the design of the second generation began, NPP safety regulations had slightly changed requiring r a number of new technical solutions. The changes affected the design of the core and security systems,” explained Slobodchikov.
In 2022, Rosatom decided to start work to extend the service life of RBMKs to 50 years. “Today, the residual resources of the components at Leningrad 3 of the reactor unit of the third power unit of the Leningrad NPP has been assessed – technological channels, control and protection channels, graphite masonry,” Slobodchikov said. “The equipment needing replacement has been identified. The state of building structures, control and protection systems has been assessed. Documents justifying the safety of the unit’s life extension have been sent to Rostekhnadzor [regulator]. An operating licence is expected by the end of the year. Similar work is underway at Leningrad 4. Work on the extension of the other RBMK units has also begun.”
Slobodchikov made it clear, however, that extending the life of RBMK-1000 units beyond 50 years is out of the question. “The service life of a power unit, like other complex technical systems, is determined by the condition of non-replaceable elements including building structures. For RBMKs, this also includes large components of the reactor plant such as separator drums and metal structures,” he noted. “This equipment is technically impossible or economically unprofitable to replace. In addition, approaches to energy efficiency, productivity and working conditions change, and the level of scientific and technological development in general has changed.”
At all RBMKs, a system for monitoring the geometry of structural elements of the nuclear reactor core has been introduced. It uses fibre optic sensors, developed by scientists at the Russian Academy of Sciences. The sensors are lowered into the reactor channels on a special measuring rod. It takes 15 minutes to measure the deformation of each channel and to decide if it is time to begin restoring the resource characteristics of the graphite lining. The system can control fuel geometry without shutting down the reactor and unloading fuel assemblies.
In addition to generating heat and electricity, RBMKs are also used to develop valuable isotopes for medicine and industry. “Today, the channel reactor is the only one that can cost-effectively produce a wide range of isotopes,” Slobodchikov said. “The design makes it possible to reload irradiation devices during operation: there is no need to stop the reactor. This important characteristic has led specialists from Nikiet and the Kurchatov Institute to consider further development of the channel reactor. Nikiet has developed the concept of a new isotope energy reactor that fully meets modern safety requirements. Its power is less than that of the existing RBMKs – we are prioritising the task of producing isotopes.”