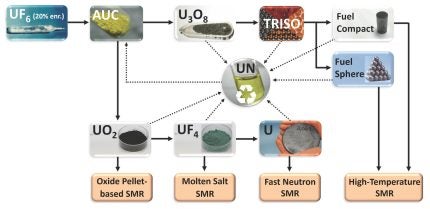
Most advanced or established reactor concepts can be designed as small modular reactors (SMRs). Considering fuels, the four main SMR designs are based on either ceramic oxide pellets, fuel dispersed in a molten salt, metallic uranium alloys or TRISO-coated uranium kernels. Enrichments in the HALEU range (5% – 20%) are beneficial for SMR fuels, because they have of a higher energy density enabling smaller reactor cores and generally allow for higher burnups. Consequently, refuelling cycles can be extended, and nuclear waste can be reduced in volume.
Starting from HALEU uranium hexafluoride (UF6), the preferred process is ammonium uranyl carbonate (AUC) deconversion to yield uranium dioxide (UO2) with beneficial physical and chemical properties. If the aim was to produce ceramic oxide SMR fuel, UO2 could now be pressed into pellets and sintered at high temperatures.
Furthermore, AUC can be directly calcined to yield triuranium octoxide (U3O8), which is the input material for high-temperature reactor (HTR) TRISO fuel element production. Several TRISO-coated particles are processed into fuel spheres or cylindrical compacts for all HTR-SMRs. A major advantage for TRISO fuel applications is the comparably low fluorine content resulting from the AUC process. UO2 originating from AUC deconversion can easily be fluorinated to uranium tetrafluoride (UF4) by hydrofluoric acid (HF). UF4 is the base material for liquid molten-salt SMR fuel cores. Finally, metallic uranium can be produced via calciothermic reduction of UF4. Uranium metal can be alloyed to fuel liquid metal-cooled SMRs like the sodium-cooled fast reactor (SFR).
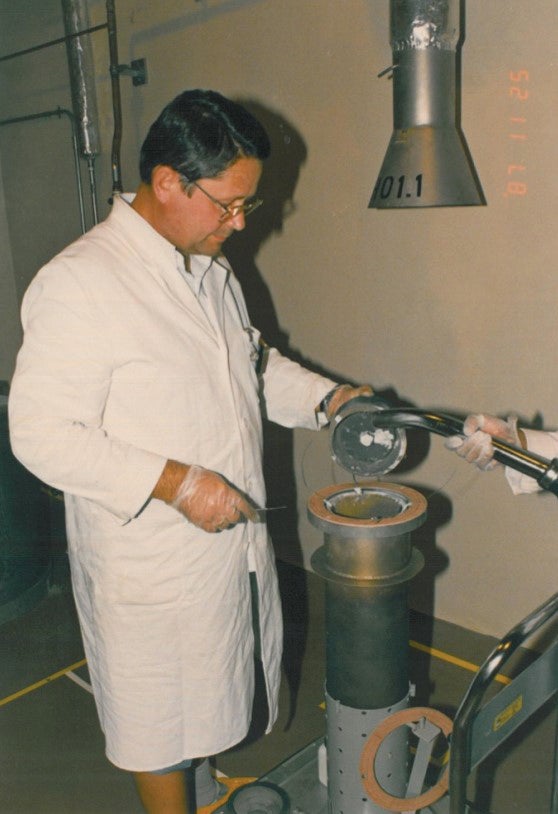
Overall then, it can be recognised that fuel for all common SMR types can be produced starting with uranium oxide gained from AUC deconversion.
The major SMR types and their fuel
Considering the four major SMR types based on their fuel in the context of current reactor designs the focus lies on the uranium-based fuels mentioned: UO2 pellets, molten UF4 salt, metallic uranium alloys and TRISO particles.
