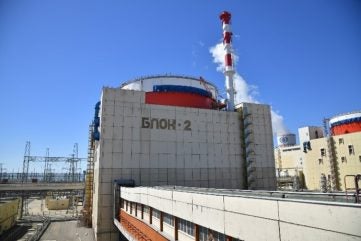
At unit 2 of Russia’s Rostov NPP, a new generation of accident tolerant fuel (ATF) has begun its third cycle of pilot operation. Fuel assemblies with experimental fuel elements are being tested according to the standard nuclear fuel operating cycle for Russian VVER-1000 reactors – three fuel campaigns of 18 months each. During the next scheduled maintenance at the power unit in spring of 2026, the fuel will be unloaded from the reactor core, and will undergo post-reactor examination.
The third 18-month cycle, like the entire ATF fuel pilot operation programme is carried out in strict coordination with regulator Rostekhnadzor based on required justifications and in accordance with the issued licence.
In 2021, three combined fuel assemblies of the TVS-2M design were loaded into the reactor core for the first time, each containing 12 fuel rods of an innovative design. Six fuel elements are made using chromium-nickel alloy 42ХНМ as a structural material, and six with cladding made of zirconium alloy with chromium coating. This makes it possible to either completely eliminate or significantly slow down the development of the zirconium-steam reaction in the reactor core in the event of an emergency.
The next, final step for qualifying Russian ATF fuel will be the loading into a reactor of several fuel cassettes containing 312 innovative fuel rods. At the Chepetsk Mechanical Plant in Glazov (part of Rosatom’s fuel company TVEL) a production site has been established for applying chromium coatings to cladding made of a traditional zirconium alloy. A pilot batch of chrome-plated fuel rod cladding has already been manufactured and accepted.
This is fully consistent with world practice in the development and implementation of innovative nuclear fuel, whereby the first few experimental fuel rods are loaded into the reactor (lead test rods) followed by several assemblies consisting entirely of the innovative fuel rods (lead test assemblies).
“The ATF development programme has produced another important result. It turned out that chrome cladding can provide the missing technological link for creating a completely unmanned automated production of fifth-generation VVER fuel – the TVS-5 design. This fuel for VVER-1200 reactors is specially designed so that, during its assembly it avoids a number of technological operations that are not automated and still involve personnel,” said Alexander Ugryumov, Senior Vice President for Scientific & Technical Activities at TVEL. “Similar to the fabrication of fuel for fast breeder reactors, unmanned industrial production is necessary to close the nuclear fuel cycle for standard thermal light water reactors. This provides an opportunity to use as fuel not only enriched uranium, but also materials extracted from irradiated fuel – regenerated uranium and plutonium.”
Researched and written by Judith Perera