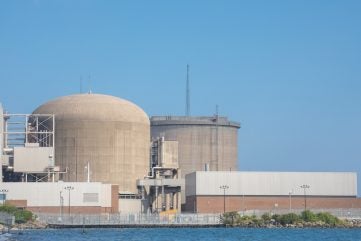
The radioisotope cobalt-60 that is manufactured in some nuclear reactors is used to sterilise approximately 40% of single use medical devices globally. These devices include items such as syringes, catheters, IV sets, surgical gloves, and gauze that used in a wide range of health care applications. A patient in surgery or receiving wound care or simply having a blood sample taken, is highly likely to be treated using products that have been sterilised using cobalt-60 in a process called irradiation. Other important uses of cobalt-60 include the non-invasive treatment of cancers and brain tumours, polymer processing, food treatment and environmental applications.
Cobalt-60 production and supply
Cobalt-60 is produced in a small number of reactors located in Argentina, Canada, China, India and Russia. The largest producers are Bruce Power and Ontario Power Generation (OPG) that operate CANDU type reactors in Canada. CANDU reactors are well suited for cobalt-60 production with the technology and processes established in the early 1970s with a history dating back to the 1950s.
CANDU reactors operate with stainless steel adjusters that shape the neutron flux for reactor operations. For cobalt-60 production, these stainless steel adjusters are replaced with adjusters containing bundles of metallic cobalt-59 slugs encapsulated into zirconium alloy capsules. The cobalt-59 adjusters are designed to replicate the neutron absorption characteristics of the stainless adjusters that they replace, so reactor operation is not impacted. While in the reactor core, the cobalt-59 atom absorbs one neutron to become cobalt-60 and over time the ratio of cobalt-60 to cobalt-59 increases. To achieve the required level of cobalt-60, the adjusters are activated over a period of 18-36 months.
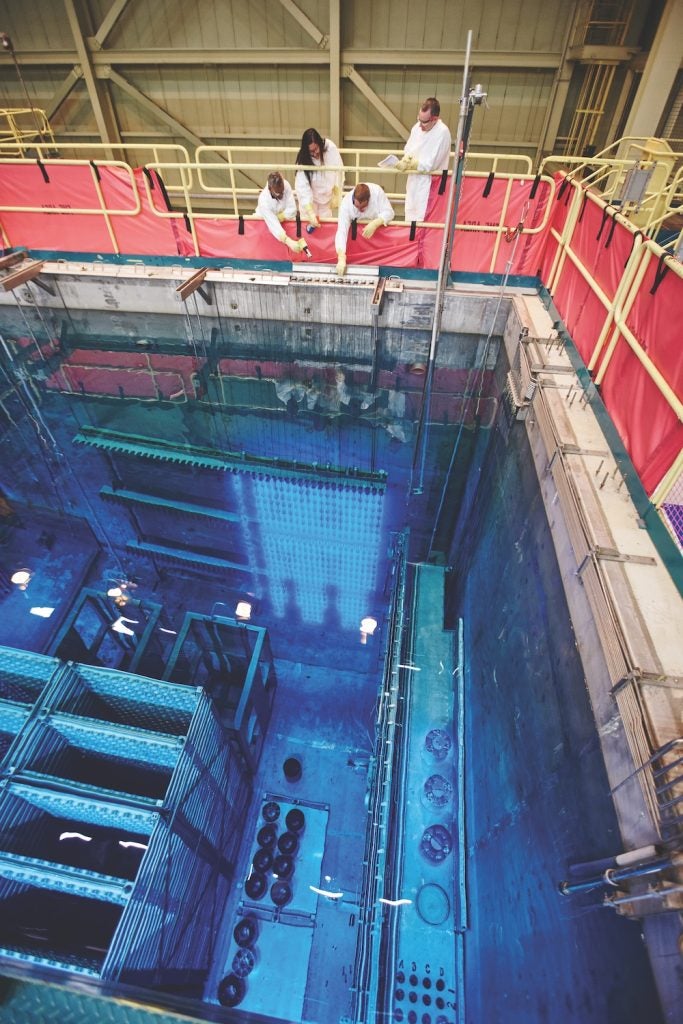
After this activation period, the adjusters are removed from the reactor during a routine maintenance outage. They are then transferred to a large pool at the reactor site where the adjusters are disassembled and the individual cobalt bundles are removed. These cobalt bundles are then shipped off site for processing and production of the finished product that is used for irradiation sterilisation.
The design of the finished product, sealed radiation sources, must comply with international standards and be licenced by national regulators, and their manufacture must be to the highest quality standards. Only a very few specialist companies have the necessary infrastructure to meet these requirements and supply to the global irradiation sterilisation industry. All of the cobalt-60 from the Bruce Power and OPG reactors, currently making up around 50% of global supply, is manufactured into sources by Nordion (Canada) Inc., the world’s largest supplier to the irradiation industry worldwide.
