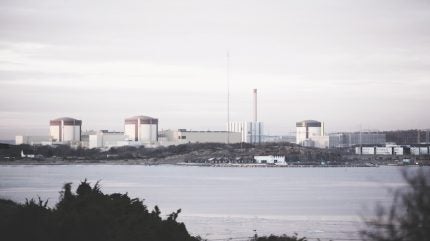
With nuclear power plant owners worldwide looking at extending the service life of their assets to 60, 80 years or even longer it’s clear that while the reactor itself is unlikely to change, key balance of plant components will need to be upgraded or replaced. One of the most important balance of plant elements is the steam generator and by uprating the design, important economic and performance opportunities potentially emerge. Steam generators have a typical service life of between 40 and 50 years, meaning their replacement is all but guaranteed during the extended lifetimes that are being commonly mooted today. However, since many of today’s operating large light water reactors were designed and built in the 1970s and 1980s, steam generator design and the materials used have seen a number of significant advances. Taking advantage of these breakthroughs, Framatome developed its axial economiser steam generator. With its improved thermal efficiency, this design can significantly increase the outlet steam pressure and thus boost electrical power produced by a nuclear reactor. Framatome states it can achieve these gains while also preserving the operating flexibility of the plant.
Charles Merlin, who leads Framatome’s NSSS large components business development in North America, explains to NEi that the origins of the new steam generator lie in the French N4 reactor: “It’s based on the steam generator design for the N4 reactor,” he says, noting that applying experience from these reactors commissioned in the early 2000s the design has now evolved to become a standard feature on the French 1650 MW EPR design being built, for example, in the UK at Hinkley Point and elsewhere. “We came up with this design for the N4 originally as an improved steam generator. Afterwards it was deployed on the EPR platform as the only way to get such a high power rating on the four loop design without introducing a very large steam generator, like Combustion Engineering has been doing. Axial economiser steam generators are now installed in all our EPRs,” says Merlin.
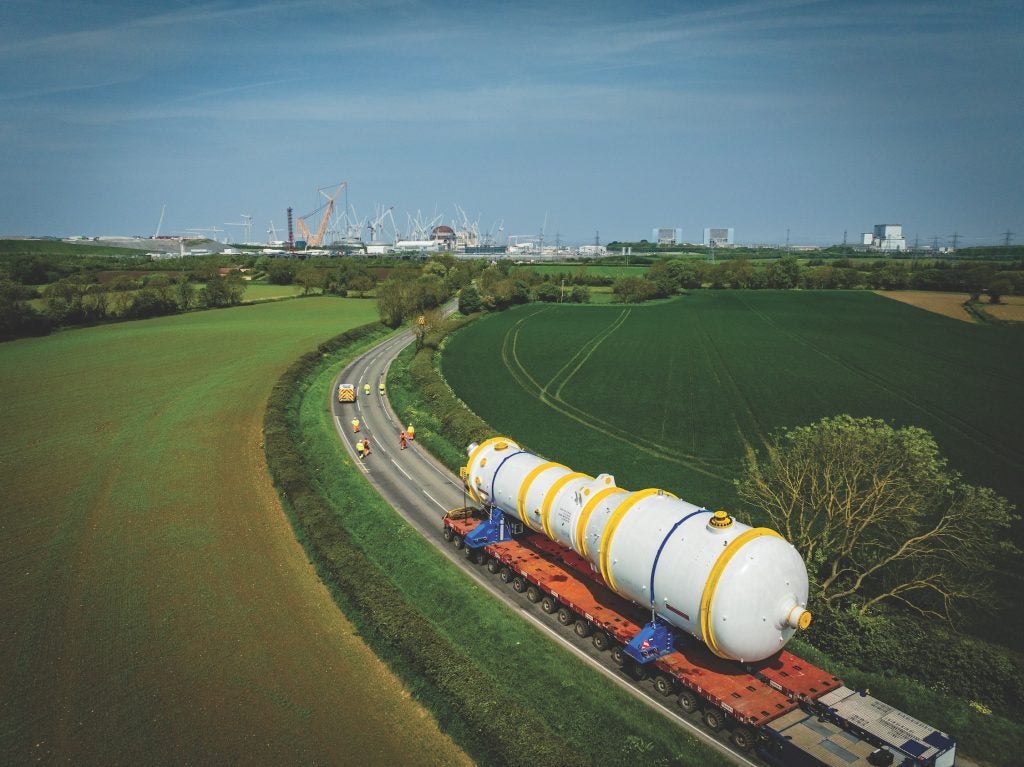
One the key technical developments in the axial economiser is the design of a recirculation system which enables feedwater preheating. “There is a double wrapper around the steam generator shells, around the tubes in the bottom part. There is a second cylindrical part so we can inject cold water from the recirculation on the cold leg at the bottom of the steam generator where the tube starts. The effect is mainly to increase the thermal transfer by getting a much bigger temperature difference between the water in the tube and the water around it from the secondary loop. The recirculation is on the secondary side and the feed water is transformed into steam in the recirculation with pre-heating,” says Merlin. And, while he acknowledges that the idea to have an economiser and steam generator is not new, the Framatome design has a crucial difference with earlier attempts. “There was an attempt, for example, by others, where there was a horizontal pre-heater, but due to the fact that it was horizontal it generated water hammer.”
