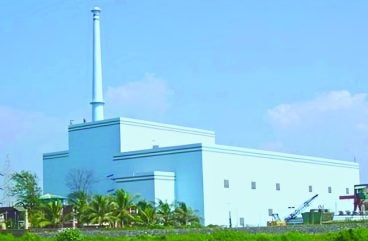
Tarapur Atomic Power Station (TAPS), located in Tarapur, Maharashtra state, is among the largest nuclear power stations in India with an installed capacity of 1400 MW. The facility is operated by the Nuclear Power Corporation of India Limited (NPCIL).
In March 2020 both reactors at the Tarapur nuclear power plant underwent a shutdown, which stemmed from a critical leakage incident in the recirculation piping. Upon investigation of the weld joints of the primary recirculation loops, NPCIL identified Intergranular Stress Corrosion Cracking (IGSCC) as the root cause of the leakage. IGSCC is a form of corrosion cracking that occurs along the grain boundaries of the heat affected zone (HAZ) of austenitic steel welds or in the cold worked zone.
With this discovery, NPCIL made the decision to replace the primary recirculation loops along with a few other class-1 piping elements. Having embarked on a first-of-its- kind endeavour for replacement of primary recirculation piping at TAPS Units 1 & 2 this unprecedented project aims to revitalise the nation’s first nuclear power facility, which initially commenced operations back in 1969.
NPCIL entrusted the works to CORE Energy Systems Ltd., a Mumbai-based EPC contractor specialising in such projects. Subsequently the contract for the complete replacement of the primary recirculation piping was awarded to CORE Energy Systems Ltd., who were deemed the most competitive technically qualified contractor.
The project entailed addressing significant challenges, including working in a radioactive zone, executing detailed engineering of cutting, disposal of the existing piping and replacement with pipes of highly specialised materials all in a constricted work area.
The forged pipes and fittings to be used for the replacement work are being manufactured conforming to ASME SA 312 SS 316 LN with stringent chemistry and dimensional control. The entire reactor building interiors have been scanned using high precision 3D scanning technology, a 1:1 mock-up structure has been erected to recreate the reactor environment. Most of the planning and training activities are being undertaken using these innovative aids. The radiation exposure to workers has been minimised by the use of automated orbital cutting and orbital welding machines and the application of shielding measures. The project has also required CORE to develop systems for decontamination, safe end shielding plugs and insertion mechanisms, positional monitoring systems and many more innovations that reflect CORE’s commitment towards the Government of India’s push to develop indigenous technologies.
A spokesperson from CORE remarked: “We anticipate the completion of this project as per the planned schedule and are confident that the refurbishment will extend the Tarapur power plant’s lifespan by a decade.”
It is anticipated that the cost of refurbishment is likely to be recovered within a year of the power plant’s renewed operations.
India demonstrates its ability to handle such complex projects through indigenous companies, bolstering the nation’s ability to develop technology locally. Such initiatives are pivotal in strengthening India’s sustainability and enhancing the reliability of its energy infrastructure. By investing in these projects, India underscores the value of homegrown engineering firms, entrusting them to play a critical role in shaping the nation’s nuclear capabilities.