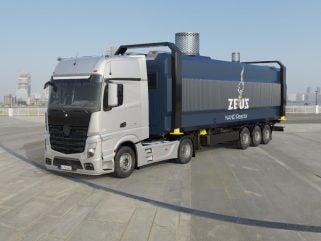
Founded by Jay Jiang Yu, NANO Nuclear Energy Inc was born from the anticipation of a resurgent interest in nuclear energy. Based partially on recognition that investment in renewables like wind and solar was falling, it also followed an understanding that mandates for industry to decarbonize were coming in and that the only solution was nuclear.
One of the first recruits to the emerging business was James Walker, with a background as a nuclear physicist and engineer, he was clear that the nuclear industry has a very high bar to entry and is also very capital intensive. Nonetheless, he explains: “With further analysis we realised very quickly that actually the area where we believe the most potential actually was, was not in the more developed areas like small modular reactors, it was actually in the micro-reactor space. That was because you could make 100,000 micro-reactors in a year, and you still wouldn’t meet the demand that they could potentially have.”
Walker argues that micro-reactors allow deployment of nuclear to areas where there had been no nuclear before and in fact nothing else other than diesel. Markets such as remote communities, military bases, disaster relief areas, remote industry, mining projects, oil and gas projects and maritime vessels were all in the frame. As Walker says: “The number of clientele just went on.”
However, beyond the clear market opportunity, technical factors also played a part. “Another reason why we were interested in this space was because the level of development was not nearly as far along as it was with SMRs. There was no licensed micro-reactor company, not even a company that was going through a licensing process. We thought with the right team and the right company structure so that we can finance it properly, we can actually pull ahead into this area pretty quickly,” explains Walker.
On taking the decision to step into the microreactor space NANO quickly reached out to two prominent and world-leading research teams. One from University of Berkeley, California, and one from the University of Cambridge in the UK. “We did a bit of analysis of what the customer would actually want and found that nobody would want to buy a reactor, nobody would want to run a reactor, and nobody wanted to deal with a reactor once it was end of life. We realised that if we own the reactor, we operate it and we just sell the energy that’s actually a business model everyone might be interested in because in remote locations, for diesel, it’s actually very expensive,” he says, adding that the logistical costs of bringing fuel in on a daily, weekly, or monthly basis, are very x much more expensive than the cost of the fuel itself. Conversely, a micro-reactor would simply run for 15 or 20 years without any need for fuel supplies or other intensive logistical support. Walker explains: “If we had a contract with, say, a mine for 15 years, we can work out how much that’s going to cost, and we can contract that capital cost over time, and actually start beating the cost of diesel in these locations.”
Having effectively established a business framework this in turn informed substantive design elements: “Once we had that business model in mind, we knew that we had to get the micro-reactors to be very portable, they had to be passively cooled so they’re extra safe, they had to have very few mechanical parts, wouldn’t need many personnel, and they had to be able to move by road, ship, or train, so you could deploy it anywhere very easily.
Reactor design fundamentals
Given the constraints imposed by the business model the two technical teams were given the same guidelines as the starting point for their designs but both teams came up with novel solutions. For the ZEUS team out of University of Berkeley – ZEUS is the name of their reactor – their solution was to remove the coolant completely and to instead have a solid core. In this case thermal conduction is harnessed to remove the heat from the uranium to the periphery of the core, and then normal air circulation takes that heat from the periphery of the core for use. “That’s pretty much as simple as you could make a reactor,” says Walker, adding: “We even call it a nuclear battery, because I don’t think you can simplify it any more than that.”