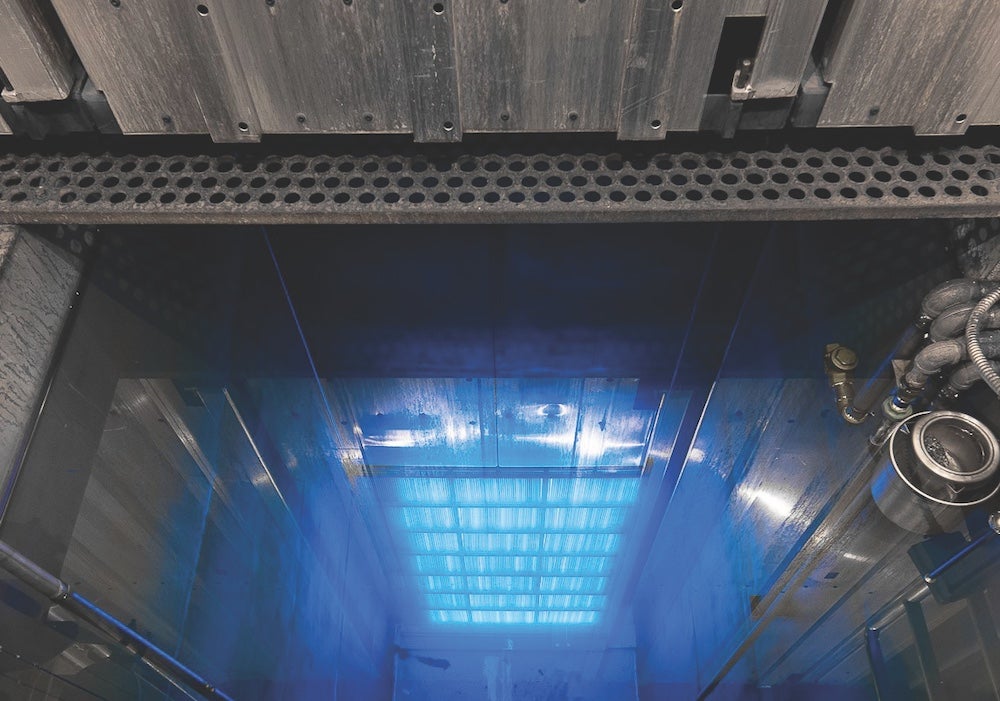
The supply of cobalt-60 from Russia, which represents about 25% of global supply, is also mostly through Nordion although some volume is supplied direct to the irradiation industry by JSC Isotope, an enterprise of Rosatom. Despite the challenges to continued supply from Russia in light of the current geopolitical situation, governments around the world appreciate the importance of cobalt-60 to global healthcare and have worked hard to ensure supply from Russia remains uninterrupted.
Most cobalt-60 produced in China and India and some from Argentina is used to supply regional markets. This is partly due to a desire to support local operators but also a result of licensing restrictions and transportation constraints.
Cobalt-60 supply and demand status
Irradiation technology is applied globally by a network of approximately three hundred irradiators using cobalt-60. Approximately 80% of this cobalt-60 usage is for the sterilisation of medical devices. In the US alone, it is estimated that some 16 billion devices are sterilised annually using cobalt-60.
The demand for sterilisation and, therefore, cobalt-60 is growing at rates not previously seen due to an increasing and ageing population, greater access to health care and the development of new devices that require sterilisation. Some sectors are experiencing double digit annual growth rates and in recent years, vaccine supply pressure concentrated the need for sterilisation and, in some cases, created a backlog.
Although cobalt-60 supply continues to increase, in recent years this growth has been out-paced by growth in demand. This is of concern to the healthcare sector that relies on irradiation sterilisation to enable it to meet growing patient treatment needs. Whilst alternatives to cobalt-60 technology are available for sterilisation, these alternatives do not have the capacity to meet existing demand or the infrastructure to enable rapid growth to meet future demand.
At a time of increasing sterilisation demand, there have been a few disruptions to cobalt-60 production. This includes the temporary shutdown for refurbishment of some existing cobalt-60 production reactors in Canada and Argentina, and periods of reduced supply from Russia. Reactor refurbishment is critical to extending the life of reactors by 25-30 years and but also creates opportunities to increase cobalt-60 production for the long term.
