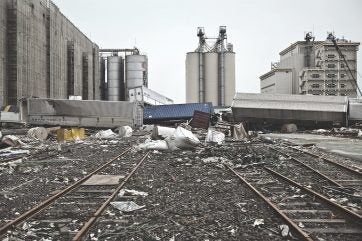
The protection of nuclear power plants against the effects of tsunamis and severe flooding is of critical safety importance, particularly in view of the potentially catastrophic effects of such events. A sensible strategy to increase the safety of nuclear power plants is the diversification of protection devices. By combining different protective measures potential vulnerabilities of individual systems can be minimised and the overall safety of the power plant can be increased.
In some cases, this approach is already being implemented by reinforcing or supplementing existing structural measures, for example by building higher or more robust flood protection walls designed to withstand extreme flood waves. Another option is the installation of special flood protection doors or barriers at critical locations within the power plant site. In addition, advanced monitoring and early warning systems could be implemented to respond to potential threats in time or to take appropriate measures in advance.
Alternatively, additional protective devices may be installed that act independently of the existing flood protection walls. These additional protective devices could serve as a supplementary safety measure and improve the overall resistance of the nuclear power plant to the effects of tsunamis and severe flooding.
Flood risk for nuclear
The threat to nuclear power plants from the effects flooding is a highly relevant issue. There are currently 74 reactors at 23 nuclear power plant sites worldwide that could potentially be affected by tsunamis and this trend is rising as the construction of new reactors gathers pace in various parts of the world. Beyond tsunamis, the effects of climate change must also be taken into account, particularly with regard to flooding and storm surge events. Rising sea levels and the increase in extreme weather events increases the risk of flooding which could also potentially endanger nuclear power plants. In addition, global political instability leads to further potential threats that must not be ignored, for example deliberate embankment failures that could trigger flooding of coastal areas and nuclear power plants.
Given the consequences, as illustrated by the 2011 Fukushima disaster, the devastating effects that tsunamis can have on nuclear power plants represents a turning point in the debate about flood safety. Although the Fukushima Daiichi nuclear power plant already had a flood wall of 4 metres in height, this was raised to 5.7 metres after the Indian Ocean tsunami in 2003. While this is a clear response to the lessons learned from this earlier event the enormous wave heights of the tsunami of 11 March, 2011, saw even this increased protective wall proven to be insufficient. The tsunami wave on this occasion reached a peak height of 14 metres and as high as 10 metres at the site of the nuclear power plant with devastating effects. The external power supply was destroyed and the critical infrastructure of the nuclear power plant, such as the emergency diesels, emergency standby and transformer buildings, were flooded. The subsequent collapse of the internal battery supply meant that the cooling water pumps for the reactors could no longer be supplied with power – a decisive factor in the nuclear disaster that followed.
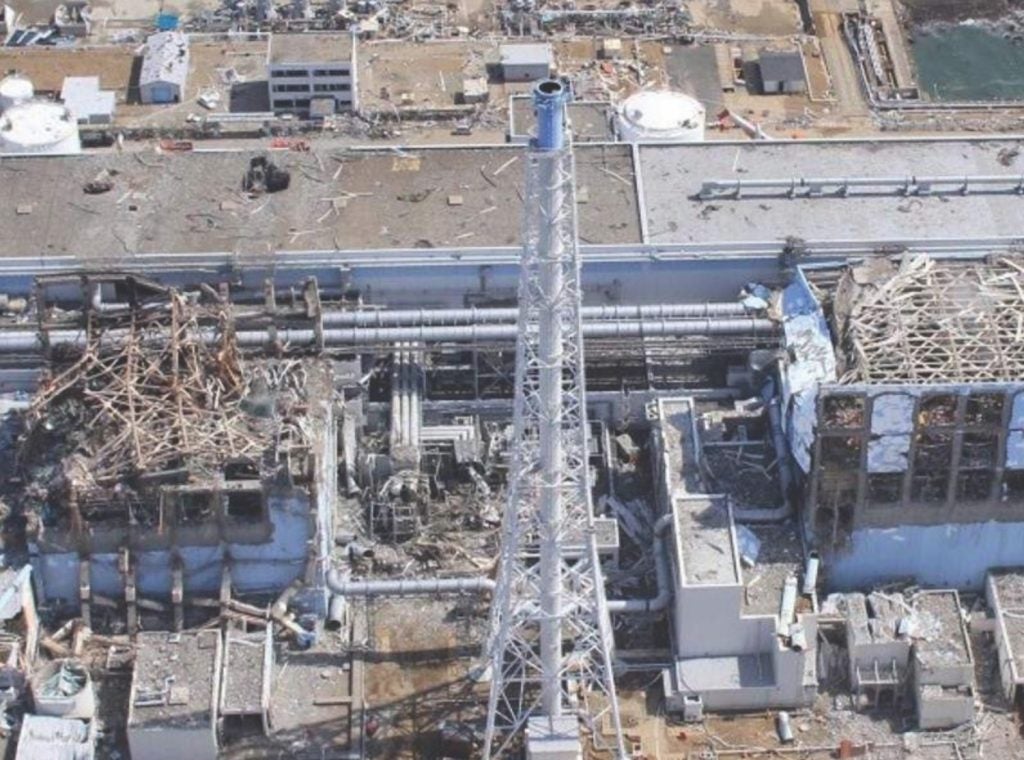
These events revealed the weaknesses of existing safety precautions against the effects of tsunamis and flooding and underlined the urgency of developing more robust and reliable protection systems. It has become clear that the construction of flood walls alone is not sufficient to cope with the potential risks for nuclear power plants.