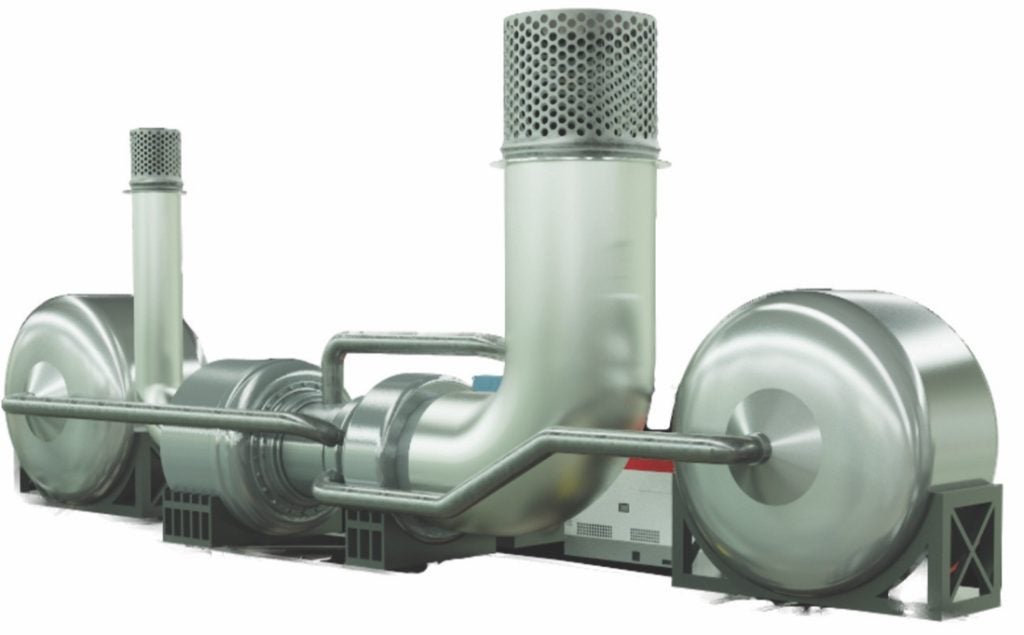
Meanwhile the ODIN team out of the University of Cambridge came up with a different approach. “They thought a lot more about deploying a more commercial product, and so they wanted to use more technology readiness level technology with off-the-shelf components, known fuels, and known technology so the licensing would be very easy.”
Their solution was a solar salt utilizing thermal convection, while using natural circulation to remove the heat. “Again, it’s incredibly basic, and the benefit of ODIN actually is it operates at a lower temperature with less thermal stresses, and it’s cheap to manufacture,” notes Walker.

For both reactors, because the power output is relatively small, there is still a large volume of space within the iso-container dimensions, which was the primary size constraint, which allows peripheral systems like the turbine to be included within the standard containerised unit. Both machines operate a Brayton cycle turbine which supports a compact design. “Operating a water-cooled reactor at above 100° means it needs to be highly pressurised and that leads to a more complicated safety case and longer licensing period. If you use solar salt as with ODIN you avoid those issues because the boiling point of the salt is obviously much higher. If you can remove the pressuriser, the reactor shrinks down further and on the ZEUS reactor, their solution was to remove the coolant completely,” he says. Walker also notes that the University of Cambridge is deeply involved with aircraft carrier turbines allowing NANO to develop its own optimized turbine to suit both reactor designs that will be installed with them.
While the reactors are quite different in their design philosophy, Walker is confident this is the right approach: “We can envisage a situation now where, even though we built two reactor teams to de-risk our endeavour and so we would have two modes of success, the reactors ended up being quite complementary, because ODIN is cheap to manufacture, can be mass manufactured very easily and deployed, whereas ZEUS has a higher operating temperature and can be more useful for things like process heat for industry. We’re still pursuing both for that reason,” he says.
Furthermore, the two teams offer other advantages, as Walker explains: “The technical teams actually can feed off each other and act as a sanity check to come in and audit each other as we go along. The knowledge that one team has they can actually pass on if it’s something like heat exchanger work that both teams can really benefit from. Sometimes we combine the work even if there have been big benefits of doing two different designs.”
