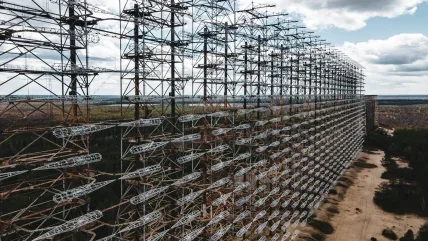
Nuclear energy has a key role to play in ensuring we can continue to meet the world’s growing demand for electricity. In fact, the IEA predicts that nuclear power generation will see a 75% increase by 2050.
Yet regions like Europe are expected to face significant growing pains as the expansion of nuclear generation picks up pace. This will include not only the challenge of building new facilities, but also how to handle more widespread decommissioning and maintenance work. Many existing plants are ageing, built as long ago as the 1970s with a typical lifespan of around 40 to 50 years. These assets will need to be replaced in the coming decades for the continent to meet its energy transition goals.
The growing need for decommissioning and maintenance should be met most efficiently and – above all – safely. A major challenge that will be increasingly faced by nuclear projects is the sheer variety of different facilities that were built from the 1970s onwards. This means that there is no one methodology that can be applied across all sites. This is not simply a case of construction and layout, but also the data available – it is quite common to have to work with a lack of detailed information on older plants built some 50 years ago or more. This means that more work is needed early in each project to ensure the logistic methodologies will work within the site.
This early involvement also gives suppliers the best chance of developing bespoke equipment within the project timeframe. Problems can often be solved by addressing them laterally. It can be highly undesirable or simply impossible to move modules through the plant itself. Instead, alternative options should be considered such as cutting a hole in the roof of the containment building, lifting the vessel out using a crane or gantry, or creating a bespoke engineering solution that has not been used before.
Overcoming complex logistics
A case in point comes from the Lingen Nuclear Power plant in Germany, where as part of a wider decommissioning project Mammoet removed two steam converters from the control area of the facility, under very tight space restrictions.
During the execution phase, these needed to be moved vertically and then tilted to a horizontal orientation, before being lifted from the building to waiting transportation below. Mammoet’s engineering team created a combined lifting and transport solution with strand jacks, designed specifically for this working environment.
Due to the high radiation protection requirements on site, the entire tooling, equipment and 100 tonnes of fabricated steelwork had to pass special radiation checks before being brought into the control area. This considerable time factor had to be taken into account in the planning so that the overall deadline could still be met.
Prior to execution, all core components including the support strap, temporary lifting device and the skidding beam for the transverse skidding operation were subjected to a thorough load test. After successful acceptance by the authorities, work could begin in the control area.
First, the support strap had to be installed onto the first steam converter. Due to its installation position in a narrow housing, the upright-positioned component was difficult to access and first had to be jacked up with hydraulic climbing jacks and moved laterally.
After the support strap was attached, the temporary lifting device took over the steam converter. It was pushed out of the housing centimetre by centimetre with a skidding device and finally placed precisely onto a skidding track. The now horizontal steam converter was then rotated by 90 degrees and lowered.
After removal, the steam converter was lifted from this portal gantry in a tandem operation, with a 1200-tonne and a 750-tonne mobile crane, and loaded for transport on the power plant site. The second steam converter followed the same procedure.
In this position, the large component could be removed from the control area to a gantry built several stories high against the building exterior. Due to interfering edges and the narrow diameter of the opening, only a few centimetres of clearance were available to perform the operation.
Bringing new, more efficient thinking
Although the nuclear industry has its own specific demands and stringent standards that must be respected, it is also important to remember that many of the logistical challenges this sector faces are in many ways similar to those found in the wider energy sector or in civil engineering projects. The danger to the nuclear industry is if a wide variety of opinion is not sought. This approach limits the range of potential experience available. In that case there will be a lower chance of finding new, more efficient solutions that may have been developed in other industries and can be adapted to meet the specialist demands of the nuclear sector. There might be a potential for cross-application, for example, in sectors where a particular methodology or piece of equipment may not be the norm.
A good example of this comes from the installation of the new sarcophagus at Chornobyl, where the original emergency shelter covering the reactor needed to be replaced with a more permanent solution. The scale of this task was huge – requiring the construction and installation of a shelter weighing nearly 35,000 tonnes, which would be the largest land-based movable structure ever built. Putting this into perspective, at 165 metres long, 260 metres wide, and 110 metres tall the structure is big enough to completely house Notre Dame Cathedral in Paris. An innovative approach and tailor-made equipment were needed to deal with such size and weight and deliver it with millimetre precision.
To provide a clean and safe working area, the construction site was located some 330 meters from the reactor and a new foundation was laid. It allowed personnel to work continuously and save construction time. To complete the project as safely and efficiently as possible a lifting system and software to control up to 60 strand jacks simultaneously and a skidding system consisting of 116 skid shoes with a capacity of 703 tonnes each was developed. With both sides of the skidding system 260 metres apart, the movement was fully monitored, controlled, and synchronised. Each half of the arch was lifted in three stages, allowing the crew to work at lower heights. At each stage, elements were added before raising the arch further. Once the first half was raised, it was skidded away to make room for the assembly of the second half. Upon completion, the first one was skidded back to the construction area where both halves were connected to finalise the construction.
This approach had many advantages. Alongside the efficiency and safety benefits of reduced working at height, only half the jacking capacity was needed compared to raising the arch in one piece, greatly reducing costs. Last, but not least, remotely-operated equipment prevented the crew from having to work in the contaminated area, making this project a textbook example of safe, efficient, and out-of-the-box engineering.
The nuclear industry is facing a time of change as it scales up to play an even bigger role in the energy transition. With decommissioning and maintenance work on the increase, it’s important that we make the most of the expertise – in both engineered heavy lifting and across other disciplines – to ensure these challenging projects can be completed as safely and promptly as possible.
Author: Jan Kleijn, Mammoet COO