A solution-focused approach
A multidisciplinary approach and, in the best case, a complementary passive system is needed to increase the safety of these plants and thus prevent similar disasters in the future. For this purpose, it is urgently necessary to identify building openings within a nuclear power plant that are important for safety and to protect them from flooding, regardless of their height. In an emergency diesel building, which is critical infrastructure, for example, this includes the combustion air intake, the diesel exhaust system, the fresh air intake and the exhaust air openings. Furthermore, an important goal in the development of an appropriate flood protection system is to achieve diversity compared to the existing flood protection walls and ensuring functionality of the system independent of the height of the tsunami.
A key aspect is the passive operation of the system, both when closing and opening with the system’s independence from an external power supply ensuring a high level of reliability, as it continues to function even in the event of power failures or technical problems. Control of single fault criteria and a multi-redundant design are further important features to consider in the design of a flood protection system. This ensures that the functionality of the system is maintained even if individual components fail. An additional application of the system is the prevention of internal flooding from room to room. This can also prevent possible contamination carry-over. In addition, strict requirements are to be set with regard to earthquake safety in accordance with specific nuclear regulations, such as KTA 2201.4 or KTA 3211.2.
The system to be developed should also be able to withstand various environmental conditions, such as flotsam, muddy water, high and extreme outside temperatures and high exhaust gas temperatures.
In order to maximise protection against potential debris and other external influences, an associated debris protection system should be developed in addition to the flood protection system. One of the most important functions of debris protection is to protect against floating loads, such as debris like gas/fuel tanks or trees.
In addition, debris protection should be designed to minimise the impact of blast pressure waves. For this purpose, reinforced concrete structures are typically used to reduce the effects of pressure waves and protect the various system components. It is also conceivable to extend the structure with explosion pressure flaps. Furthermore, the debris protection should potentially be designed to withstand extreme weather conditions such as severe winds, ice loads and abnormally high outside temperatures.
In addition, an earthquake decoupling system should integrated into the debris protection system to protect the systems from the effects of an earthquake and minimise any potential damage. The debris protection should be anchored using anchor plates and/or in conjunction with the existing building reinforcement to ensure stability. Further plant-specific protective measures can be implemented in the debris protection system to protect nuclear facilities from additional threats. These measures could include additional protection against debris from an aircraft crash, where the design aims to minimise the impact of such an event.
Further precautions can be taken to protect nuclear facilities from damage caused by tornadoes and/or tornado-induced loads. And, depending on the requirements, debris protection can be further developed to defend against terrorist attacks by reinforcing the structures and implementing object protection grids, for example.