In contrast, Framatome’s economiser sends the recirculated water in a vertical plane parallel to the steam tubes. This allows pre-heating without getting any water hammer or vibration in the pipes.
Merlin explains the key challenge of water hammer and the benefits of designing it out of the steam generator: “It’s very important because you have always a thermal stratification and water hammer decreases the life expectancy of the steam generator tubes. There is no cross flow, so no potential tube vibration and also increased water level stability in the steam generator. This economiser contributes to an increased lifespan over a normal steam generator because there is no water hammer”.
He also highlights several additional benefits of the design: “There is a dedicated auxiliary feed water system to improve the pressure shell design. It also increases operating flexibility because there is a bigger separation of steam and water.”
Merlin also argues that the design helps to minimise maintenance costs too: “It also facilitates better sludge management and has a higher permeability of the tube support plate to reduce the clogging risk and a foreign object catcher is included by default on this type of design,” he says.
Summarising the benefits of the new design he notes: “In the end you get an increase in outlet pressure and power for a given heat exchange surface so you can get less tubes for the same power and thus a more compact design or get a potential upgrade by keeping the same number of tubes and the same surface, but much higher surface heat exchange.”
Merlin continues: “The first effect is to increase the thermal transfer in the steam generator but also you get more cooling capacity and because it creates increased margins for safety analysis it is possible to increase the core power. In the event of an accident and even during normal functioning given this there is a higher margin to increase power from the core, so the fact that you have this double effect gives you the possibility to have this larger power capacity.” To realise this opportunity in an existing facility some additional requirements and upgrades are needed to other elements of the balance of plant. “To transform the operating electricity output you need turbine investment, but it’s definitely the cornerstone of any such very large improvements on the nuclear steam supply system,” says Merlin
The economiser also takes advantage of materials development that have taken place over the decades, as Merlin points out: “Beyond the economiser on this state-of-the-art steam generator architecture we use 690 stainless steel thermal treated tubing for the internals”.
Steam generator replacement at Ringhals 4
Although the enhanced economiser design has been installed in the four units at Chooz and Civaux as well as the EPRs at Taishan in China, Flamanville in France, Olkiluoto 3 in Finland, and at Hinkley Point C in the UK, this design has also been deployed as an upgrade at the Ringhals 4 plant in Sweden.
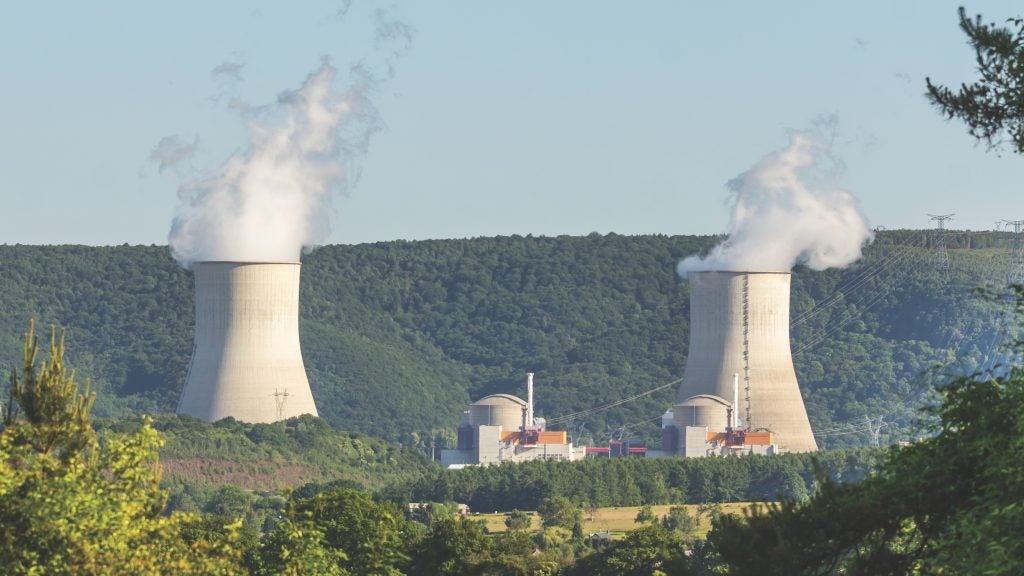
Ringhals, located some 60 km south of Göteborg on the Värö Peninsula, is host to three PWRs (units 2, 3 and 4) and one boiling water reactor (BWR). All units were constructed between 1969 and 1985. Ringhals is owned by Ringhals AB, which in turn is owned by Vattenfall (70.4%) and EOn (29.6%).
