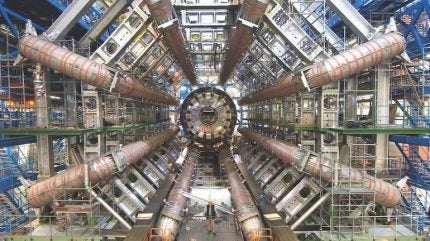
Nickel-based alloys like Inconel or Hastelloy are used in many nuclear reactors. Their use, however, presents a number of challenges. Yinbin Miao, principal materials scientist at the US Department of Energy’s (DOE) Argonne National Laboratory, tells NEi: “Nickel is a critical material and it’s not only costly and hard to transport, but also it is produced in geopolitically unstable areas.” Recognising these issues, Argonne researchers established a two-year investigation programme to discover alternatives. Miao says: “The goal of this research is to try to reduce the reliance on nickel for the nuclear industry, at least for advanced reactor technologies, by figuring out a way to reduce the use of nickel alloys”. He adds a crucial observation: “We noticed in many applications, like in molten salt reactors, Inconel or Hastelloy nickel alloys were selected not because of the high mechanical performance characteristics, but because of the corrosion resistance. In that case, it’s a surface performance, not a bulk material performance that is critical, so we can use a coating with similar or better performance compared to nickel and use a less expensive substrate, like stainless steel, or even cheaper mild steel.” Miao continues: “Because the coating is relatively thin compared to the bulk material the cost is not very sensitive to the kind of material we’re using. Even if we use some expensive material for the coating, the total cost will still be limited.”
While reducing the use of nickel alloy components and replacing these materials with mild steel or stainless steel that is coated with a highly corrosion-resistant layers will not eliminate nickel, it will reduce its demand for the nuclear sector.
With this in mind, the team set about trying to discover alternatives to nickel with comparable strength, corrosion resistance and a structure that can withstand the harsh environments found inside nuclear reactors.
Funded by Argonne’s Laboratory Directed Research and Development programme the project was launched to not only develop coatings but also to establish a framework to accelerate discovery of new materials appropriate for the highly demanding applications found in the nuclear power space.
A multi-physics model
While the solution would provide an equivalent if not better performance compared to Inconel, for example, implementing new material solutions for the nuclear industry is difficult. Says Miao: “We’re trying to figure out a way to combine different components, including simulation, experiments, and cost analysis to have this framework to accelerate this process.” He adds: “The focus of this project was to not only develop this kind of coating solution, but also develop a framework to help evaluate and optimize this coating solution. We also needed to provide a demonstration case”.
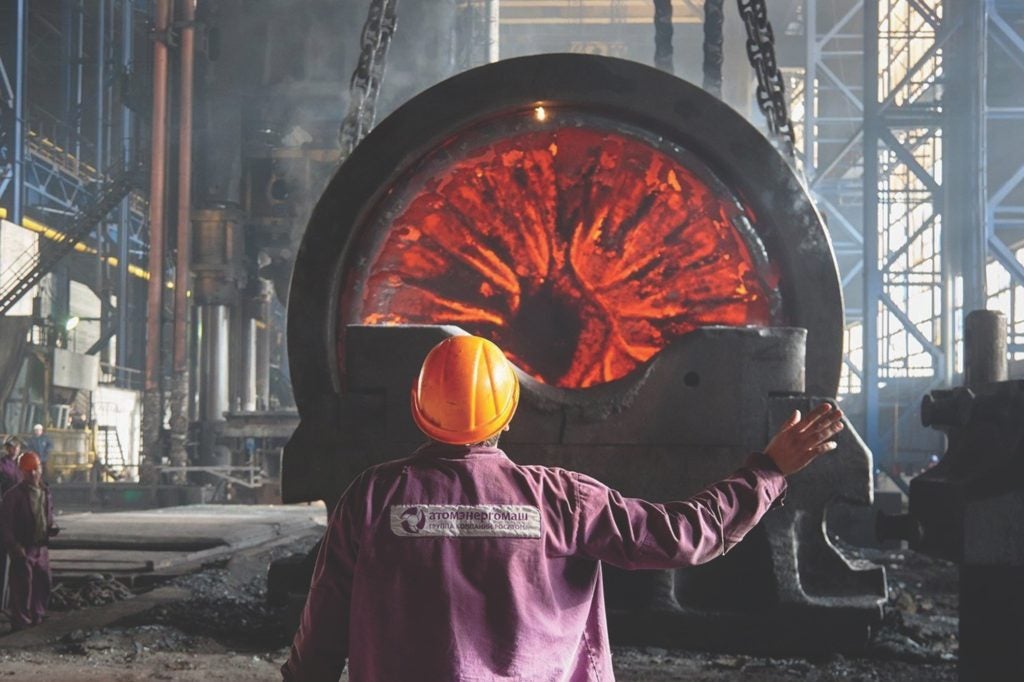
The team selected a molten salt reactor as the proposed demonstration case given the high anti-corrosion performance needed to operate in such an environment. “The idea is we need some material with high performance for an advanced nuclear reactor, like molten salt,” he says. Using a multi physics approach to drive experimentation and determine which potential combinations or alloys of coatings could be used, the Argonne approach aims to address multiple challenges by finding alternative materials that have the high corrosion resistance suitable for these environments with high temperature, pressure, and potentially neutron flux, all while in the presence of corrosive molten salts.