The TsunamiFloodProtection system
Based on these core criteria, INNOMECOM AG has developed its TsunamiFloodProtection (TFP) system using a specified qualification plan to ensure its effectiveness and reliability.
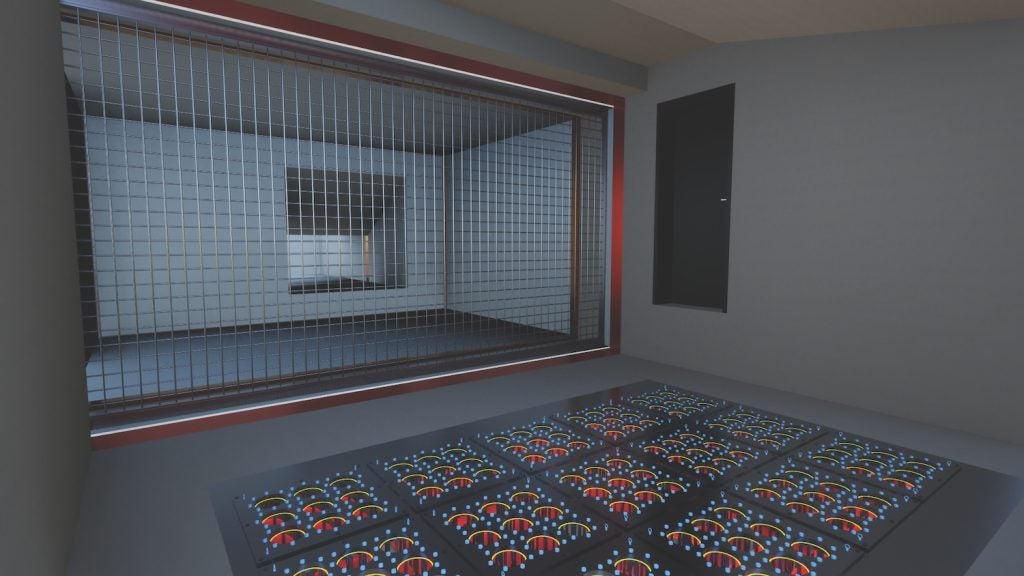
In order to meet high nuclear safety standards, the closing function of the TFP system was reduced to the essentials. Double floating systems were designed according to specified buoyancy, which run in guide rods and close a constructed base plate tightly in the event of a tsunami or flood. This system is bolted into a specially developed modular mounting frame for maximum flexibility and integrated into the debris protection system.
Carried out in accordance with nuclear-specific quality standards such as KTA 1401 and IAEA 50-C-Q, this comprehensive approach illustrates the need and the ambition with which the TFP system was developed to provide the highest safety standards for nuclear power plants. For example, as part of the design process the TFP system parameters were calculated in accordance with the earthquake verifications of the KTA regulations in order to prove its effectiveness under seismic conditions. To achieve effective earthquake decoupling, special spring damping elements were installed that meet the nuclear requirements. These elements play a crucial role in absorbing vibrations and help to maintain the structural integrity of the system during seismic events.
This TFP system can be installed in conjunction with the debris guard in both the intake and exhaust air path of a ventilation system. The debris protection is divided into a lower and upper section, with the lower section connected to the ground and the upper section connected to the building. In addition to keeping debris out, the debris shield is designed to break tsunami waves and severe flooding and direct water to the TFP system. This function is critical to protecting the system from the effects of extreme hydrodynamic forces.
Thanks to its design, the TFP system is a passive system and fully redundant. It can also withstand large masses of mud and floating debris, extreme weather conditions, as well as high earthquake loads. This approach fulfils all of the previously defined requirements and the system therefore also falls into the desired IAEA Passive Category C. The selection of appropriate space conditions for the
installation of the TFP system and the associated protection devices is of great importance. Taking the spatial requirements into account ensures that the installation and periodic inspections of the TFP system can be carried out properly.