A key part of the design approach has been aimed towards regulatory approval and licensing and NANO has taken substantial measures to engage with regulators from the outset. “We’ll always be looking to refine and develop and improve upon what we’ve got but I still think in the micro-reactor space, as far as launching a commercial product goes, we’re really in the lead because we’ve anticipated the regulatory requirements and how to actually design around those and we’re very transparent too. I think we’re the only micro-reactor company that paid the government to put an engineering team on our reactor and tear it apart, look at it and give us feedback,” says Walker.
According to Walker, both reactor designs were subject to an in-depth audit by Idaho National Laboratories, principally for that reason. “That external validation and input is actually very useful,” he says, noting that the output from those engineering investigations builds into the licensing documentation.
The University of Cambridge team that have been working on the ODIN reactor have a higher technology readiness level and have now completed the design and all the related computer modelling and concept work. Now they moving into the construction of test rigs that will be used for model validation, but also provides the data needed for the licensing process. “The Cambridge team have already designed the rigs and they are already building up the team because it is going to have to be expanded massively now. We’re already looking at a test bed reactor site, but we can build the initial rigs now to validate models and then we’re going to have to do almost the same rigs again, but with nuclear material, explains Walker, adding: “We’d like to get that going and have the site finalised at an initial land preparation later this year, with the idea that next year we begin buying in that nuclear material and then doing nuclear tests to produce the final data we’ll need to go to licensing. At that point, we’re essentially ready to go through that process to produce that commercial product.”
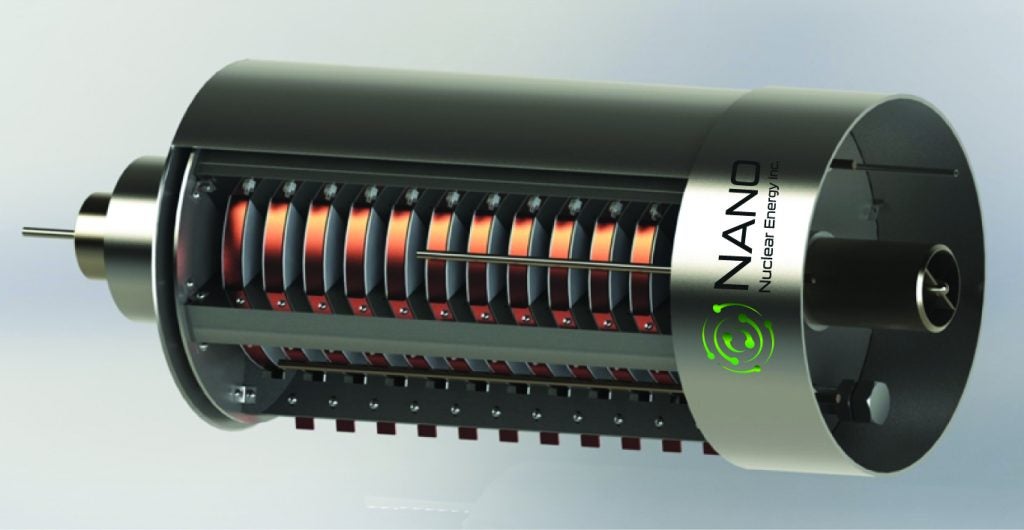
Once the licensing is complete NANO intends to be in a position where they can immediately go to market and start supplying the customer base. As Walker says: “We’ve had interest from big mining companies, from the military, and the island nations too because they’re looking for cleaner solutions that aren’t nearly as expensive as diesel.”
Tackling commercial risks
A key theme running through the NANO Nuclear strategy is addressing commercial risk. Walker observes: “I think where NANO became very different from the competition very quickly is that when we were looking to de-risk the final product, we realised that there were massive capability gaps in the United States for actually being able to build a reactor because of deficiencies with the associated supply chains.” Walker cites some reactor designs which rely on the development of novel fuels to operate. This and similar issues prompted a different methodology from NANO. “We looked at that and thought ‘that’s a major impediment to actually developing a reactor’ and so we spoke to the Department of Energy and the national labs about solutions for this problem. They were fairly certain that if we were to pursue a fuel fabrication facility, as an example, it would be the only Cat II facility of its kind in the United States, and it would de-risk our project, but it would also open up a different line of business for us, a new opportunity. So that’s what we did.”
