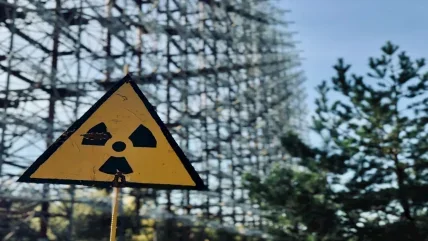
Exposure to radiation is detrimental to the function of electronic equipment. Magics Instruments has developed chips that are highly resistant to radiation – up to 1MGy. This technology offers an opportunity to use of electronics in interventions during nuclear accidents, reactor inspections, dismantling of old nuclear power plants, disposal of radioactive waste, space travel missions and new developments such as nuclear fusion reactors. Magics’ radiation-hardened sensing technologies offer intelligence and automation capabilities for remote handling tools in hazardous environments.
How are electronics affected by radiation?
Radiation has two main effects on electronics: single event effects and total ionising dose effects.
Single event effects are caused by highly energetic particles, which can cause bit flips in digital circuits or voltage spikes in analogue circuits.
The total ionizing dose is an accumulating effect, of the dose rate and the total time a circuit is exposed to radiation. Ionising radiation creates electron-hole pairs in the electronics, changing the transistor parameters and eventually destroying them. It can also cause leakage currents between circuits.
Options for radiation hardening
Magics Instruments is a spin-off company from KU Leuven, MICAS research group, KU Leuven Technology Campus Geel, KU Leuven / AdvISe research group, and SCK•CEN (the Belgium Nuclear Research Centre). It offers standard rad-hard electronic solutions or customised integrated circuit design services.
There are three options when it comes to radiation hardening.
Most off-the-shelf electronics can only maintain its functionality in radioactive environments with tungsten or lead shielding. This is heavy and bulky, making design, installation and replacement complex and expensive.
Another option is to use dedicated, non-mainstream processes, but these are expensive and difficult to maintain.
The third option is radiation hardening by design – using a combination of circuit and layout techniques to harden electronic circuits, which also means virtually any circuits can be made.
ITER remote handling work
Magics is working on the international ITER fusion project, providing electronics for remote handling equipment that operates in high radiation environments in and around the tokamak.
In general, the radiation-sensitive electronic boards are in control cubicles that are located in green zones and connect to the actuators and sensors through long cables. However, it is some front-end electronics that will be located close to the actuators and sensors. In the Divertor Remote Handling System it is estimated that these components will face gamma radiation up to 300Gy/h (in-vessel) and a total dose of 1MGy.
Magics has developed a demonstrator that allows sensor networks to be installed in high-radiation environments. This work results from a contract supported by Fusion for Energy, the European Union organisation managing Europe’s contribution to ITER, and it has been licensed to be used in the market.
The instrumentation module presented in Figure 1 above consists of state-of-the-art integrated circuits developed in-house. All the integrated circuits have been assessed and characterised in doses up to 1MGy. The first block in the signal chain is a low-offset (1μV), low-noise instrumentation amplifier and it has a programmable gain between eight and 256. This amplifier is followed by a high precision 16-bit ADC. Its main function is to digitise the amplified signal coming from the amplifier. The digital data stream from the ADC is fed to a signal processor and the bus. The signal processor conditions the signals and implements all digital logic for a master-slave bus protocol.
The sensor nodes in the network act as slaves. The master nodes control all the slave nodes and receive all the data. In turn, the master nodes send all the data to a computer, server or laptop where the sensor data is visualised. The module can be used to read multiple environmental parameters (temperature, pressure, radiation etc) and link sensors in one single network.
Most of the components are now successfully tested up to 1MGy and the final design is due to be completed around October 2017.
The module provides a first step to introduce digital connected networks in the nuclear industry. This unlocks a wide range of possibilities such as severe accident monitoring, efficient remote handling tools and inspections or monitoring in high radiation environments.
About the author
Jens Verbeeck is managing director of Magics Instruments