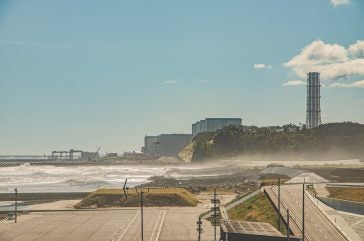
There is broad agreement that nuclear power is an important part of the transition to clean energy. Indeed, it is widely believed that swiftly scaling up nuclear power capacity could address not only the challenges of climate change but could also tackle energy poverty and promote economic development.
However, public confidence in the safety of nuclear power plants is less certain. There have been only two major reactor accidents in the history of civil nuclear power – Chornobyl and Fukushima Daiichi – during 18,500 cumulative reactor-years of commercial nuclear power operation in 36 countries but these events remain in the public consciousness. While the former accident was traceable to flawed design and inadequate training, the sequence of events that led to the failure of the reactor cooling systems and the subsequent explosion at Fukushima were more complex and triggered by natural phenomena, specifically an earthquake and tsunami.

As extreme natural events are likely to become more frequent and more severe due to climate change, it is imperative that safety-critical systems in nuclear power plants are capable of functioning under abnormal circumstances.
The sequence of events at Fukushima have been examined in detail by nuclear regulatory bodies and the scientific community so that lessons can be learned to improve legislation and safety processes. Investigating the performance of the physical equipment and the role that engineering can play in improving safe operation, in particular the role of pumping equipment in the reactor core isolation cooling (RCIC) system led to an improved pump design.
Cause and effect
The catastrophic failure at Fukushima began with a severe seismic event that occurred on 11 March 2011 at 14.46 (local time) off the Japanese coast near Honshu Island, approximately 250 miles north of Tokyo. With a magnitude of M9.0, the Tohoku-Chihou-Taiheiyo-Oki earthquake was the largest ever observed in Japan and the fourth largest recorded earthquake in the world. The Great East Japan Earthquake, as it came to be known, also triggered a tsunami that flooded more than 200 square miles of coastal land. The earthquake and tsunami initiated a severe nuclear accident at the Fukushima Daiichi Nuclear Power Station, operated by the Tokyo Electric Power Company (TEPCO).
Immediately after the earthquake, offsite power was lost to all three units in operation at the power station, leading to automatic start-up of emergency diesel generators. Approximately 40 minutes later the tsunami struck. Waves measuring in excess of 14m high hit the site and flooded the power station. This caused the shutdown of emergency diesel generators at 15.41, leading to station black-out (SBO).
Despite emergency diesel generators and battery backups, the cooling supply was lost to Unit 1 within several hours of the earthquake-tsunami event. Similarly, Unit 2 lost cooling after 71 hours and Unit 3 lost cooling after 36 hours, leading to hydrogen build-up and subsequent explosions in all three units. This represented an unprecedented nuclear event and was rated as a Level 7 “Major Accident” on the International Nuclear and Radiological Event Scale (INES) on 12 April 2011.
Learning lessons
Emergency preparedness and response management, as well as procedures for planning for the management of a severe accident, were completely updated as an outcome of the Fukushima incident. Weaknesses in plant design were addressed, particularly the assumption that there would never be an interruption in electrical power at a nuclear power plant for more than a short period. The possibility of several reactors at the same facility suffering a crisis at the same time now had to be considered, together with the possibility of a nuclear accident occurring at the same time as a major natural disaster.
Many of the conclusions were by no means unique to Japan. Consequently, other countries responded to the accident with measures that included carrying out ‘stress tests’ to reassess the design of nuclear power plants against site-specific extreme natural hazards, installing additional backup sources of electrical power and supplies of water, and strengthening the protection of plants against extreme external events, including terrorist attack.
From an engineering perspective, the loss of AC power (due to earthquake) and DC power (due to tsunami) was a primary concern because it rendered the High Pressure Core Injection (HPCI) systems and the Reactor Core Isolation Cooling (RCIC) systems to fail in less than 48 hours. All the reactors at Fukushima stopped operation automatically when the earthquake motion was detected. This in turn
led to the stoppage of the main feed water pumps. Failure of the water injection system over these extended periods was a key reason why the Fukushima accident developed to a point where explosion was inevitable. The preliminary investigations and subsequent reports following the Fukushima incident considered several pumping solutions.
Pumps and nuclear safety
The role of flow control equipment in the safe operation of nuclear power stations cannot be underestimated. Pumps form one of the most critical elements in a nuclear plant. Large-capacity pumps and high-pressure pumps used in domestic PWR nuclear power plants include reactor (primary) coolant pumps, charging pumps with safety functions, safety injection pumps and residual heat removal pumps in the nuclear island, as well as main feedwater pumps, condensate pumps and circulating water pumps in the turbine island.
The most safety-significant systems in the case of a station black-out are the RCIC systems for boiling water reactors (BWRs) and the auxiliary feedwater (AFW) system for pressurised water reactors (PWRs). The steam-driven water pump in these systems is typically the frontline component that addresses SBO and provides core heat removal.