Miao explains: “First, we need to identify a coating solution that can meet all the comprehensive set of performance criteria we need for molten salt fast reactors. We need to identify what kind of material would work and then also other coating parameters, like how thick the coating needs to be and if we have multi-layer coating, the thickness of each layer and then the exact composition we need to use.”
He contrasts the multi-physics model with the conventional approach to managing this kind of materials challenge, saying: “People typically just use a matrix of conditions which could be a very big set of data on a group of examples. Samples are prepared and then experimentation is used to find the optimal one. What we are trying to do is to develop a framework that would benefit from a multi-physical model, establishing a reactor model which can mimic the actual operating conditions for the coating – in this case that would be a molten salt reactor – and trying to put all the relevant information into the model. That model is also informed in real time by experimental data.”
The framework assesses the qualities of different alloys and immediately rejects those that do not meet key criteria, such as resistance to the corrosive environment. This eliminates large parts of the experimentation that would otherwise be required. The idea is this multi-physical model, together with the experiment data, will help to make the experimentation phase more efficient so that the optimal solution can be found faster with fewer experiments.
“After we identify the best solution, we can also use the same framework to further collect data and demonstrate the effectiveness of the solution so it will also help us with the qualification and the licensing process,” adds Miao
Taking coating to the next level
Having run the programme for close to two years, the researchers have succeeded in identifying a novel coating material and have also now demonstrated that the new material could indeed withstand reactor conditions and resist the molten salt corrosive environment. However, the research framework goes beyond discovery of the basic coating material. Miao explains: “We are actually developing the coating rather than use a commercially-available coating and are aiming to optimise the composition. It’s not adding new elements, we’re more adjusting the percentage of different elements. We know that some combination of elements will work but we don’t know what the best composition is. We also want to know the optimal thickness to sustain the stress and also the corrosion.” He continues: “Currently we are focusing on how thick each layer of coating needs to be, for example, one micron or two microns. We put everything into the model which is informed by previous experimental data. We know, for example, that a one micron-thick layer would be under high stress and that it cannot endure the reactor conditions so we may need a two or more micron-thick coating instead. These are existing coating materials that have already been tested in some respects as a potential choice but that haven’t been applied in this environment.” The goal then is to develop a coating that can withstand the corrosive high temperature molten salt environment under reactor conditions, including the challenges of thermal expansion.
Following a programme of analysis and experimentation developing promising compositions the next phase of the research will be testing the materials in the Argonne Tandem Linac Accelerator System (ATLAS) device.
“We have already identified an optimal composition for the coating and then we have testing, not only after we identify it, before it too. For example, we also use testing to help screen the optimal solution by testing thermal stress and resistance by thermocycling. We also tested with molten salt at high temperature to test corrosion resistance. We also put it into an ionic irradiation materials testing station at the ATLAS called the [ATLAS Material Irradiation Station] AMIS as an accelerated way to see the radiation resistance of our coating,” says Miao.
The prime national facility for nuclear structure research, ATLAS is the world’s first superconducting linear accelerator for heavy ions at energies in the vicinity of the Coulomb barrier while the AMIS uses low-energy ion beams to emulate material damage in nuclear reactors. Damage that could take years in a reactor environment could in principle be reproduced in few days using the ion accelerator.
“All that information is also used to inform the model so that with the existing knowledge from this experiment we can further accelerate the future optimisation and the qualification for those coatings,” says Miao.
Commercial coatings
While the goal of the research is to reduce the volume of nickel required, the programme also focuses on costs, as Miao explains: “The project’s main focus is trying to develop an evaluation framework that should be extendable to different coatings and different reactor types. It is a multi-phase model as it has an experimental part and it has also a cost-effectiveness analysis part. When we reduce the reliance on nickel, we also reduce the cost because nickel is expensive but depositing a coating is also more expensive than not having a coating so we want to consider both aspects to make sure the final solution would still be profitable depending on the different coating deposition process such as vapor deposition or electroplating. We’re trying to consider the cost at the very beginning to make sure that whatever solution we provide would still be beneficial.”
