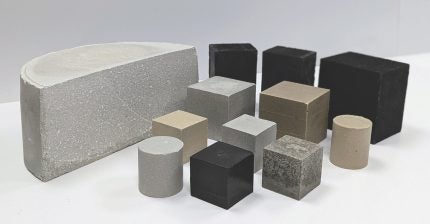
As nuclear energy continues to scale into the future as part of the global energy mix, the continuing challenge of how to deal with problematic radioactive waste becomes only more pressing. Nuclear waste immobilisation is part of the process of safely transporting and storing these nuclear materials. This process transforms radioactive waste into a compact form through solidification and encapsulation, reducing the potential for migration or spreading of radionuclides into the environment during transportation and disposal.
Immobilisation of waste is attained by its chemical absorption into the structure of a suitable matrix, such as cement, glass, or a polymeric composite, preventing leachate escape from the matrix. The use of cement-base slurries the favoured method in some countries to encapsulate and immobilise a wide range of hazardous compounds, but the most common, Portland cement (PC), exhibits some limitations when aiming to encapsulate some key types of wastes. For instance, Portland cement may not be the most suitable candidate to encapsulate radioactive wastes since its hydration process is highly exothermic and this can exacerbate the activity of radionuclides rather than assisting to immobilise them.
In addition, Portland cement pastes cured at high temperatures tend to develop a more porous microstructure which limits their long-term quality as an immobilisation agent. Likewise, Portland cement does not perform very well when encapsulating organic wastes, but the lack of compatibility is of a different nature. Most organic compounds will inhibit the hydration of Portland cement leading to a very inhomogeneous and not chemically bonded product.
Although these limitations can be to some extent addressed through the addition of other materials such as inert fillers, the economic and supply chain implications arising from this solution bring about problems of their own. A clear demand is therefore present for an appropriate alternative to existing cements for nuclear waste encapsulation.
MIDAR® geopolymer technology
Lucideon’s MIDAR® technology brings together a unique blend of materials science, formulation technologies, and expertise to provide the optimum performing geopolymer solution across a range of applications.
MIDAR® is a geopolymer technology that uses a low-temperature chemical reaction to consolidate aluminosilicates and form a robust body with high strength and chemical stability. The material is classified as an alkali-activated cement / geopolymer that relies on minimally processed natural materials or industrial by-products to achieve a significantly lower carbon footprint than Portland cement.
Incorporating a solid or liquid waste stream into the inorganic solid matrix formed during the reaction results in a material that functions as an encapsulation and immobilisation agent, qualifying it as a suitable candidate for use as a waste encapsulant.
Lucideon’s application of this geoploymer technology for the purpose of nuclear waste encapsulation has been supported by Innovate UK for commercial scale-up under the name MALLETTM (MIDAR®-Augmented Lower-Carbon Lower-Cost Encapsulation Technique). The Foundation Industries Sustainability Consortium (FISC) has identified a range of key workstreams as particularly high-impact areas of research for the cement, metal, glass, ceramic, paper, and chemicals industries to deliver global innovation in low-carbon resource-efficient sustainable solutions. Lucideon is taking the lead in several of these workstreams, including geopolymer scale-up. A core output of the geopolymer scale-up workstream is the establishment of a dedicated geopolymer facility, designed from the ground up to house a comprehensive selection of formulation and scale-up equipment, that brings a new level of scalability and consistency to geopolymer development.