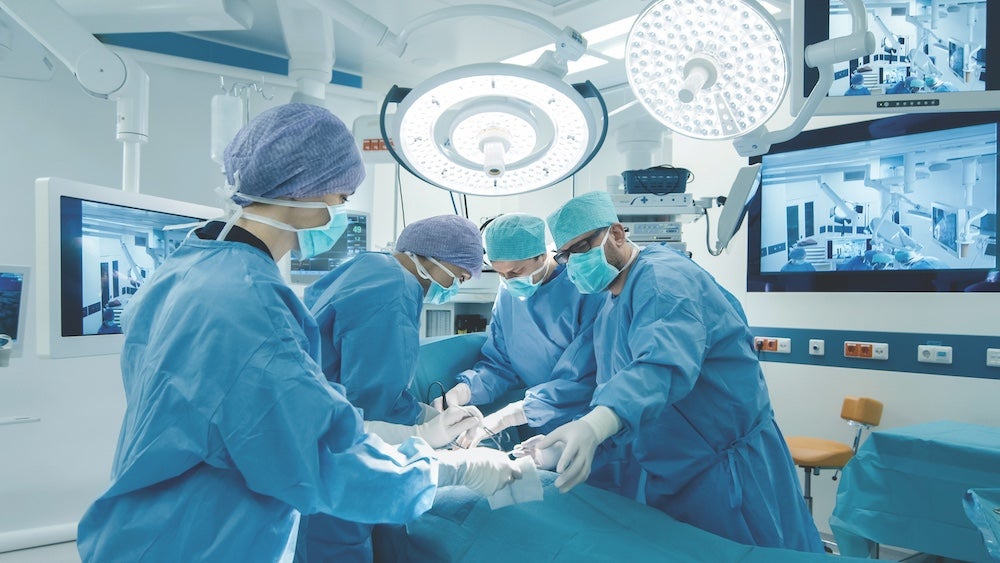
Reactor refurbishment and conversion for cobalt-60 production
In the case of the ongoing Bruce Power Life Extension Program and Major Component Replacement Project, the opportunity has been taken to add more cobalt-59 adjusters to increase cobalt-60 production above the existing levels. This investment will secure the operation of these reactors and cobalt-60 production until 2064.
At the OPG Darlington refurbishment, the opportunity will also be taken to convert these four reactors to enable cobalt-60 production. This will add valuable cobalt-60 supply and builds on OPG’s experience of cobalt-60 production at Pickering.
The Pickering reactors have been scheduled to cease commercial operation at the end of 2024, however, the Ontario Government recently confirmed its support of OPG’s plan to refurbish the Pickering B reactors that are also cobalt-60 producing units. This refurbishment is subject to approval by the Canadian Nuclear Safety Commission (CNSC) that is already considering a request from OPG to extend the operating licence of the Pickering B reactors until 2026. If approved, the reactors will continue operation until shut down to begin the refurbishment programme. Refurbishment would enable continued operation of these reactors for a further 30 years.
The CANDU reactor at Embalse, Argentina, has also been refurbished recently to enable continued operation and cobalt-60 production for a further 30 years. Additionally, Russian cobalt-60 production has been expanded. While two of the cobalt-60 producing units at the Leningrad Nuclear Power Plant have been shut down, five reactors at Kursk and Smolensk have been added. There is also a reported intension to increase cobalt-60 production at Indian PHWR reactors; and Nuclearelectrica Romania has announced a study of cobalt-60 production at its CANDU reactors at Cernavoda NPP.
Currently, almost all of the world’s cobalt-60 is produced in CANDU Pressurised Heavy Water Reactors (PHWRs) and RBMK Light Water Graphite-moderated Reactors (LWGRs) of which there is a limited number. The greatest opportunity to significantly increase the availability of cobalt-60 is therefore to develop production in new reactor types. There are approximately 440 commercial reactors in operation of which more than 300 are Pressurised Water Reactors (PWRs). This has made PWRs the reactor platform of focus for future cobalt-60 production.
In February 2020, Nordion announced that it was partnering with Westinghouse to develop large-scale production of cobalt-60 in PWRs. Both Nordion and Westinghouse have since updated the irradiation market with the timeline of this important initiative and confirmation that progress has been made with technology development, licencing, manufacture of components and the recruitment of three utility companies that operate five reactors. Production of cobalt-60 in PWR’s would be highly scalable with the capacity to at least double existing worldwide production volumes from PWRs in the US alone.
Other initiatives include the announcement in December 2021 that Framatome and Exelon Generation will cooperate to understand and develop solutions to produce cobalt-60 in PWRs operated by Exelon Generation (now Constellation).
Securing the critical supply of cobalt-60
The healthcare industry has relied on cobalt-60 since the 1960s when the demand for medical device sterilisation started to grow. The production of cobalt-60 in nuclear reactors remains critical to health care and will continue to be critical for the long term future. Although significant steps are underway to increase production, growing demand for healthcare means that new cobalt-60 supply will always be important.
The road to engaging in cobalt-60 production is complex. There are a number of design and engineering considerations, safety assessments, the need to understand the impact on reactor efficiency and operations, and many other regulatory and operational considerations. However, there is also a wealth of experience and willing partners who understand the importance of increasing cobalt-60 production. In addition to the provision of clean energy, the production of cobalt-60 in support of health care remains a highly positive contribution by the nuclear industry to societal wellbeing.
Author: Martin Comben, General Manager Gamma Irradiation, International Irradiation Association