The Ringhals 4 unit started operations in 1982 and features a WH-3 loop steam system with W-D3 steam generators. In 2007 Ringhals AB applied to the regulator to increase the plant’s thermal output from 2783 MWth to 3300 MWth. A prerequisite for the uprate was the replacement of the unit’s three steam generators. These were replaced during the summer of 2011 as part of an uprating and life extension project.
In January 2007, following a series of studies carried out by Framatome – at the time AREVA – the nuclear technology company was awarded a contract for life extension of the unit and a simultaneous uprate in capacity with the replacement of the three steam generators and the pressuriser. In another project in 2007 replacement of the low-pressure steam turbines led to a 40 MWe power increase.
Nuclear power plants typically replace steam generators periodically and it is a process that is also often considered when existing plants are modernised as part of a life extension programme. Merlin, explaining the overall strategy behind the design, says: “In the original Westinghouse philosophy the steam generators are smaller. To keep everything in the containment building without having a very large steam generator and four loops we had to find a solution to increase the thermal transfer”. Merlin notes the strategy behind the adoption of the new steam generator design: “Generally when you do steam generator replacements, you try to get a steam generator which has the same volumes as the previous one you are replacing.
Given that this is potentially a more compact solution it was considered an option for the Ringhals 4 upgrade because while there wasn’t available space to put in a bigger steam generator it was nonetheless possible to increase output from the reactor.”
“Ringhals 4 is a very classical Westinghouse three loop design, like North-Anna, Surry, Beaver Valley etc… This is the same design family. We did a steam generator design, which was the same volume as the original one but with this economiser which created a large margin compared to the original steam generator,” Merlin says.
The new steam generators, each of which weighs some 300 tonnes and is about 20 metres long, were transported by ship from the port of Videbergshamn on Sweden’s west coast to the Studsvik harbour at Nyköping on the country’s east coast ahead of their final journey to the plant. During the summer of 2011 refuelling and maintenance outage at the plant, the three new axial economizer steam generators and the new pressuriser and new high-pressure turbines were installed. Replacing the original steam generators with the axial economizer design led to an 18% increase in plant capacity. The new high-pressure turbines added a further
30 MWe, boosting the unit’s rated power output from 930 MW up to 1130 MW with the new steam generators adding a substantial proportion of the increase alone.
The capacity uptick was confirmed in early 2015, after testing and a safety audit, when the Swedish nuclear regulator, Sweden’s Radiation Safety Authority (Strålsäkerhetsmyndigheten, SSM) approved the 1130 MWe output, equivalent to adding 200 MWe. The replacement of the three steam generators was the largest single project in the unit’s modernisation and life extension programme.
In January 2012 the three old steam generators were transported to the Studsvik plant, where they were processed for recycling and disposal.
In the wake of the upgrade, in 2017 Ringhals decided to invest in further subsequent improvements with an independent core cooling system in units 3 and 4. With this investment, totalling around SEK 900 m (US$82 m), the plant will be able to supply electricity into the 2040s.
Future steam generator replacement market
Looking ahead, Merlin sees much more scope for uprating reactor power ratings by retrofitting axial economiser steam generators. “From all this family of reactors the one in Sweden is definitely by far the one with the highest power rating so this is the biggest opportunity, given those other design families also have opportunities to increase output by using this better steam generator design,” he says. Although acknowledging that the gains achieved may be less than that at Ringhals 4, Merlin is nonetheless clear that there are substantial benefits: “We couldn’t necessarily expect 18% everywhere, that would be unrealistic and will also depend on the balance of plant. Not all the reactors from this generation are really standardised too, even if the core could be the same sometimes the geometry is a bit different, so we’d need to study the opportunity on a case-by-case basis. But, in the general case it will create quite a large margin to operate, which is usually the thing you want to increase for operational and maintenance flexibility. This provides a future opportunity to uprate the steam turbines and other balance of plant equipment to get that extra leap in power depending on life expectancy,” he says.
Merlin also points to broader macro-economic trends that point to life extension and capacity increases across the global reactor fleet: “For reactors which have very old steam generator designs with alloy 600 tubing, replacing them, especially if they want to go to 80 or even 100 years of operation, is a no regret option because the steam generator would have to be replaced at some point in the lifetime of the plant because the tubes are from earlier alloys that are not as good so they’re being replaced everywhere,” he says.
In addition, “It goes well with the current paradigm, especially in the US where there is an incentive for major investment plans to maximise lifetime and production. Under the IRA, because the steam generator allows operational improvements, such upgrades are therefore eligible for funding,” he says.
There are also underlying drivers such as growth in the data centre sector and elsewhere that favour the continued operation of nuclear power plants beyond their original lifespan. “I would say the climate around this changed quite quickly. This is something we weren’t hearing before that much. There is a demand for increased power and our steam generator technology is definitely suitable for this so that potentially also bodes well for uprating and life extension,” Merlin concludes.