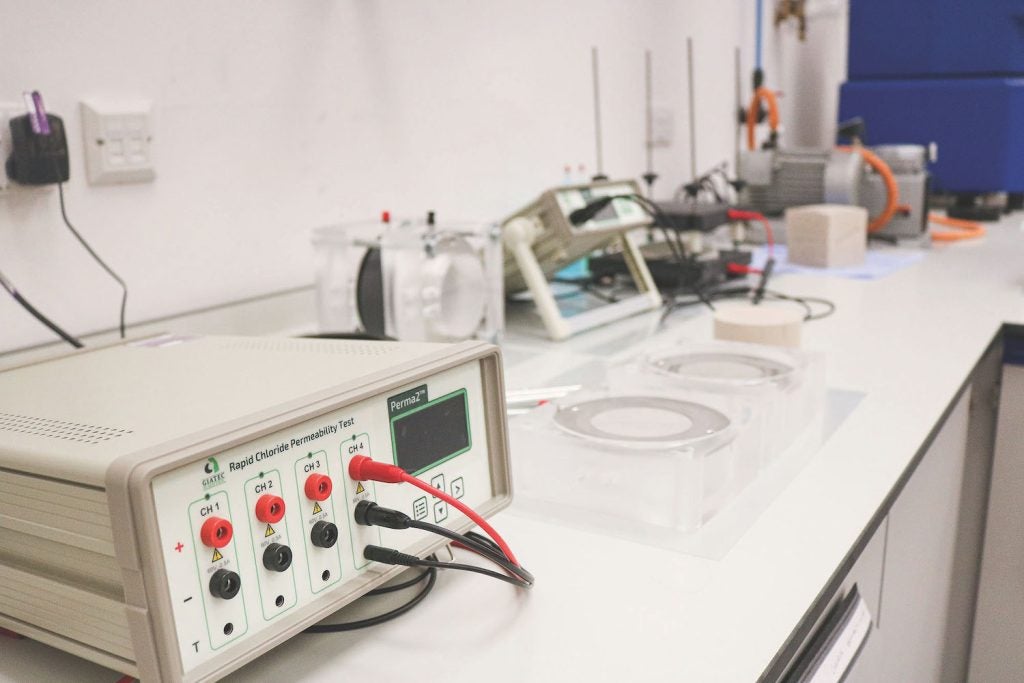
The equipment purchasing and building of this facility are proceeding under FISC’s first project, ‘Economic Materials Innovation for the Sustainable and Efficient Use of Resources’ (EconoMISER). EconoMISER is funded by Innovate UK as part of the Transformation Foundation Industries (TFI) Challenge and is intended to build on existing innovation capability of the FISC partners. Some of the activities were facilitated by Innovate UK Knowledge Transfer Network and were partially funded via the UK Research and Innovation (UKRI) Challenge Fund through Innovate UK.
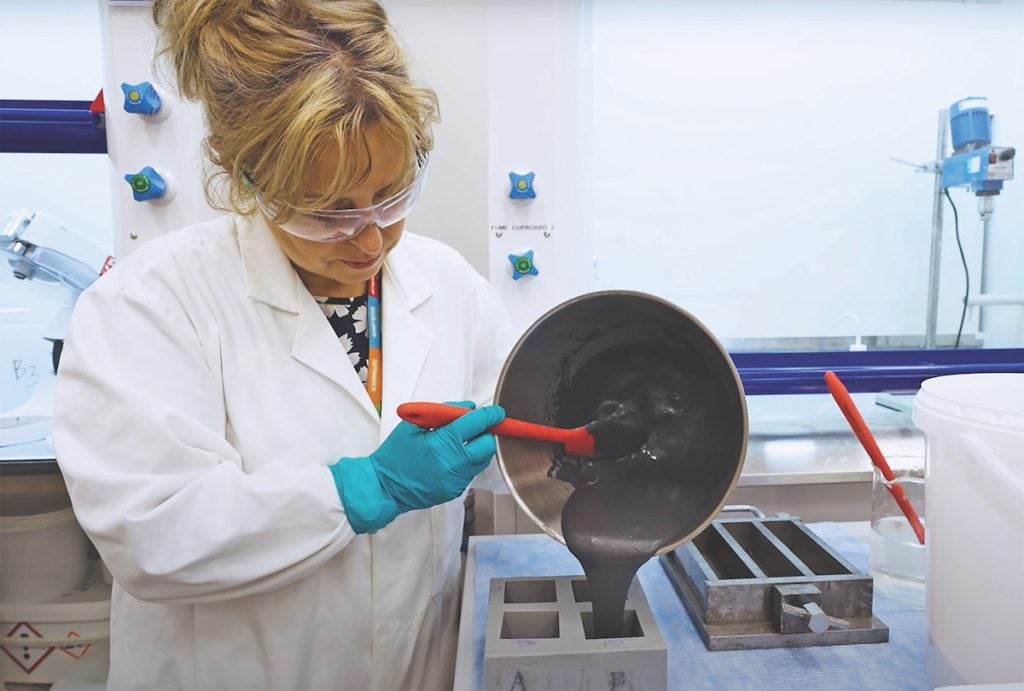
The scale-up work is underpinned by a comprehensive suite of testing and characterisation capabilities co-located onsite, centralising the essential analysis processes for geopolymer technologies and minimising transit delays to allow for rapid iteration and reformulation based on test findings.
The new facilities will expand capabilities in geopolymer formulation for various forms and functions, accelerate scale-up from laboratory to demonstration level, and ease the burden of achieving acceptable criteria and standards through improved characterisation capabilities for product properties and durability.