Working with industry professionals and the national laboratories, NANO sourced land and a technical team to design a fuel fabrication facility. In terms of fuel fabrication, NANO plans to buy in enriched uranium and then fabricate that into fuel assemblies. “Currently there is a US facility planned for HALEU TRISO, but the majority of the HALEU [High Assay Low Enriched Uranium] market is not going to be TRISO and our reactors don’t use that so it’s going to have to be something we do by ourselves. There might be opportunities for collaboration with some of the bigger players as we begin this, but we were quite surprised that they weren’t really developing in this area themselves. The thing with HALEU is we know it’s going to happen, and everyone is designing around that, but it’s still an anticipated industry essentially. To build out these facilities is a big commitment. While there are big nuclear fuel players, I don’t think many of them are building micro- reactors or SMRs, so they wouldn’t be de-risking their own final product by building these capabilities for themselves.”
Clearly, many SMRs and different reactor designs are looking at HALEU which potentially represents a market and a different revenue stream for NANO. “The advantage here is that it’s building back the US infrastructure, but it’s also providing us with a revenue stream that comes online even before the micro-reactor is deployed”, says Walker.
He argues that even if both the company’s reactors are ultimately unsuccessful, this approach offers a model for continued profitable operations. “If anybody wins the SMR micro-reactor race ahead of us, that’s great, because what we want to do is be able to supply everybody. The fuels business will be independent of NANO’s reactors, but all SMR companies, all micro-reactors, if DoD, DoE, the national labs need HALEU, which they certainly do, and they’ll need it fabricated, that’s something we want to provide. We want to make that business as widely available to everybody as possible. If somebody comes up with a better reactor it’s actually wonderful that they’ve done that, because it has more commercial potential and if it has more commercial potential and they’re manufacturing more of these things then that’s more fuel for us to fabricate.”
This diversified, vertically integrated business model also extends to transportation. Walker explains that work on the fuel fabrication business led to another opportunity for NANO: “We also realised that we needed a way to move commercial quantities of HALEU fuels. Again, we spoke to the DoE, and we found out that there had been technology that had been funded by the Department and the national labs had built, but funding had stopped. There was a technology that was just sitting on the shelf so we went out and bought it and that put us in the lead, essentially, in that race to create a way to actually move commercial quantities of fuel around the country.”
The technology that had originally been designed was of a basket type for the movement of uranium dioxide, but NANO is adapting it so it can also move uranium hexafluoride, nitride, hydride, and uranium metal for example. “The idea here is that it needs to be as spread as wide commercially as possible and to move all of these different types of fuel. All the modified baskets will just go into a cask system, which we’ll also own the IP for,” Walker says, adding: “Then we have an entire transportation technology system.”
Again, Walker envisages a large market for nuclear transportation services, saying: “Say you’ve got an enrichment company and they produce HALEU. How do they move the enriched UF6 to the deconversion facility? How do they move it from deconversion to fuel fabrication? How do they move it from fuel fabrication facility to the customer where they fuel the reactor, or to the deployment site where they refuel? All of those different elements are things the transportation business will cater to.” He adds: “A lot of people are talking about transporting fuelled reactors and then taking them away again and refuelling them when they’re needed but it’s not that the business wouldn’t be able to function if people just fuelled their reactor at their manufacturing facility and moved it to the deployment site. There would still need to be transportation throughout that entire network and so we’re looking to try and place the company in those areas to provide that service.”
De-risking this fuel transportation technology business has also involved recruiting the former president of global operations from UPS. As Walker explains: “The challenge here is that while we’re fairly developed with the technology, the actual business of running a logistics company is something I’m very happy to admit that I know nothing about. Once you start talking to them, you realise how very complicated a business like that is and so bringing in people who are more expert is, I think, essential.”
