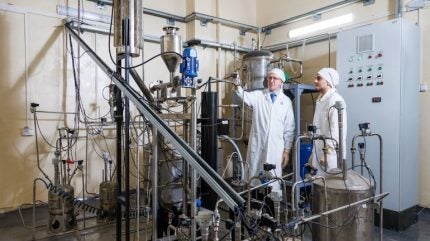
Research is now underway to develop new technologies for the reprocessing facility planned as part of the Experimental Demonstration Energy Complex (ODEK – Opitno Demonstratsionovo Energo-Kompleksa), being built at the Siberian Chemical Combine (SCC) in Seversk under the Breakthrough (Proryv) strategic industry project intended to demonstrate closed fuel cycle technology. ODEK includes three unique facilities: a module for fabrication and refabrication (MFR-YaT – Modulya po Fabrikatsii/Refabrikatsii Yadernovo Tolpliva) of mixed nitride uranium (MNUP) fuel, a 300 MWe Brest-300 lead-cooled fast reactor, and a module for reprocessing and recycling irradiated fuel.
The MFR began pilot operation in January. Brest (Bistrii Reaktor Estestvennoi-bezopasnosti co Svinstovim Teplonositelem – Fast Natural-safety Reactor with Lead Coolant) is a Generation IV 300 MWe power unit nearing completion and scheduled to begin operation in 2027. The module for reprocessing irradiated fuel from Brest is planned to begin construction in 2025-2026 for commissioning in 2030.
MNUP fuel is based on two key components – depleted uranium, which is a by-product of uranium enrichment for nuclear reactors, and plutonium, extracted from irradiated nuclear fuel. A new crystallisation refining technology will be used at the ODEK reprocessing module. Materials extracted from the used fuel, after processing, will be sent for refabrication and recycling to produce of fresh fuel.
The technology for reprocessing Brest fuel will be largely automated. Some stages, such as dissolution, extraction and cleaning, are already well mastered by industry and used during the processing of fuel of existing reactors. But there are a number of innovative technologies that need to be developed. In order to transfer these from the laboratory to experimental and industrial development, specialists Russia’s AA Bochvar Research Institute of Inorganic Materials (VNIINM -Visokotechnologicheskii Nauchno Issledovatelskii Niorganicheskikh Materiolov) have developed a research stand. VNIINM (part of Rosatom’s TVEL fuel company) is collaborating with the Proryv design section on this project.
The stand consists of an electrochemical dissolution apparatus, a crystalliser, an installation for microwave distribution and a robotics complex (RTK – RobotoTekhnicheskovo Kompleksa).
“At the stand, we must demonstrate the performance of three processes in conjunction,” explains Konstantin Tvuglazov, a leading researcher at VNIINM. “All continuous settings are fully automated and designed to be controlled remotely. Repair and periodic maintenance is undertaken using RTK.”
Experiments will be conducted with uranium-containing simulators. This year, the institute will test each installation separately and select the optimal operating modes. Next year, a comprehensive experiment is planned in which all three installations and RTK will work together continuously.
To extract nuclear materials from traditional uranium fuel, chemical dissolution is enough. However, for uranium plutonium fuel, an additional, electrochemical stage is needed.
“In fact, we leach nuclear materials, in particular plutonium, from residues that are formed during chemical dissolution,” said Konstantin Dvoeglazov. “Either a pulp containing solid plutonium compounds or a powder of plutonium dioxide is loaded into the device with a screw dispenser. They are mixed in a certain proportion with nitric acid and a divalent silver catalyst. An electric current is turned on, and the process starts.”
The experimental stand is scaled at a tenth of the size of the planned complex. VNIINM is working with simulators of nuclear materials and last year the device conducted its first series of experiments. The main equipment has been mounted and tested but it remains to equip the operator’s workplace in the next room and check the gas treatment system in operating mode.
The solution of uranium obtained at the earlier stage of the process is steamed, turned into a thick melt and enters the crystalliser, which is a column filled with a solution of nitric acid. “In fact, this is a small diameter pipe,” says Elizaveta Filimonova, a senior researcher at VNIINM. “There is another pipe around it, divided into sections – jackets. Heat carriers with different temperatures circulate through the jackets. This is how we organise the temperature profile of crystallisation. The initial solution is hot at about 70° C. We need to gradually cool it to a crystallisation temperature of just below zero.”
At the bottom of the column, the crystals meet a washing stream of nitric acid. The crystallisation apparatus at VNIINM is experimental and industrial and it can purify 30 tonnes of uranyl nitrate a year from fission products. The plant is designed to produce actinide oxides either directly from their nitric acid solutions or from crystals of hexavalent actinide nitrates. There are three zones for this purpose, which are continuously supplied with microwave radiation.
“In the first zone, the solution evaporates. In the second, denitration occurs, that is, the conversion of uranyl nitrate to uranium oxide,” said Dvoeglazov. ”The third involves calcination at a temperature of 600-700° C in an argon-hydrogen mixture.” The final product of the processing is uranium dioxide. It is unloaded into receiving containers. The robot detaches the filled containers and puts them on a rack. After sampling and analysis, the dioxide can then be used for fuel refabrication.