Proper operation of the AFW system in a PWR traditionally requires DC power from a station battery, steam from the steam generators and an adequate supply of secondary plant water. The total amount of current draw on the station battery can be a limiting factor in determining the duration of SBO coping.
Coping without power
Clyde Union Pumps (CUP), part of Celeros Flow Technology, has concentrated its efforts on improving the design of its turbine/pump set for RCIC applications. In addition, it has worked with Westinghouse to incorporate such turbine/ pump sets to provide an improved plant AFW system that addresses many of the concerns raised by the Fukushima accident.
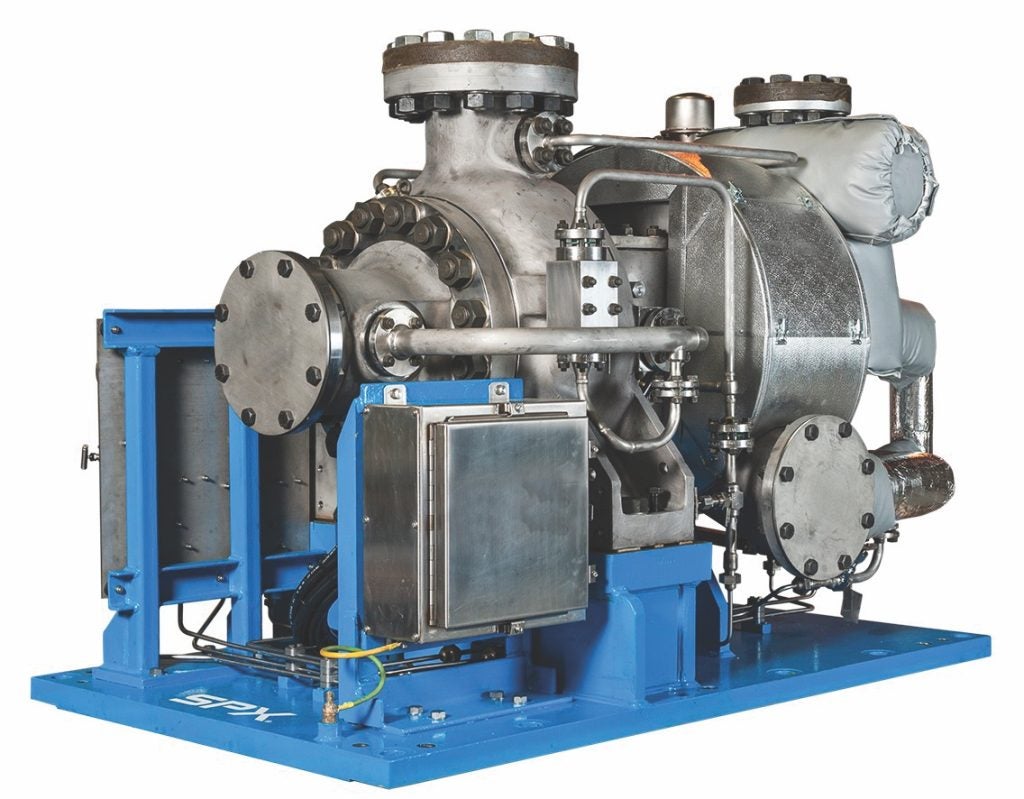
The pump is a single wheel steam turbine, two-stage pump designed to ASME III Class 2 & 3 requirements. Both the turbine and impellers are mounted on a rigid shaft, supported by a central bearing assembly integral within a monobloc turbine/pump casing.
It is one-third to one-half the size of a conventional pump and turbine unit, which makes it ideal for congested nuclear islands where space is at a premium. This compact design will also withstand water slugs in the steam line.
The pump provides required performance pertaining to discharge head, flow rates and required steam conditions. It has a capacity of up to 350m3/hr (1550 USgpm) and a delivery up to 1300m (4265 ft). This pump therefore exceeds existing PWR installation requirements (1200 psig and 900+ gpm), and the set is extendable for power uprates.
These pumps are designed to operate with no external lubrication, no external cooling water, no drive coupling, no barometric tank or vacuum pump and – more importantly – no electrical connections. These units also incorporate self-contained turbine governor/controls and overspeed trip mechanisms within one package.
