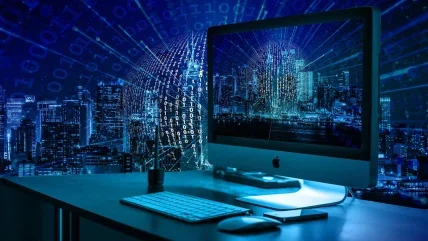
For many parts of the nuclear energy industry, vast expanses of land are dotted with critical data points, each requiring meticulous monitoring. Traditionally, this meant laying kilometres of cables. The sheer scale of the endeavour makes it unfeasible in many scenarios. But in highly regulated industries laying cables for data monitoring applications is not always even possible because of strict regulations and the extensive planning permissions required, as well as cabling costs. Disruption caused by the associated installation and maintenance work can also become prohibitive. Here, wireless communication systems can help facility managers retrieve and manage critical data from the field wirelessly, safely and efficiently and wireless telemetry systems are becoming increasingly important for plant-wide monitoring and control applications.
There are two fundamental types of wireless networks. The first is a classic master-slave system, typically used when communicating with a top-end system like a SCADA system. The simplicity of these systems makes them easy to manage over a network as there are no signal clashes between devices.
Alternatively, multi-point wireless systems operate in a peer-to-peer manner and report by exception. Multi-point systems like this are common in applications where there are multiple devices communicating over a large area, instead of reporting to a central point like a SCADA. For example, a system featuring multiple pumps and valves with devices dispersed across a site that must communicate with each other.
In these systems, it is possible that multiple nodes will try to communicate with each other simultaneously and cause a signal collision that results in neither signal reaching their destination. The only way the node knows its signal didn’t reach its destination is if it doesn’t get the short acknowledgement message back from the other end.
Managing multi-point wireless traffic
To minimise clashes, these multi-point systems should use carrier sense multiple access (CSMA) protocols that allow all the nodes on the network to listen to the traffic and wait for a gap to send a signal. However, even with CSMA in operation, it is possible that multiple nodes may try to send a signal in the same gap in traffic and create a clash. In these cases, the system should then implement a backoff and retry mechanism.
In this case, retry timings should be randomised as fixed timings are more likely to cause subsequent clashes. Furthermore, it best to set a retry limit of between three and five attempts as any more attempts than that are just needlessly blocking up the network while draining the nodes’ power supply.
Another way of minimising potential clashes is by ensuring there is not an excessive number of nodes on a network. Evidently, the more nodes, the more likely it is that signal clashes will occur. Although site-specific considerations determine the optimal number of nodes for a given network, as a general rule it is best not to exceed a dozen nodes to help keep traffic manageable.
For example, Omniflex wireless telemetry systems are optimised to ensure reliable data traffic so any disruptions are minimised with wireless protocols that contain an inbuilt digi-peating feature, which solves the issue of having two devices wanting to communicate with one another when they cannot communicate directly because of lack of line of sight. For example, node A wants to send a signal to node B where they both have network addresses but are either too far apart or out of line of sight. Adding a node C at a high point between them allow the signal to be relayed. With the digi-peating address included as part of the protocol, node C automatically relays the signal it receives.
Moving to wireless
This technology has found practical application through a partnership with Sellafield Ltd. which led to the design and manufacture of a suitable wireless interface to all its RPI manufacturers’ monitors, the W3 Wireless Interface Node. The W3 is a plug-and-play system that was commissioned for use at the Sellafield nuclear site to meet the demands of the industry. It offers a number of advantages over traditional monitoring systems, all of which lead to greater on-site safety and significant cost savings.
For instance, it has a universal interface and can be set up in minutes, eliminating thousands of hours spent installing and testing systems in active areas on-site. The system also drastically reduces personal radiation dose-rates that operators are exposed to because they can now monitor radiation levels remotely. There is also no need for additional third-party verification because it is a standardised product, made to ISO 9001 standards. Wireless interfacing has already begun reshaping monitoring systems for the nuclear industry, prioritising safety and efficiency.
Author: Ian McNeilage, Engineering Manager at Omniflex