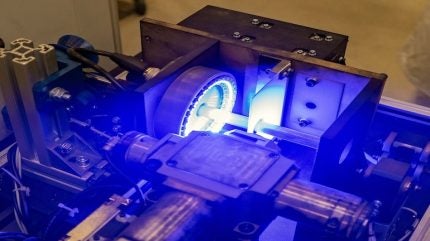
Russia’s Chepetsk Mechanical Plant (ChMZ – Chepetskii Mekhanicheskii Zavod) in the Udmurt Republic, part of Rosatom’s Fuel Division, has introduced an automated complex that uses neural networks to monitor zirconium shells (pipe blanks) for RBMK reactors. This ensures the most stringent requirements for product quality are met.
Using video control at a speed of 150 frames per second, the system captures the image of zirconium shells and determines potential defects, and neural network algorithms compare them with an extensive database. To train the neural network during several years, an extensive database of images of defects of various types was collected. Currently, it contains several thousand images. When a defect is detected, the product is sent to an automated electronic microscope, where high-precision measurements of the depth or height of the defects are carried out by interferometry to compare them with the permissible values. In addition, the straightness of the shell is controlled using a system of shadow optoelectronic sensors. As a result, the system decides on the quality of the outer surface of the pipes.
The complex was created specifically for the Chepetsk Mechanical Plant by the Siberian Branch of the Russian Academy of Sciences in Novosibirsk. The overall control system of the complex was developed and manufactured by the subsidiary of the plant, Pribor-Service.
“Neural networks combined with high-resolution optical systems will completely eliminate the influence of the subjective human factor when evaluating the appearance of products,” said Sergey Chineykin, General Director of ChMZ. “Automated control is another step towards the perfect quality of zirconium shells, which, in turn, guarantees the reliability of Russian fuel for nuclear power plants. Our plans are to introduce similar quality control technologies not only into the production of RBMK fuel shells, but also into the manufacturing process of products for all other types of reactors produced by our plant.”