Ceramic uranium dioxide pellets are utilised as fuel in the form of classical cladded fuel rods for light water-cooled SMRs. Currently, the most widespread concept is the pressurized water reactor (PWR) but the boiling water reactor (BWR) also exists as an SMR, though it represents the less common technology. A pioneer in HALEU-fuelled pressurized water SMRs is Russia: An example is the RITM-200, which powers the Arktika icebreaker since 2019.
A land-based version of this SMR is known as RITM-200N and planned to be commissioned in Yakutia by 2028.
The next SMR type is the molten salt reactor (MSR). A crucial operational point lies in dispersing the fuel within the molten salt core. In this way, the core material itself
can also be used as coolant. UF4 is the compatible chemical form of uranium to be applied in this case. MSRs can be realised with a thermal as well as a fast neutron spectrum. The Danish developer Seaborg is designing a floating MSR with a capacity of 200 MWe per module. Their compact molten salt reactor (CMSR) has a thermal neutron spectrum and requires a moderator. The original design was based
on HALEU and a sodium hydroxide moderator. To mitigate the timeline risk because of an insufficient HALEU supply, Seaborg changed their current design to more readily available low-enriched uranium (LEU) and accordingly changed the moderating material from sodium hydroxide to graphite. This example again stresses the need for a reliable HALEU supply chain. Seaborg is still willing to apply HALEU for future CMSR designs.
Fuel based on metallic uranium (and various alloys) is used for a subset of fast neutron SMRs. The most common reactor concept is the liquid metal-cooled fast reactor (LMFR). To maintain a fast neutron spectrum, the moderator has to be removed from the reactor design; therefore, water cooling is not an adequate option anymore. Using liquid metal as a coolant also allows higher operating temperatures and thus a higher thermal conversion efficiency. Compared to oxide fuel, metallic fuel has a better heat conductivity and a lower heat capacity. For example, the ARC-100 reactor, which is planned to be built in Canada, is fuelled by 13% enriched Uranium-Zirconium alloy. This sodium-cooled fast reactor (SFR) is based on the EBR-II (Experimental Breeder Reactor), which was operated for more than 30 years at the Argonne National Laboratory in the USA.
The high-temperature gas-cooled reactor (HTGR) is the established design in the fourth SMR category. All high-temperature reactors (HTRs) utilise tristructural-isotropic (TRISO) particle fuel. TRISO particles usually consist of uranium dioxide (UO2) or uranium oxycarbide (UCO) fuel kernels, which are coated by chemical vapour deposition to produce TRISO-coated particles covered with four successive carbon and SiC-based layers. It is this durable and tightly specified fuel that largely guarantees the particularly high safety standard of HTRs. Near the end of 2023, China’s HTR-PM entered commercial operation and is therefore the first commercial high-temperature SMR. It is fuelled by 8.5% enriched spherical fuel elements (pebbles) containing about 12,000 TRISO particles each.
It is worth noting that besides gas-cooled HTRs, there are also salt-cooled HTRs like the fluoride salt-cooled high-temperature reactor (FHR), for example the KP-FHR (140 MWe) promoted by Kairos Power based in California in the USA. Although it is salt-cooled, it has a typical solid HTR core and operates on TRISO fuel. Thus, it should not be confused with a MSR, where the core itself is in a liquid state.