Part of the development of the TFP system was the iterative approach to creating the finite element model (FEM) in order to simulate the high earthquake loads. An overload (elastic deformation) was deliberately provoked in the first prototypes in order to determine the material and design limits while an additional calculation in accordance with ASME guidelines is also currently being implemented. TÜV SÜD IS GmbH was further consulted to determine the pressure loss for a TFP module and the ZETA value of the component using a specially designed pressure loss test
rig. The determined pressure losses are necessary for the overall design of the system in which the TFP system is to be integrated in order to generate as little additional pressure losses as possible, especially in an existing system.
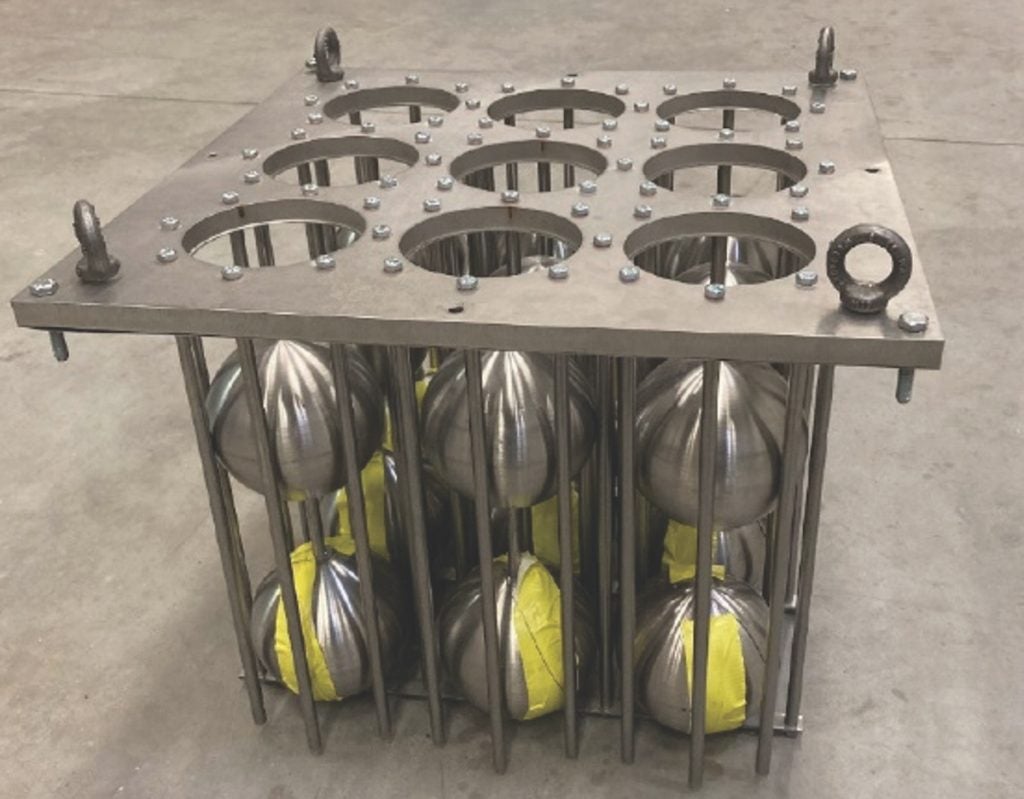
In addition, a specially specified tsunami test stand from INNOMECOM AG enables individual TFP modules to be subjected to specific mud and water masses. Tsunami and/ or flood characteristics, such as high water velocities and various forms of sludge, can be tested on each TFP module on this test stand. It is also possible to take into account the individual sludge compositions of the existing coastal and soil structures adjacent to a nuclear power plant. The proof of function on the tsunami test stand for the TFP system was independently verified by TÜV SÜD IS GmbH under specified tsunami conditions. The result is a patent-pending TFP system which can make an additional contribution to safety and to protecting nuclear facilities in the event of tsunamis and flooding with its robust design, passive and self-sufficient function, extensive testing and independent verification However, it is important to emphasise that no single protective measure or strategy can completely eliminate all risks. A comprehensive approach to safety, based on a combination of different protection devices and measures, is therefore crucial.
Author: Jens Wieneke, Head of Engineering, INNOMECOM AG