One of the ways in which this facility can be used to address the Foundation Industries’ sustainability challenge is through the acceleration of TRL progression for encapsulant technologies.
MALLETTM
MALLETTM was developed in response to several nuclear industry waste disposal challenges, most significantly low percentage waste loading rates, or in some instances providing a solution where no viable route for disposal presently exists. The geopolymer increases loading rates through formulations that fully encapsulate waste homogenously throughout the matrix.
The properties of aluminosilicate sources and the mix formulation in developing geopolymers are among the key factors that greatly affect the resulting immobilisation and encapsulation efficiency. The passing criteria of the immobilisation technology depends on the following factors:
- Type, amount and chemical composition of waste: the waste loading needs to contain a significant amount (20-50%) for minimising the volume and reduce the cost
- Storage and disposal facility of waste: compatibility with the disposal environment conditions, stored container, etc.
- Durability and stability during leachability conditions
- Chemical stability between the cement and radioactive waste without formation of another phase or compound
- Reduction in risk of releasing radionuclides from damaged containers due to corrosion, accidents, natural disasters, or human interference for example.
Among other factors, leachability resistance plays an important role when the geopolymer-encapsulated radioactive waste matrix is exposed to various conditions such as alkaline buffer solution, sulphate and phosphate solutions, acid attacks, and various forms of water such as groundwater and sea water. Wastes encapsulated within a geopolymer matrix have shown good resistance to leaching.
The raw materials used with MALLETTM are not reliant on scarce source materials such as Ground Granulated Blast-furnace Slag (GGBS) or Pulverised Fuel Ash (PFA), which are becoming more difficult to source to produce traditional nuclear waste cementation products.
Ultimately, the objective is to enable nuclear waste owners to process oils, graphite, zeolites, and sludges into a passive matrix that maximises waste loading and reduces overall waste disposal volumes, therefore providing a simple batch process with little process variability and a significantly lower carbon footprint.
Performance and characterisation
Considering waste acceptance criteria for existing waste disposal routes, the resulting product was monitored and characterised to provide qualitative evidence of performance. The results evidenced a final product which:
- Is leach resistant, demonstrating no release of chemicals from the waste or matrix
- Is fully set and free from cracking; the casting and curing procedures were carried out at room temperature (RT)
- Is dimensionally and physically stable at RT before and after leaching in various solutions including deionised water, buffer solution with high pH, and organic solvent
- Has acceptable compressive strength (>0.4 MPa, in many cases much greater) before and after leaching procedures
- Has controlled porosity, voids, and homogeneity
- Allows the product to be pumped very easily directly into containers and enables application of pour-on/ infiltration techniques through its low viscosity
- Generates a minimal exotherm during the mixing, curing and setting Irradiation testing was undertaken on a range of samples, demonstrating end-product integrity after 1 MGy total absorbed dose of gamma radiation from Co 60. MALLETTM’s technical innovation is delivered by the geopolymer formulations and encapsulation methods. With existing encapsulation methods, relatively low levels of difficult-to-treat waste materials are encapsulated, usually at loading rate levels between 2% and 30%. The technical innovations exhibited by MALLETTM have allowed this to be increased to up to 70%, dependant on waste form.
Traditional encapsulation methods using Portland cement-based grouts result in disposal packages that are 3.3 times the volume of the raw waste volume. In contrast, MALLETTM reduces this volume to 1.4 times, significantly lowering disposal costs. Evidence demonstrates that the geopolymer offers a potentially superior method of managing intermediate and low-level waste streams, including oils, graphite, zeolites, sludges, and ashes.
Solutions to the challenge of problematic legacy waste are now taking shape that are within realistic and acceptable parameters of environmental sustainability and financial viability. Prioritising scale-up of these solutions offers a golden opportunity to advance how we treat legacy and future wastes; organisations such as FISC and programmes such as EconoMISER will play a significant role in facilitating this development.
By reducing the amount of material required for encapsulation and utilizing a low-energy manufacturing process, MALLETTM achieves a significant reduction in carbon emissions compared to traditional methods. As a replacement to Portland Cement for nuclear waste encapsulation, MALLETTM has the potential to reduce the carbon impact of cementation processes, considerably reduce storage costs and provide security of supply.
The flexibility of the developed formulations also allows the material to be adapted for broader nuclear applications such as stable, corrosion and fire-resistant structural materials for long-term storage.