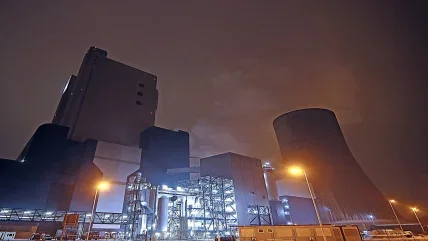
In the current century, building up a reliable fleet of High-Temperature Small Modular Reactors (HT-SMRs) could be a key strategy to tackle climate change by replacing fossil fuel generated process heat. Due to the continuously increasing demand for energy in line with the rise of the world-wide average temperature, nuclear power is again being taken under serious consideration as a clean energy source, especially in relation to international efforts in reducing overall CO2 emissions.
As of now, High-Temperature Reactor (HTR) technology is being promoted by several countries and companies, especially due to its unique inherent safety features. These features are based on the reactor concept and the fuel design itself. Accordingly, many of the small modular reactor (SMR) designs that are emerging are also based on the HTR technology.
HT-SMRs
The dream of reducing the complexity of a nuclear power plant while increasing its safety is reflected in the concept of the Small Modular Reactor (SMR). The key focus lies on reducing the size of the reactor (compared with established designs). When this requirement is fulfilled, modularity, standardisation and increased design integration can be addressed. A more integrated design results in reduced complexity and number of components. Standardisation includes the ability to deploy the reactor more flexibly with less site and grid restrictions.
Nearly all known reactor concepts from the established ones to Generation IV designs can be designed as SMRs. The International Atomic Energy Agency (IAEA) defines them as reactors of up to 300 MWe per module. Similar considerations apply to microreactors, which cover the power requirements below the SMR range.
The Generation IV design, which is meant to be the successor of the high-temperature gas-cooled reactor (HTGR), is the Very-High-Temperature Reactor (VHTR). Both HTGR and VHTR designs use graphite as a moderator and reflector while helium acts as the primary coolant. The main application of the VTHR is synchronous hydrogen and electricity generation. This is enabled by the higher possible outlet temperature: the HTGR reaches temperatures up to 750 °C, while VHTRs are expected to reach about 1000 °C.
The comparably high temperature of HT-SMRs opens the door to a variety of chemical processes, which are not feasible at lower temperatures. One example is the production of hydrogen using high-temperature water electrolysis. This allows fossil fuels substitution for process heat and tackles a large source of current CO2 emissions.
However, the technical advantages of HTRs and SMRs are worthless if safety concerns are not addressed. In addition to the inherent safety features of the SMR concept itself, there are HTR-specific advantages. SMR-specific inherent safety features are, generally speaking, based on the scaled-down design with less fissile material and less complexity.
Inherent safety features of the HTR design also come into play. One is the retention of fission products which is already ensured by the strict requirements to the HTR fuel specifications. TRISO fuel has the key feature that all fissile material is encapsulated in layers of durable silicon carbide (SiC) as well as pyrolytic carbon. Most importantly, core meltdown is practically impossible as the generated heat will intrinsically be able to passively dissipate into the environment even without an active helium cooling circuit. This is supported by the small core power density (compared to a PWR) and the large heat capacity and temperature stability of the graphite-based core itself.
HTR concepts are thus suitable to be combined with the technical advantages of the SMR, modularity, the potential for standardisation, increased design integration and reduced size. The availability of high-quality TRISO fuel is key to all HTRs. The HTR-typical high outlet temperatures can also be utilized for chemical or other industrial processes that have used fossil fuel generated heat so far.
HTR Fuel
The key component of each HTR is its tightly-specified fuel, which allows it to operate at full performance. Starting in the early 1960s, research and development of HTRs and their associated fuel was carried out in Europe and the USA. In Europe work was concentrated in the UK and Germany. The German HTR programme was initiated in the early 1960s as part of a civil nuclear development programme.
