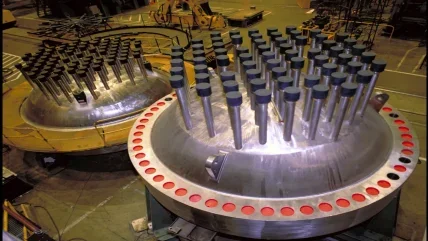
The AP1000® Reactor Coolant Pump (RCP) is designed in accordance with the requirements of the Westinghouse Electric Company’s new Advanced Passive Reactor Plant. The pump is designed, manufactured and tested by Curtiss-Wright Corporation at its Flow Control segment’s Electro-Mechanical Division (EMD) facility in Cheswick, Pennsylvania. The first use of the new design will be at the AP1000 plant currently under construction at Sanmen Nuclear Power Station, Sanmen County, Zhejiang Province in China.
The casing of the AP1000 reactor coolant pump is directly attached to the steam generator, and the pump motor with attached hydraulics is bolted and seal-welded to the casing to form a hermetically sealed assembly. The motor consists of an integrated stator and rotor assembly with attached hydraulics. Both the stator winding and the rotor squirrel cage are hermetically sealed to achieve a dry winding for the 60-year design life of the motor.
EMD has a strong history of designing and manufacturing reactor coolant pumps for the power industry. Technological advances have been made through design and analysis software, incorporating experience to improve the design and manufacture of the canned motor pumps. In particular, advances in computer capability coupled with the development of finite element analysis methods have provided design tools to permit a much more rigorous and refined design process.
EMD recently completed qualification tests of the AP1000 RCP, which met all specification requirements.
The Curtiss-Wright Corporation was founded in 1929, the result of a collaboration between companies formed by the Wright brothers and Glenn Curtiss, three of the early innovators in flight. The company brings the same innovative spirit and approach to new products and new businesses even today.
EMD’s technical legacy includes the development of the canned motor pumps used in the first commercial nuclear power plants in the US. Today EMD’s products, which include reactor coolant pumps, seals, motors and control rod drive mechanisms, are some of the highest-reliability pieces of equipment in a nuclear power plant. EMD has supported over 100 operating commercial nuclear reactors, including manufacturing over 350 reactor coolant pumps. It has now designed, manufactured and qualified the AP1000 reactor coolant pump, which will be used for Westinghouse’s generation of new plants worldwide. Currently, EMD is manufacturing reactor coolant pumps for AP1000 plants under construction in China and the US.
The AP1000 reactor coolant pumps are high-inertia, high-reliability, low-maintenance, hermetically-sealed canned motor pumps that circulate the reactor coolant through the reactor vessel, loop piping, and steam generators. The pumps are integrated into the steam generator channel head.
RCP in context
The AP1000 pressurized water reactor (PWR) system includes a primary coolant system and a secondary coolant system. The RCP provides fluid energy to circulate the primary fluid and is directly mounted to the steam generator ‘cold leg’ where the primary fluid exiting the steam generator is being returned to the reactor vessel. Installing the RCPs in the cold leg reduces the temperature of the primary fluid that is being pumped by the RCPs, which reduces the fluid temperature of the primary fluid that is allowed to circulate through the motor internals to lubricate the bearings and cool the motor.
The RCPs that circulate the primary fluid through the reactor system consist of hermetically-sealed integrated pump/motor units. The suction nozzle is welded to the steam generator channel head and discharge nozzle of the pump casings are welded directly to the primary coolant piping of the reactor system. The motor electrical hardware is sealed within thin non-magnetic metal ‘cans’ that keep the water being pumped from interfering with the electrical function of the motor. The motor housing is also bolted and welded to the pump casing and the pump impeller is installed directly on the end of the motor shaft, thus eliminating the need for seals on the pump shaft that would be prone to wear and leakage. Both the pump casing and the motor stator housing form a part of the primary coolant system pressure boundary. Refer to Figure 2 for a schematic of the AP1000 RCP.
The AP1000 RCP is a seal-less design that utilizes primary loop water as the bearing lubricant. The fundamental pump design has been proven by many years of service in commercial nuclear power (as noted above) and other applications. Since the AP1000 reactor coolant pump is attached directly to the steam generator, a significant amount of primary system piping and valves are eliminated, which enhances plant safety.
The AP1000 design uses four pumps. Two pumps are attached to each steam generator. Each AP1000 reactor coolant pump is a vertical, single-stage centrifugal pump designed to pump large volumes of primary coolant at high pressures and temperatures with a 60-year design basis. The motor power supply is from a variable-frequency drive, which permits variable-speed operation. Table 1 shows the design parameters associated with the final design of AP1000 RCP.
