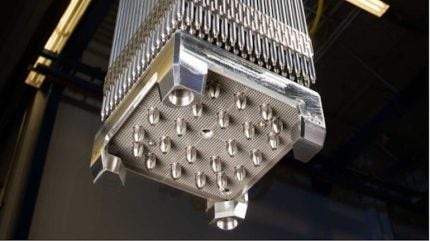
Framatome has installed 3D-printed fuel components at unit 4 of the Ringhals NPP operated by Vattenfall in Sweden. The project, which began in September 2024 aims to confirm the integrity of anti-debris filters manufactured using 3D-printing under real conditions. It is part of a multi-year irradiation programme. The components will undergo annual visual inspections during the plant’s planned outages and reactor refuelling operations.
Anti-debris filters are installed at the base of the fuel assemblies and play a key role in trapping debris in the reactor coolant, protecting fuel rods from damage. In conventional manufacturing, these components are obtained by electro-chemical machining. Additive manufacturing streamlines the manufacturing process and increases design options for enhanced functionality and improved performance.
“This marks a new major step forward in the use of additive manufacturing for strategic applications in the nuclear industry,” said Lionel Gaiffe, Senior Executive Vice President of Fuel Business Unit at Framatome. “We have already achieved promising results with 3D-printed fuel components in operating reactors, and we are committed to the qualification and industrialisation of this revolutionary innovation in the generation of safe, reliable low-carbon energy for long term operations”.
Framatome said it is committed to fully leveraging the potential of additive manufacturing to develop increasingly advanced and innovative components for the nuclear industry. As part of this strategy, the company will produce these filters in-house by 2026 at its new Additive Manufacturing dedicated facility in Romans-sur-Isère (France). This underscores Framatome’s commitment to making additive manufacturing a central pillar of its operations, with a view to strengthening supply chain security and fostering innovation in nuclear component design.
Framatome began to introduce additive manufacturing to nuclear fuel in 2015, focusing on stainless steel and nickel-based alloy fuel assembly components. Framatome fuel experts in France, Germany and the US developed this technology in close collaboration with customers worldwide. In 2021, a 3D-printed stainless steel fuel assembly channel fastener was loaded into the Tennessee Valley Authority’s (TVA) Browns Ferry boiling water reactor in the US and in 2022, 3D-printed stainless steel fuel assemblies upper tie plate grids were inserted into Vattenfall’s Forsmark boiling water reactor in Sweden.