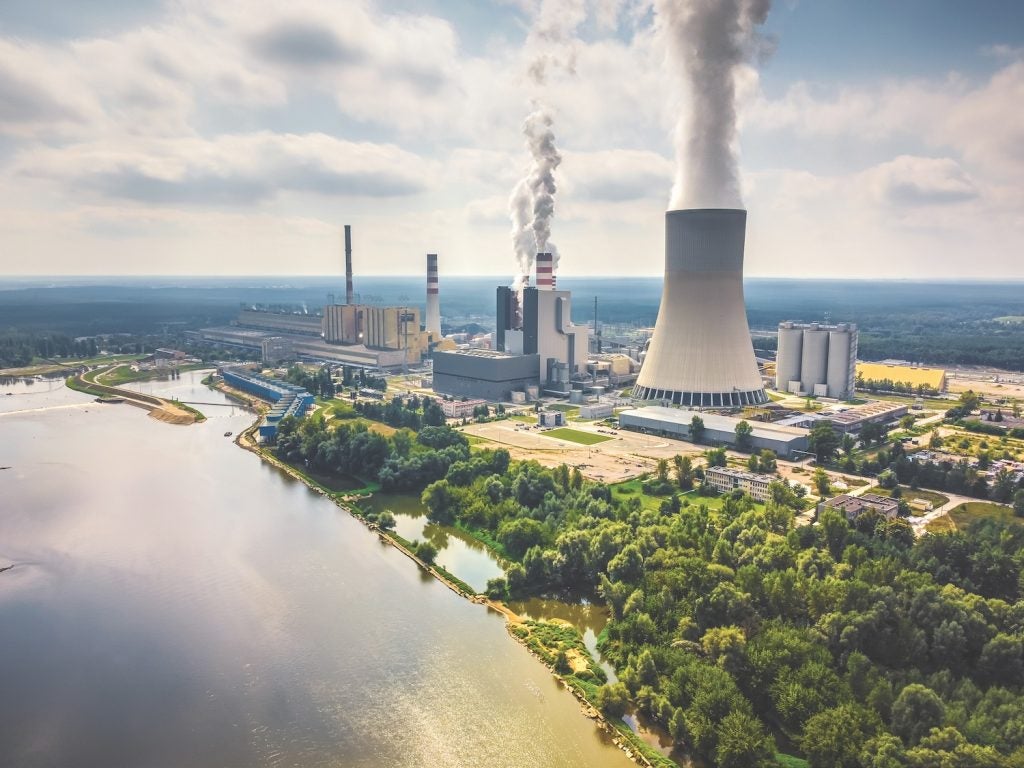
However, the main feature of the redesigned CUP pump in the context of improved nuclear safety post-Fukushima is its extended coping capability under SBO conditions without supporting services (AC or DC supply). Even the control at partial flow is much simpler, since there is no need for repeated operator intervention to adjust the flow. This saves precious time and enables personnel to concentrate on other essential items in the event of a SBO or other incident.
The pump has a single casing designed with no shaft protrusions, enabling it to start and operate while fully submerged. Tsting has shown that it will maintain safety performance and continue to operate with no adverse effects or detrimental changes to performance for a minimum of eight hours. During this time, the pump can be started and stopped, with no detriments to its performance.
Power plant owners, operators, original equipment manufacturers (OEM), designers and regulators today are acutely aware of the potential plant vulnerabilities that can lead to a complete loss of a unit’s electrical power due to multiple natural phenomena. Climate change means that the likelihood of combined extreme weather events is growing, making the ability to ‘ride out the storm’ a safety-critical design consideration.
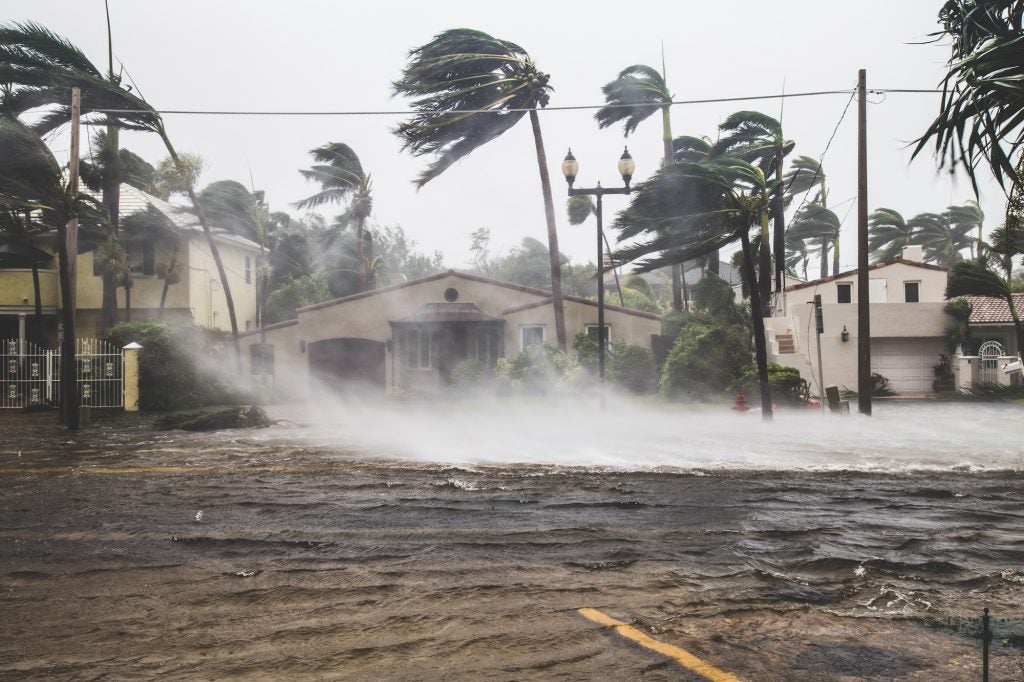
The relationship between cooling systems and the availability of uninterrupted power supply in case of SBO should be of primary importance to nuclear power plant design and operation.
Author: Pascal Montel, Celeros Flow Technology