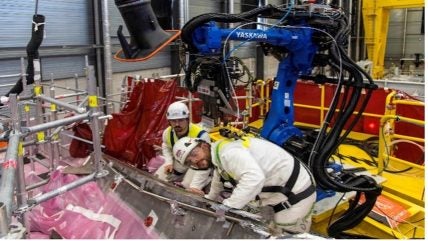
Work is progressing to address defects identified in two key tokamak components during assembly of the International Thermonuclear Experimental Reactor (ITER), under construction in France. Defects were identified in the thermal shields and the vacuum vessel sectors.
Three months after repair operations were launched on vacuum vessel sector #8, which was most affected by dimensional non-conformities of the vacuum vessel sectors already delivered to ITER. Some 90% of metal build-up and half of pre-machining tests and controls are now completed. Machining has just started with two tools; three others are scheduled to join in the coming weeks. The team in charge of repairs expects to complete operations by the end of the year.
At one end of the repair process is an automatic welding robot worth several hundred thousand euros, adapted and equipped for the specific task of metal filling and build-up. At the other end are standard ultra-fine-grain scratch pads. In between, a whole range of tools is used to progressively correct the faulty sections of the interface areas (the bevels) of vacuum vessel sector #8.
Following almost three months of metal build-up, machining has started on the bevels of vacuum vessel sector #8. Two machining tools, driven by computer numerical control are currently at work. Three others are scheduled to join in the coming weeks.
Pass after pass, progressing at an average speed of 10 centimetres per minute, the fully mechanised welding machine¹ has now completed its task on one side of sector #8. The mechanised process, however, represents only 25% of the total metal build-up required. For reasons of accessibility and flexibility, the remaining 75% must be done manually.
Even after the metal build-up is done, the nominal geometry will not be achieved. Excess metal must be removed – first by manual grinding, then by using machining tools working in parallel in different regions of the bevel. This is after having performed different kinds of non-destructive tests (including visual, liquid penetrant, and ultrasound). Although the machining tools are driven by computer digital control (Computer Aided Manufacturing, CAM) based on precise metrology and as-designed 3D models, the quality of the repair is deemed satisfactorily controlled only after a last series of “manual dressing” operations – first with a file, then with sandpaper, and eventually with scratch pads.
However, this is only half of the required task. In its present position, lying like a stranded whale in the former Cryostat Workshop, vacuum vessel #8 presents only two of its four 30-metre-long, D-shaped bevels (the outer and inner shell bevels). In order to make the other side accessible for repair, the component will need to be “flipped – a massive and delicate handling operation to lift and turn over a 440-tonne piece of steel.