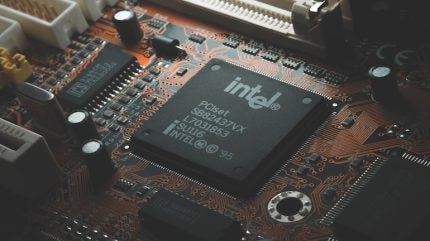
In many countries, investment in nuclear power has waned significantly over recent decades. Now, as the previous generation of engineers ages into retirement, there are too few new engineers to take over. The rise of the new nuclear industry has only further compounded the skills shortage and resulting knowledge management challenges. Simulation can play a major role in upskilling new engineers entering the field and recording the knowledge accumulated by the previous generation. Simulation can not only to help bring new reactor concepts to pre-commissioning efficiently, but also facilitate cross-functional teamwork, communication, and the transfer of skills.
From design to commissioning – a multi-step process
When a new nuclear reactor concept is first developed, it is generally limited to a preliminary design illustrated using a software-based demonstrator that runs physical equations. Moving from this early incarnation of a new reactor to a detailed design that is ready for test commissioning is a multi-step process involving several teams. At this stage, the number of elementary systems is limited, but it will increase to up to more than 200 by the time the detailed design is ready for test commissioning. The right simulation software can help with the technical and organisational aspects of these complex projects by delivering an appropriate environment for engineering activities and the development of elementary systems at each step in the project lifecycle. Ideally, a single environment, such as CORYS ALICES Plus platform, should be able to cover all activities, from instrumentation and control (I&C) to the human-machine interfaces (HMIs), physical process models, and, finally, the operating rules and instructions.

- Instrumentation and control: First, the I&C specifications should be drawn up and implemented in the simulator. An I&C emulator or equivalent I&C software is then fed into the simulator. Preparation of commissioning and tests is the final step in the process.
- Human-machine interfaces: A simulator should cover initial concepts, operator station specifications, human factor studies, and full replica operator stations for operator training.
- Physical process models: Real-world equipment data sheets should be integrated starting at the standard equipment design stage. The simulator should then be connected to the project database to enable automatic updates.
- Operating rules and instructions: Initial validation should be completed at the basic design stage, with rules for normal and abnormal operation.
Nuclear reactors are complex systems of systems involving many different subsystems and activities. It is important to rapidly move new concepts onto a scalable integration platform that can effectively orchestrate the multitude of components involved, including integrating component-specific software (such as for I&C systems) and modelling solutions (either through open standards for exchanging simulation models in a standardised format like FMI, OPC or other standards or through custom integrations). A single simulation environment that can scale from thousands of variables to millions is also essential.
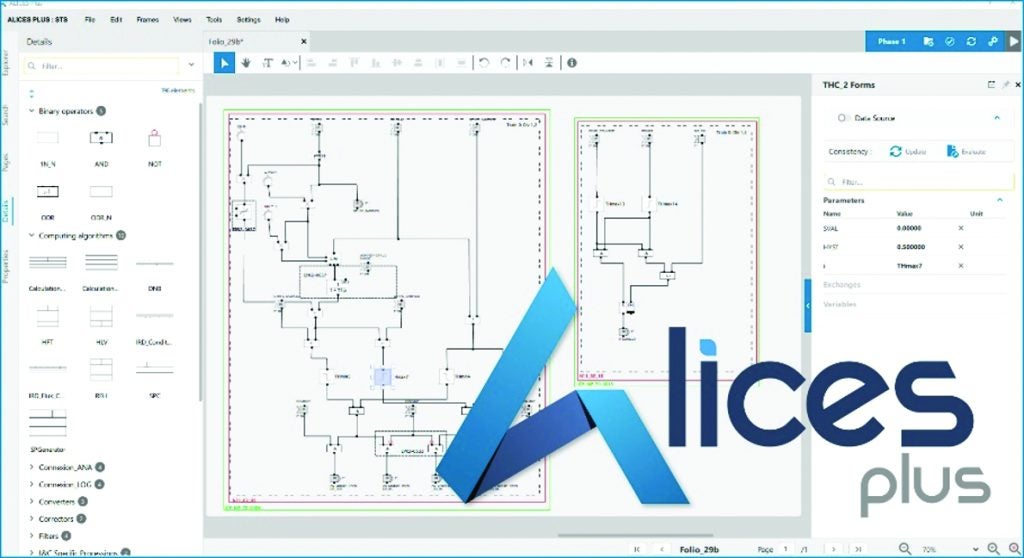
From preliminary studies to basic design
Preliminary studies focus on basic concepts: A first loop is designed with target performance values and the associated modelling. At this stage, a simulator should be able to easily run physical equations to evaluate the inlet and outlet reactor temperatures, mass flow, exchanger design and geometry, and the primary loop pumping system. It should also be possible to run the first transient scenarios on several different modelling tools and compare the results. Based on the findings of these preliminary studies, the basic design can be completed. The main objective at this stage is to integrate the basic design to ensure consistency across the entire system before beginning the detailed design. Here, a simulator should be able to provide the best estimate of behaviour of all second-level systems.