RCP reliability
As opposed to most common applications where a shaft coupling is utilized to drive the hydraulics, necessitating a dynamic seal, the canned motor and casing are integrated into a single unit that does not require a shaft seal. The pump impeller is mounted directly onto the motor shaft and the motor electrical hardware is sealed from the water by thin metallic ‘cans.’ The elimination of the pump shaft seals increases reliability and, with the AP1000 pump welded directly into the primary pressure boundary, mitigates concerns for leakage of the radioactive primary fluid from the reactor system. The primary fluid pressure boundary structure is incorporated into the motor stator assembly. The RCP is designed to operate continuously.
Achieving a long operating life for the motor requires reliable insulating materials and a cooling system that maintains the operating temperatures of the motor winding insulating materials below their rated temperature limits. The RCP hydrodynamic fluid film bearings have an inherently long operating life because a fluid film separates and lubricates the bearing operating surfaces, thus minimizing wear. The internal circulation flow circuit assures that the motor is adequately cooled and the bearings are properly lubricated. A dual heat removal system is achieved with a cooling jacket installed around the exterior of the motor housing, and a second higher-capacity externally-mounted heat exchanger with a secondary side component cooling water system. To adequately cool the motor and properly lubricate the bearings, the primary fluid in the motor region is maintained at a temperature that is much cooler than the primary fluid by use of a thermal barrier. The thermal barrier arrangement is employed between the pump casing and the motor to minimize the heat transfer between these fluids.
The AP1000 pump is designed with EMD’s strong design and analysis capabilities, which are based on more than 50 years of canned motor pump experience. Advancements in analytical software capabilities have been maintained and improved for all aspects of the design including thermal-hydraulics, structural, dynamics, and electrical design. Specific features targeted for design analysis utilize computerized fluid dynamics software for the hydraulic design, and internal circulation features to support the flywheel and thrust bearing designs. In addition, EMD has modeled defined regions of the motor electrical design and performed electromagnetic finite element analysis to optimize flux field performance.
The following is a brief description of the RCP subsystems that perform these critical functions. Figure 2 shows a typical arrangement of an RCP.
Pump hydraulics
The AP1000 RCP is classified as a mixed-flow centrifugal pump. The pump hardware includes a one-piece casing that encloses the fluid being pumped, a rotating bladed impeller and a stationary vane diffuser. The impeller design specific speed is consistent with EMD’s extensive experience and the impeller is attached directly to the motor shaft through the thermal barrier into the pump casing.
Motor
The motor is a four-pole squirrel induction motor and is used for canned motor pumps because there is no contact between the rotating and stationary electrical components. Care is exercised during the manufacture and in-process testing of the qualified insulation system to ensure reliability of the motor for achieving the operating design life.
The stator windings are hermetically sealed into the shell structure by a thin non-magnetic metal can that is installed on the inside diameter of the wound stator assembly and welded to the stator end closures. The rotating portion of the motor (rotor) is a single shaft with axially-oriented rotor bars and is also hermetically sealed inside a thin non-magnetic can. The annular region formed by the concentric stator and rotor cans contains internal circulation flow that cools the motor.
Power cables are connected to an external terminal arrangement through the external terminal box, which houses the hermetically-sealed and insulated terminal glands that penetrate the primary pressure boundary shell.
Bearings
The fluid-film hydrodynamic bearings have been technically advanced through EMD experience, such that in lieu of full-sleeve radial bearings, pivoted pad radial bearings are used to achieve rotor dynamic stability and improved reliability. Both the radial and thrust bearings are located in the motor portion of the RCP where the temperature of the fluid is maintained within a controlled temperature range. In hydrodynamic fluid film bearings, fluid pressure between the stationary and rotating members supports the bearing load, eliminating wear, which makes them well-suited for the AP1000 RCP, which is designed to operate for long periods of time without intervention.
The double-acting thrust bearing is located at the non-hydraulic stator cap end of the motor assembly. It is a self-aligning bearing with a single solid hard-faced thrust runner, operating on double-acting preloaded self-levelling thrust shoes which provide reliability improvement by achieving rotating component stability. Thrust loads are accommodated with the lower thrust bearing for start-up conditions, and are transferred to the upper thrust bearing for operating conditions.
Internal circulation
An important feature of the AP1000 RCP is the internal cooling. The motor is cooled to preserve the operating life of the insulation materials and maintain fluid viscosity for the bearings. The three RCP subsystems to achieve these important functions are the internal circulation system, the heat exchangers, and the thermal barrier.
