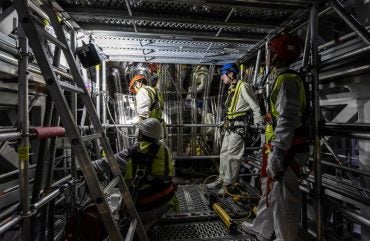
The latest report from the ITER Organisation says the “abundance of lessons learned” from repairing a defective component at the International Thermonuclear Experimental Reactor (ITER), under construction in France, will reduce the time needed for assembly work going forward.
In January 2023, ITER carried out “the most delicate handling operation it had ever performed” – the removal of vacuum vessel sector module #6, which had been installed in the tokamak pit two years previously. The extraction and subsequent disassembly of this giant component, a modular assembly “as tall as a five-storey building and as heavy as three fully loaded jumbo jets”, was required to correct non-conformities identified in two of its sub-components. These were dimensional deviations on the sector’s interfacing surfaces (the bevels) and through-wall cracks in thermal shield cooling pipes which needed to be repaired outside the tokamak pit.
The four-day-long “reverse lift,” followed by a painstaking disassembly process that lasted approximately six months, provided ITER with “a treasure trove of experience” that will eventually “divide by a factor two and a half to three the assembly time required for each of the nine modules of the ITER vacuum vessel”.
Sector module #6, which was extracted from the tokamak pit in July 2023, is now in the last stages of repair, with one side already completed and the other to be finalised shortly.
Assembling sector module #6 was a first-of-a-kind operation involving first-of-a-kind components as was the disassembly process once the module had been extracted from the tokamak pit and placed inside one of the sector sub-assembly tools. A sector module is made up of one vacuum vessel sector and corresponding thermal shield panels, plus two toroidal field coils. Nine 40-degree modules, once assembled and welded together, form the doughnut-shaped plasma chamber.
“We learned a tremendous lot throughout both operations, especially when we began disassembling the module,” said Sergio Orlandi, head of ITER’s Construction Project. “In fact, disassembly is the best method to improve assembly procedures and generate more robust processes.”
The lessons learned extend well beyond the components themselves and are not exclusively technical. “There was a lot to be desired for instance in overhead crane performance – the real bottleneck of sector module assembly,” according to Orlandi. “We invested a lot of money in maintenance, rationalised the tool’s management, replaced faulty sensors and improved the overall performance of the instrumentation and control systems.”
When assembling sector module #6 the first time, days were spent on the step-by-step approval procedures of technical documents such as the engineering and construction work packages transmitted to the contractors. This time, a new consortium (CNPE) is in charge and a different, more efficient approach has been implemented for present and future assembly operations. The CNPE Consortium comprises China Nuclear Power Engineering; China Nuclear Industry 23 Construction Company Ltd; Southwestern Institute of Physics; Institute of Plasma Physics, Chinese Academy of Sciences ASIPP; and Framatome.
“Now the documents are ready at the moment we sign the contract,” said Orlandi. “The work scope is clearly defined and comes with a firm price – that is a major difference. As assembly progresses, we only need the approval of the company that certifies nuclear. That’s an important change-generating value. We are cutting down on dead time to be more efficient and improve quality.”
Assembly operations on sector module #7 began in September 2024 and should be completed in the first quarter of 2025. This will be a seven-and-a-half month process compared with the 18 months spent on the initial assembly of sector module #6.
Another area where time-saving measures have been implemented is metrology. Metrology is used to verify the as-built configuration of a component as well as the alignment of interfacing elements, data that is then used as input in deciding the reverse engineering of shims that fit into the gaps of two adjacent surfaces. “Metrology was also taking a lot of time: surveys were implemented by different companies under different responsibility levels and the results were not always aligned. Here too we have rationalised the approach so that metrology is now done by the ITER Organisation exclusively. We have acquired a much better understanding and command of the global complexity and the input data necessary for engineering applications.”
Orlandi is convinced that the new methods and procedures, the improved organisation, the dependability and performance of the upgraded tools and, above all, collective determination will allow the teams to complete the ongoing assembly of sector module #7 in the first quarter 2025. “We aim to do even better for the re-assembly of sector module #6, which we plan to achieve in six months.” Every module assembly will now have to comply to Orlandí’s challenging six-month objective. “We have a rigid and very challenging time schedule,” he concluded, “and the stakes are very high.”