Within this programme, NUKEM, for example, was focused on the design of fuel elements, fuel specifications, the development of the fuel manufacturing processes and the actual production of HTR fuel. During the 1970s and 1980s NUKEM’s 100% subsidiary HOBEG (Hochtemperaturreaktor-Brennelement GmbH) manufactured and supplied more than 250,000 spherical fuel elements for the AVR experimental nuclear power plant at Jülich and more than 1,000,000 fuel elements for the Thorium High Temperature Reactor (THTR-300) at Hamm-Uentrop in Germany. Based on a highly systematic approach and the development of special quality control procedures for the production processes, fuel quality was continuously investigated and quality standards were established. Consequently, the highest level of HTR fuel quality with regard to minimum fission product release was achieved at this time – and still represents today’s quality standards.
The German experimental AVR (construction began in 1961) was the origin of succeeding pebble bed HTRs like the German THTR-300 (construction started in 1971), Chinese experimental reactor HTR-10 (construction began in 1995), its power producing predecessor HTR-PM (construction start 2012, 250 MWt per unit) and the South African PBMR (never constructed for financial reasons, 400 MWt). PBMR and the HTR-PM are examples of HT-SMRs and both use spherical fuel elements which are based on the HOBEG/NUKEM pebble manufacturing process.
As opposed to the ‘German-origin’ pebble bed reactors there is another concept based on cylindrical fuel compacts originating from the United Kingdom experimental Dragon Reactor (construction began in 1960, 20 MWt). Fuel compacts are arranged in a prismatic fuel assembly – usually a hexagonal graphite block with rod-shaped openings that are filled with the cylindrical fuel compacts.
HTR fuel in the form of a cylindrical compact or a spherical pebble consists of many small uranium kernels of about 0.5 mm in diameter. Uranium can either be in the form of pure uranium dioxide or uranium oxycarbide (UCO), which is a mixture of uranium dioxide with a certain fraction of uranium carbide.
While the German Thorium-High-Temperature-Reactor (THTR-300) utilised highly enriched uranium (HEU of 93 %) with added thorium, nowadays only uranium with lower enrichment levels is used due to the risk of proliferation. High-assay low enriched uranium (HALEU) is established as the term to describe uranium with enrichments ranging from 5% to 20%, which are usually used for modern advanced reactors, including HTRs.
Each uranium oxide or carbide kernel is coated with several layers of pyrolytic carbon (PyC) as well as a durable silicon carbide (SiC) layer. While the inner PyC layer is porous and capable of absorbing gaseous fission products, the dense outer PyC layers forms a barrier against fission product release. The SiC layer improves the mechanical strength of this barrier and thus the retention capacity for certain fission products.
The proven German TRISO spherical fuel, based on the NUKEM design, has demonstrated the best fission product release rate, particular at high temperatures. The enriched uranium TRISO particles were contained in a moulded graphite sphere. A NUKEM fuel sphere consists of approximately 9 g of uranium (about 15,000 TRISO-coated kernels) and has a diameter of 60 mm – the total mass of a fuel sphere is 210 g. In more recent projects NUKEM also developed cylindrical compact fuel based on the same TRISO fuel kernels. A cylindrical compact has a typical length of about 25 mm and 12 mm in diameter. It contains about 1.2 g of uranium per compact (about 3,000 TRISO-coated kernels).
HTR fuel production
The HTR fuel production process can be divided into four major fuel production process areas as well as two recycling areas for the recovery of uranium and other valuable materials from liquid process effluents, as well as out-of-specification solid fuel material.
In the Kernel Production Facility, fresh U3O8 powder is dissolved in nitric acid (HNO3) and mixed with special chemicals to a viscous ammonium di-uranate (ADU) solution. This solution is drip-cast (vibro-dropped) to form microspheres from many small droplets, which are then gelled, dried and calcined to form UO3. The UO3 is reduced to UO2 and sintered to a kernel. In the case of UCO kernels, a similar process is utilised to partly form uranium carbide.
Within the Coating Facility the kernels receive four coatings using a chemical vapour deposition (CVD) process to produce the TRISO-coated particles.