When it comes to simulation data, traceability is vital. At any time during the development process, it should be possible to explain the origin of any data used in the simulator, which should be connected to a specific database containing the engineering data values used for simulation. This ‘data package’ must be validated with the simulation team. In organisational terms, this means that the basic design simulation can only begin once the engineering and simulation teams have given the green light to proceed. In other words, when both teams agree that the data is of sufficient quality. This means:
- Determining what alternative data will be used if any data is missing
- Data type and format so that the data package can be imported automatically
- How missing boundary conditions and initial state data will be handled
- Having sufficient hydraulic line data for functional validations, which means having a PID controller with sensors (PID V2) and consistent I&C lines and specifications
Once the basic design simulation project is ready to begin, preliminary transient scenarios are run for functional validation. At this stage, simulation is essentially based on one dataset. Again, organisationally, good communication is crucial. Equipment datasheets can be upgraded in the simulation if the engineering and simulation teams come to a consensus, bearing in mind that at this stage, the purpose of the basic design simulation remains the testing of major transient scenarios to validate the general architecture before entering the detailed design phase.
Data readiness is one of the main challenges during detailed design. The ability of a simulator to handle multiple data packages while ensuring traceability and calculating impacts on validation scenarios is crucial. Ideally, a simulation provider should provide not only tools, but also methods and support with:
- Data management
- Simulator updates
- Test automation
- Regression tests
- Data traceability
Additionally, the tools delivering these capabilities should be able to interface with product lifecycle management tools to enable interactions with engineering.
Engineering creating new requirements
Once the engineering phase starts, deliveries will be expected around every three months, which means that every three months the elementary systems must be updated in the simulator. This requires a dataset or batch that must be defined. Generally, each batch delivery will come with its own acceptance tests. These tests – and their results – will form the basis of the reactor’s future operating procedures. In addition to the data requirements, this phase raises new organisational challenges. Engineering and simulation will have to work seamlessly together for the project to succeed. An engineering simulator project manager should be assigned to liaise with all project stakeholders to create a data package delivery schedule. A simulator representative on the engineering team should be assigned the tasks of promoting the simulator and training users within the engineering team.
For example, the I&C engineer can use the simulator to update the I&C specifications using the I&C CAD tool and then load the new I&C system into the simulator so that the new sequence can be tested interacting with all other systems and thermohydraulic lines. Several platforms running the engineering simulator can be made available to the engineering team and automatically updated. The required hardware configuration is common; it takes just a few computers with Intel core i9 chips. In terms of skills, testing the I&C sequence is similar to running a debugger. A fix in the I&C diagram is straightforward and the user can simply reload the ongoing sequence after a change by using the snapshot management system in place with the simulation platform.
With the revival of nuclear power at the center of the transition to low-carbon energy, simulation will play a critical role in advancing new reactor concepts. And, with the shortage of experienced engineers and the increasing complexity of reactor systems, simulation will help bridge the skills gap while supporting every stage of new nuclear concept development, from preliminary design through to commissioning.