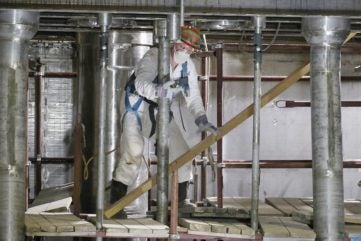
At Russia’s Mayak Production Association in Ozersk work is continuing to install a sixth furnace at the radio chemical plant. The new electric furnace – the EP 250/6 – is part of a major upgrade of Mayak’s technology for high-level waste (HLW) processing involving vitrification. Its previous electric furnace – the EP-500/5 – was closed in 2020 after four years of operation during which 141m curies of activity contained in liquid solutions obtained from used fuel was vitrified.
In 2021 Mayak developed design documentation for two new unique types of melter to provide its radiochemical facility with modern HLW vitrification units. These are an EP-250/6 type melter for producing alumino-phosphate glass and a small-sized EPM type melter for producing borosilicate glass. The designs were developed based on previous experience of operating five EP-500 electric furnaces, as well as prototypes that had been tested on the experimental stands of the enterprise.
The new vitrification complex at the radiochemical plant was designed by JSC RaoProekt. The design capacity of the new complex is 490 tonnes of vitrified HLW a year. Commissioning was scheduled for 2028 but work is ahead of schedule.
“The work is progressing even slightly ahead of schedule,” emphasised Vladimir Polisadin, a specialist at Mayak’s Repair & Construction Department (RSU – Remontno-Stroitelnomu Upravleniyu). “The immediate main task is to install the technological equipment inside the furnace. Of course, there are difficulties: Previously furnaces were built from the top using a crane, but currently in the workshop the work is carried out almost manually. It is an honour that the construction of such a complex and unique facility was entrusted to RSU and, in particular, to our site. I think that after the construction of the furnace is completed, our workers will be “academicians” of the installation business.”
The construction of the EP 250/6 is under the strict supervision of specialists from the industrial safety service, the capital construction department, the Mayak design and construction department, and the radiochemical plant. “The management of the enterprise has set strict deadlines for putting the facility into operation,” noted Alexander Akintsev, Head of the Department for Development & Reconstruction of Production at the radiochemical plant. “The entire team of specialists involved in the construction of the furnace works tirelessly. The pace of construction is good: most of the main equipment has been installed and the furnace is taking on its design shape.”
The main difference of the new vitrification complex is that, in addition to time-tested electric furnaces of the EP-500 type, it will use a removable small-sized melter. At the end of its service life, it will be remotely disassembled, packed into containers and transferred to centralised storage at the Federal State Unitary Enterprise National Operator for Radioactive Waste Management, and a new melter will be installed in its place. The construction of the new facility at Mayak PA is part of the Federal Target Programme Ensuring Nuclear and Radiation Safety for 2016-2020 and for the Period until 2030.
The original vitrification complex was put into commercial operation in 1987. The vitrification method involves melting alumino-phosphate glass in electric furnaces where it is mixed with solutions of radioactive waste and fluxing additives. The glass melt containing HLW is then poured into special containers where it solidifies to form of a mechanically strong and chemically stable monolith. The filled containers are placed in metal cases. After three containers are filled, the canister is closed with a lid, sealed and transported to the special storage site for vitrified HLW.
The last EP-500/5 electric furnace was put into operation at the end of 2016 in workshop 4 of the radiochemical plant. The previous four electric furnaces were mothballed at the installation site after their service life expired. The new complex will include a unified transport and technological system associated with the main technological redistribution of radiochemical production. All the ceramic melters in it will be replaceable – when they are worked out, they will be dismantled, fragmented, packed in containers and transferred to storage at the Federal State Unitary Enterprise National Operator RAO.
The new complex is designed to solve environmental problems related to the immobilisation of liquid radioactive waste that was accumulated in the early years of the enterprise. It will use two types of ceramic melters: high-performance ones, such as EP-250 electric furnaces for producing alumino-phosphate glass, and small ones for producing borosilicate glass. The high-performance ones are intended for processing liquid HLW accumulated from the previous activities of the enterprise, as well as from processing special types of used nuclear fuel. The small ones will be used for vitrification of waste from reprocessing used fuel from power reactors.”
Mayak was originally established in the late 1940s to produce plutonium for the Soviet nuclear industry. The main directions of the current activities include: fulfilment of the state defence order for the production of components of nuclear weapons; transportation and processing of used fuel; production and sale of isotope products; mechanical engineering and instrument making; research and production activities; and the solution of nuclear legacy problems.
Like weapons production sites worldwide, there was little attention to safety in the early years and unregulated disposal of HLW left large areas highly contaminated. This was exacerbated in 1957 by the explosion of a waste tank. Mayak has since faced a huge remediation task, with which it is making positive headway. In 2015, after years of work and huge expense it completed the mothballing and remediation of Lake Karachai on the site where HLW had been dumped and which had been described by the Washington, DC-based Worldwatch Institute as the most polluted spot on Earth.
Akintsev explained that, instead of constructing and equipping a new building, the new electric furnace will be mounted in the same building, where its predecessors are mothballed, as part of the technical re-equipment of the existing vitrification complex. This will not only reduce the time needed to put the furnace into operation, but also significantly save the resources of the enterprise.
Researched and written by Judith Perera