In the Fuel Compact (or Sphere) Production Facility, the TRISO-coated particles are overcoated with a layer of matrix graphite powder (MGP). The MGP-overcoated particles are dosed into pressing moulds together with additional matrix graphite powder according to the desired packing fraction, which determines the volumetric fraction of TRISO-coated particles relative to the total fuel element volume. The resulting fuel element is then carbonised and annealed in two consecutive furnaces – and thereby significantly hardened. In the case of a fuel sphere, this is the final fuel element production step and it is now ready to be introduced into a fuel assembly. Fuel compacts are first inserted into rod-shaped openings within a prismatic graphite block to yield the final fuel assembly.
Two recycling areas ensure that on the one hand almost no enriched uranium gets lost within the process and on the other hand the required chemicals are reused as often as possible. All traces of uranium from spent liquids are retrieved before they are discharged in the form of decontaminated waste-water.
The liquid effluents from the production processes are recycled and cleaned in the Effluent Treatment Facility. The main purpose is to recycle process liquids for reuse in the Kernel Production Facility. The scrap material from the different stages of the production process – including odd kernels, oddly coated kernels and off-specification fuel elements, as well as other uranium-containing materials – is recycled in the Uranium Recovery Facility to form U3O8, which is ready to be reused in the Kernel Production Facility.
The HTR fuel element production plant operates as a closed loop system that is designed to approach a 100% overall uranium yield from the raw material U3O8 to the final fuel compact or sphere; and therefore, approaching zero emission. The installed quality control procedures ensure that only in-specification intermediate products (uranium kernels and TRISO-coated particles) are used to manufacture the final fuel compact or sphere which has to pass a final quality control step.
Improvements in the HTR production plant
As it became evident in the early 2000s that there may be further interest in Pebble Bed Reactors, NUKEM reactivated the key personnel who were formerly responsible for the development and adjacent commercial operation of the HOBEG fuel production plant. This unique know-how had a significant role in the revival of the HTR fuel technology within NUKEM.
NUKEM developed its up-to-date TRISO fuel production process mainly during the design of the Pebble Bed Modular Reactor (PBMR) fuel Plant. The PBMR Fuel Plant (PFP), originally to be constructed near Johannesburg, was intended to fuel the first South African PBMR. The design of the reactor was based on the fuel specification and the equivalence of the fuel elements to the German fuel. This equivalence is important for the fuel qualification as the former NUKEM fuel has been long-term tested through irradiation tests in the German AVR reactor performed by the Research Centre Jülich in the 1980s.
In the course of more recent fuel plant designs, including PMBR, the process was continuously upgraded in accordance with the most advanced international norms and standards. In general, the focus shifted from administrative criticality safety control to technical control, i.e., the application of safe geometry as far as possible. The implementation of geometrically-safe equipment is superior compared to administrative measures to prevent the occurrence of a critical configuration of fissile material. Safe maximum equipment dimensions are determined for certain worst case scenarios – these limits are kept throughout the geometrically-safe areas of a nuclear fuel production plant.
A lot of equipment of the former NUKEM/HOBEG was redesigned with safe geometry considerations in place. The processes for the near-total recycling of uranium and chemicals, as well as for decontamination and purification of liquid and gaseous effluents were also developed in more recent fuel plant projects with respect to criticality safety and radiological protection.
The important revival of the existing TRISO fuel production know-how, the consideration of modern techniques and state-of-the-art safety requirements represents a challenging engineering task, which was accomplished by NUKEM at the end of the 2000s.
The main target of the current century is to continuously replace fossil fuel generated, CO2-heavy process heat. This can be achieved by building up a fleet of HTRs. Especially, the HT-SMR, which combines the advantages of the HTR with those of the SMR. SMRs can be deployed very flexibly in industrial cluster areas with high demand for process heat and NUKEM is ready to fuel the emerging HT-SMR fleet.
Authors: Dr. Marina Sokcic-Kostic, Principal Engineer; Dr. Georg Brähler, Technology Adviser; Karl Froschauer, Deputy Director Business Development & Sales; and Christopher Reiser, Physicist NUKEM Technologies