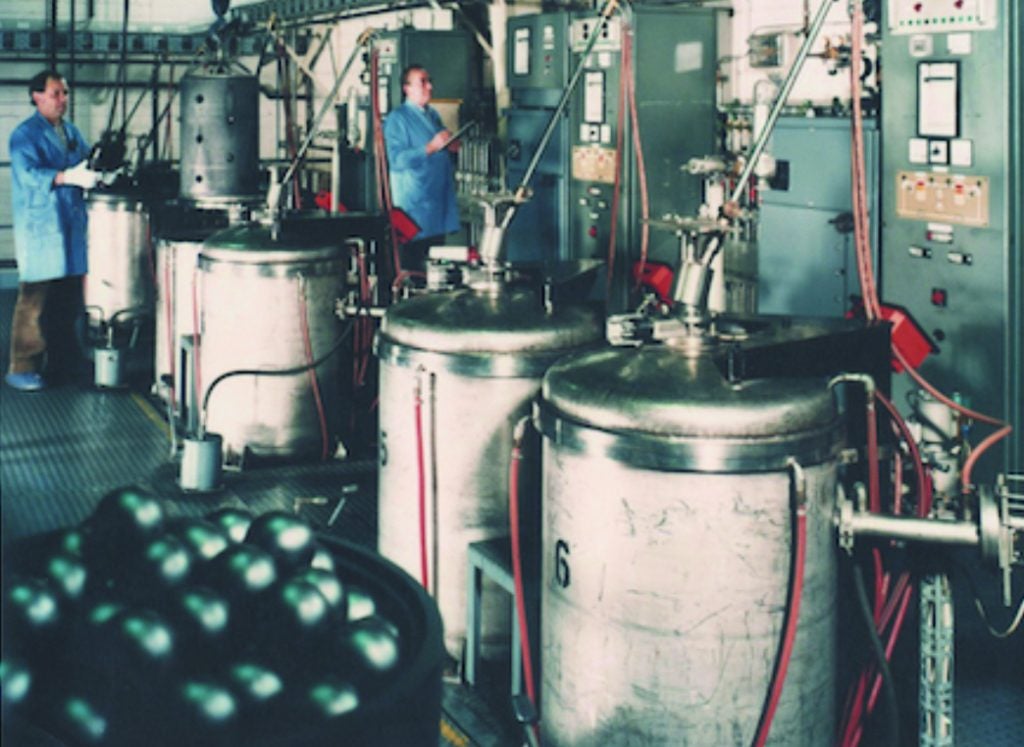
Using experience as a fuel plant operator and designer
NUKEM developed TRISO spherical fuel elements in the 1960s which found their way to China and the HTR-PM. In the 1970s and 1980s, a TRISO fuel production plant was operated in Hanau, Germany and as part of a later cooperation agreement parts of the original fuel fabrication plant were shipped to Beijing, China, in 1995 and rebuilt at Tsinghua University. The laboratory production line at the Institute of Nuclear and New Energy Technology (INET) went into operation in 1998. Based on the experience gained from the INET plant, CNNC designed the fuel production plant of the HTR-PM.
In addition to HTR TRISO fuel, uranium metal-based fuel covers the remaining three SMR fuel types. The process for producing uranium metal-based fuels begins with AUC deconversion to UO2 and continues through UF4 to metallic uranium. Since 1956, NUKEM has fabricated fuel assemblies from metallic uranium for the research reactor FR2 at Karlsruhe, Germany and the ECO reactor at Ispra, Italy. A superior AUC process, which has been well established for the mass production of UO2 for standard light-water reactor (LWR) fuel, was first introduced in 1978 at a new pilot plant. An industrial uranium metal AUC plant was designed and installed for BATAN, the national nuclear energy agency of Indonesia, and has supplied 20% enriched fuel elements for a Siemens material test reactor.
A certain amount of uranium-bearing scrap – off-specification material and the like – is normally generated at all stages of fuel element fabrication. Production processes should include the recycling of all of the uranium via dissolving, extractive purification and feeding the resulting uranyl nitrate (UN) solution back into the AUC process. This is done using the same equipment and ensures that no uranium is lost in the process.
Design of industrial-scale fuel production plants with throughputs of several tonnes of uranium per year for all common uranium-based SMR fuel types is possible. The prerequisite of a criticality-safe process keeping state-of-the-art radioprotection standards is available for HALEU material up to 20% enrichment.
Authors: Dr. Marina Sokcic-Kostic (Principal Engineer), Christopher Reiser (Physicist), Karl Froschauer (Deputy Director Business Development), Dr. Georg Brähler (Technology Advisor) NUKEM Technologies Engineering Services GmbH, Karlstein am Main, Germany