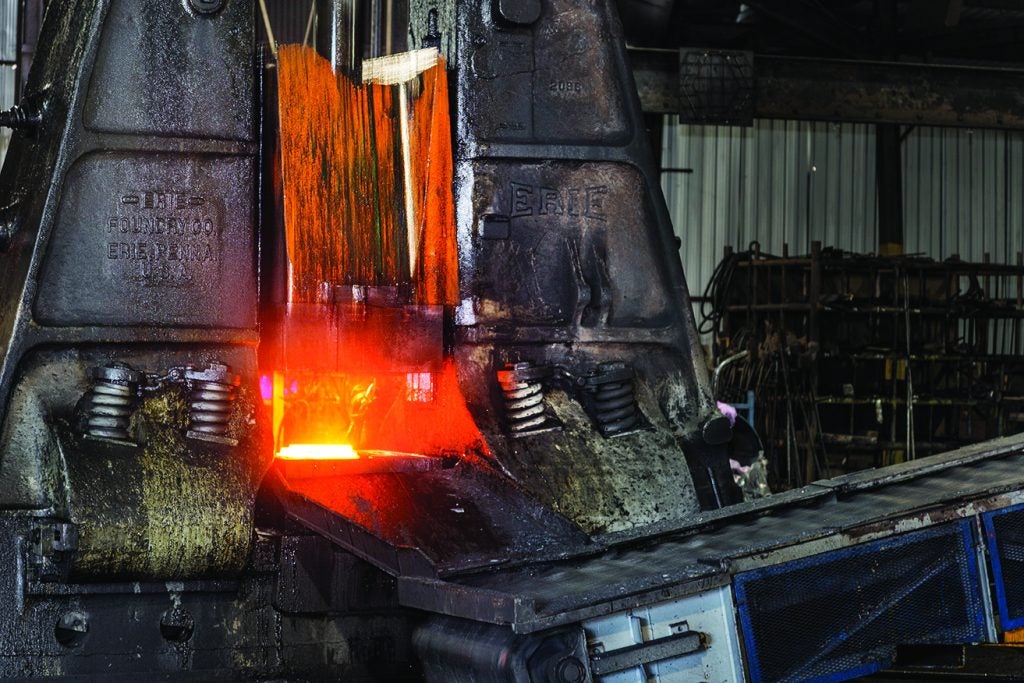
The experimental phases are also feeding back into the data set to make an improved framework for further research. In the future, coatings with different compositions could also be assessed using the model: “Adding a new element would be a future aspect of improvement for this current framework,” says Miao.
Another likely avenue for further research is the use of AI in assessing a large data set, although Miao is clear that their approach is not using AI or machine learning to derive results currently. “So far, we haven’t used AI, but that’s a potential for the future because we developed our framework based on a US Department of Energy and Office of Nuclear Energy code. It is AI ready and it can use AI in the future but our data is not large enough to give us a prominent benefit when using AI, but in the future when the database grows AI is possible”.
As a two-year project the initial Argonne National Laboratory-directed R&D programme is now close to completion, but the team are actively approaching government programmes as well as industry vendors to try to continue to develop this approach and add more details to the database. The team will also file a patent for the new coating material and is currently seeking more funding to further investigate its properties.
“In the future, we’re trying to approach not only government programmes to obtain further funding, we’re also trying to approach private sector nuclear industry vendors to use our tool so that when we have an actual advanced reactor model, which is developed either by a government agency or by a private sector company, we can replace the concept model with the actual model people are trying to develop. It’s a different model and will give you a different operating condition, but we can still use the existing data and the framework to test whether the coating solution will still perform within the conditions found in the actual reactor design. If yes, that’s good news. If not, we still have this tool set to further optimise and find a new solution for the specific reactor conditions,” says Miao, adding: “We already have a demonstration case to identify a coating solution for the concept molten salt reactor, but we might also have different reactor designs like lead-cooled designs”.
Although mainly multi-physics based, the framework tool that has been developed is also likely to serve future regulatory appraisals too by combining different elements and also connect it with experimental data and the cost-effectiveness analysis. Says Miao: “We’re trying to use those tools, combine them and use them to establish the framework. Then you take that whole, real-world model of an existing actual reactor design and that’s what goes to the NRC where they assess that for safety, repeatability and all those other characteristics that they are interested in.”
Using existing approaches, trying to quantify new materials for reactors can take decades, this framework model is therefore expected to shorten this process by establishing that a coating meets the quite narrow requirements of reactor conditions already and so a relatively short and truncated testing programme is sufficient to validate the material.
Miao concludes: “We wanted a demonstration case to show our potential users that we have a framework that already works for one solution, the molten salt reactor and coating. From the Laboratory Directed Research and Development (LDRD) project point of view, we’re wrapping it up, but for the framework, as well as the coating we have identified, we’re trying to secure more funding to continue developing it”.