Transportation issues have also influenced the design of the as-supplied NANO reactors in another nod to reducing commercial risks. In this example the NANO reactors will be transported separately from the fuel. Walker explains why: “The reason why we didn’t go ourselves for a fuelled reactor is because currently, unless regulations change, it’s not permitted – you can’t take a critically configured reactor by road. The regulations don’t allow for it unless there’s a major change. That’s big gamble so it’s probably more sensible to work around the current regulations and not hope that they just change in your favour.”

Next steps to commercialisation
Walker acknowledges that there is still work to do to secure a licensed design. He says: “Typically, companies that are in this phase will do two years of physical testing and demonstration work, and might modify the design slightly given real-world feedback. Once that’s done, we’ll go into the licensing process at that point. When we clear that, it’ll be about 2030. Alongside that licensing process, we’ll be building out our manufacturing facilities and it looks likely we’ll be building those in Tennessee. We’ve identified land packages for that manufacturing operation, as well as where we would site the fuel fabrication facility and the transportation business.”
Whatever the ultimate fate of its microreactor designs though NANO’s ambitious approach to develop a vertically integrated nuclear start-up company is novel, a point Walker emphasises: “NANO diversified fairly quickly and that’s where we really began to differ from everybody else.” He also points to the financing arrangements for NANO as another point of differentiation between it and other nuclear start-ups in the small reactor space. “The other thing we realised is if we structure the company properly, if we go to become public early and come out very small, we can grow with the public and avoid the problems where companies list and their valuation is very high, and then if it drops down it makes very difficult to raise further money. By structuring it in this way, this gives us financing routes for the future, so we can keep funding increasing, because the costs are going to increase linearly as we go along. This gives us a mechanism to keep that funding going. That separates us because a lot of these projects can be very dependent on government money and grants, and it’s not a good tactic for long-term development, just because you don’t know when they’re coming, you don’t know if you’re going to win, and if you don’t win those things, you’re stuck.”
Another key difference is that the NANO business model is energy as a service rather than reactor supply. Nonetheless, it’s likely that the initial customers will come from industry and so will focus on process heat rather than electricity. Both designs will have the option to include the turbine and switch between thermal and electric output.
ZEUS operates at high temperatures and around 5 MWth and 1.5 MWe so is well suited to production processes or heat for industry. Whereas ODIN operates at a much lower temperatures which allows for less salt degradation, thermal stress and allows more off the shelf components. ODIN is around 4 MWth and just about 1 MWe.
Walker says: “The intention originally was that we would pursue both because it would de-risk eventual success but they ended up really catering to almost different areas and being quite complimentary. You can see industrial operations where you could deploy both to meet different requirements and so we’re still currently pursuing them both and, barring any major technological interventions, we’ll keep doing that up to a point and maybe we will just take both of them all the way up to licensing.
He notes that the ODIN design may go to licensing a bit earlier because it uses off-the-shelf components but ZEUS is expected to follow on quickly after that. Both designs are on roughly the same time frame, with a goal for commercial launch in around 2030. “It might be that ZUES comes online maybe a year later but it wouldn’t be a significant difference because they started at approximately the same time and the licensing period is fairly standard. The NRC estimates that licensing for a micro-reactor design is about a 40-month process and it is possible that they could modify regulations or introduce a process that is more ideally suited to a micro-reactor design. However, for the NRC to introduce such an amendment may take years. It’s always safer to err on the side of what’s currently permissible over what could be,” says Walker.
Looking ahead, Walker believes it is likely the two reactors will be deployed differently with applications like remote industry, space or for high heat using ZEUS while for island communities, or military bases where you need consistent power, the ODIN reactor makes more sense. As Walker concludes: “The ODIN reactor might be the more widely commercially developed and deployed product with ZUES being more targeted at more specific areas that it’s just a bit more ideally suited for.” Whether either, both or none of the NANO reactor designs emerge as commercial prospects doesn’t really seem to matter though, Walker is confident that in any eventuality the company will be a success.