Primary water circulates through the motor internals via an engineered circulation system to cool the bearings and remove motor heat, while a secondary heat exchanger system removes the motor generated heat.
To maintain acceptable temperatures in the motor cavity, a thermal barrier is installed between the motor cavity fluid and the much hotter water in the casing region. The thermal barrier limits the heat transferred from the pumped fluid in the casing, and also incorporates a close-running-clearance labyrinth seal that limits the interchange between the casing water and the bearing water.
Flywheel inertia
A critical innovation in the AP1000 RCP is the incorporation of two high-inertia flywheels, one at each end of the shaft located within the pressure boundary. These provide the necessary coast-down inertia to maintain sufficient fluid flow to the reactor in the case of a loss of power. The location of the upper flywheel is in the hottest region of the fluid path to reduce the power losses associated with fluid friction. The design location utilizes the active flow path for motor cooling, whereby the mechanism of Taylor vortices is engineered to carry the heat along the outer diameter of the upper flywheel into the cooling circuit. The second flywheel is located at the lower non-hydraulic end as part of the thrust runner assembly.
Both flywheels are designed in a manner to hermetically seal the high-density tungsten alloy segments. They are helium leak-tested, and subjected to low-speed balance corrections at over-speed.
Pressure boundary
The RCP casing nozzles are welded directly to the reactor system steam generator and piping, which makes the RCP casing part of the reactor primary fluid pressure boundary. The motor housing structure is also a part of the reactor primary fluid pressure boundary, and consists of the stator shell assembly. The stator can provide a fluid barrier to the electrical windings. The stator shell, closures, and power terminal glands are designed for primary pressure. In conjunction with the stator can and back-up sleeves, the closure hermetically seals the motor winding cavity to prevent the primary fluid from wetting the motor stator windings.
Seal design
There are several locations within the AP1000 RCP where close-running clearances between the rotating components and the stationary components are necessary to control fluid flows. The interface locations for controlling the fluid flow are as follows:
- At the impeller upper and lower seal location, seals limit the amount of fluid that passes through
- At the thermal barrier to the rotating shaft seal location, the seal limits the amount of fluid that passes through this shaft interface to limit the bearing water temperature
- At the other locations within the motor cavity, seals are established to control the internal circulation flows through and around the various bearing assemblies
In addition to sizing the seals for proper fluid control functions, seal design incorporates a tolerance to control the radial clearance to avoid rubbing contact that would lead to changes in the seal geometry. The seals are optimized to minimize the leakage flow rates and provide a large-enough clearance to avoid contact wear.
Testing
EMD has established a hydraulic screening facility (HSF) to provide a low-pressure, low-temperature water test loop for evaluation of scaled model hydraulics. Scaled model testing in both air and water was performed via a technique that has been used by EMD to evaluate pump designs and performance characteristics for a variety of commercial nuclear applications. The HSF, along with suitable test components and instrumentation, allows the performance characteristics and hydraulic thrust loads to be estimated in an expeditious manner prior to fabrication of the full-scale prototype hydraulics. The AP1000 RCP hydraulics were tested in the HSF to obtain design performance prior to component manufacture, which provided valuable engineering data prior to full-scale prototype testing. In addition, scaled testing was performed to obtain homologous characteristics to support the reactor system design for reactor control and flow design.
Lead unit and production testing
The AP1000 RCP full-scale lead unit testing has been successfully completed. The test program verified the hydraulic, electrical and coast down performance of the RCP. In addition, EMD performed special engineering tests to acquire data for design and analytical verification. The testing programme involved a series of test and inspection cycles leading to confirmation of the finalized design.
The final design was tested for numerous service cycles, and hundreds of hours at hot operational conditions.
Each RCP manufactured will undergo a production test prior to shipment for installation. Testing consists of hydraulic, electrical and coast-down tests, as well as two service cycles and 50 hot operational hours. During these production tests, the RCP is bolted into a factory test casing that is part of a full-scale test loop that is fully-instrumented to obtain all necessary pump operational data.
The AP1000 Reactor Coolant Pump is a prime example of EMD’s commitment to quality and reliability.
This article was originally published in the December 2012 issue of Nuclear Engineering International magazine.
Author Info:
Robert Ladefian, EMD Power Business Segment Engineering Manager, Curtiss-Wright Flow Control, telephone: +1 724-275-5563
AP1000 is a registered trademark of Westinghouse Electric Company, LLC.
Related ArticlesSuccessful testing of AP1000 reactor coolant pumps Sanmen RCPs to be shipped by June